Muffle furnaces are extensively utilized in laboratories and industrial settings for high-temperature applications. They provide precise and uniform heating, making them essential for material testing, sintering, ashing, and other heat treatment processes. If you are looking to understand the muffle furnace working principle, this guide will provide detailed insights.
What Is a Muffle Furnace?
A muffle furnace is a type of high-temperature furnace designed to isolate the material being processed from direct contact with heating elements. It uses a refractory chamber (muffle) to create a controlled environment where samples can be heated at high temperatures without contamination.
Key Features of a Muffle Furnace:
- High Temperature Capability: The temperature of a muffle furnace typically ranges from 1200°C to 1700°C, depending on the model
- Heating Coil Technology: Advanced heating elements, such as silicon carbide, molybdenum disilicide (MoSi2), or Kanthal wire, ensure efficient and uniform heating
- Compact & Insulated Design: The chamber is well insulated to retain heat and improve energy efficiency
- Digital Temperature Control: Modern muffle furnaces come with programmable temperature settings for precision
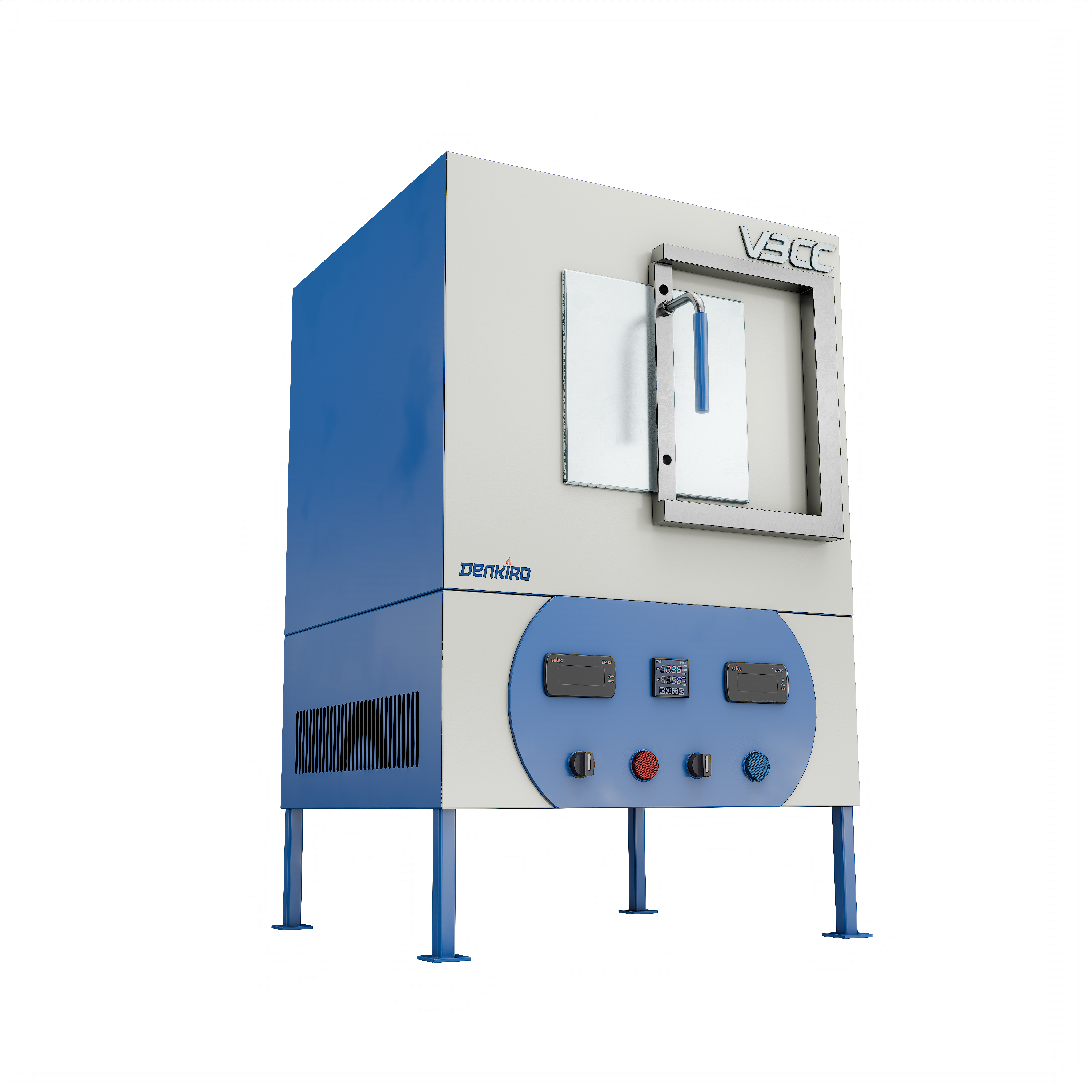
Muffle Furnace Working Principle
The muffle furnace working principle is based on indirect heating. Unlike conventional furnaces where the material is in direct contact with the heating element, a muffle furnace has a separate chamber that shields the sample from combustion gases and contaminants.
Step-by-Step Working Mechanism:
- Powering the Furnace: When the furnace is switched on, the heating coil inside the refractory chamber starts to heat up
- Heat Transfer: The heat generated by the coil is evenly distributed within the insulated chamber, maintaining a consistent temperature
- Sample Heating: The material inside the chamber absorbs heat, gradually reaching the desired processing temperature
- Temperature Control: Advanced temperature controllers regulate the heating process, ensuring precision and preventing overheating
- Cooling Phase: After the process is complete, the furnace cools down before the samples are removed
Applications of Muffle Furnaces
Muffle furnaces serve a broad range of industries, such as:
- Metallurgy: Used for processes like heat treatment, annealing, and metal hardening
- Ceramics & Glass: Sintering and glazing applications
- Pharmaceuticals & Chemicals: Sample ashing and material testing
- Research & Development: Precise high-temperature experiments
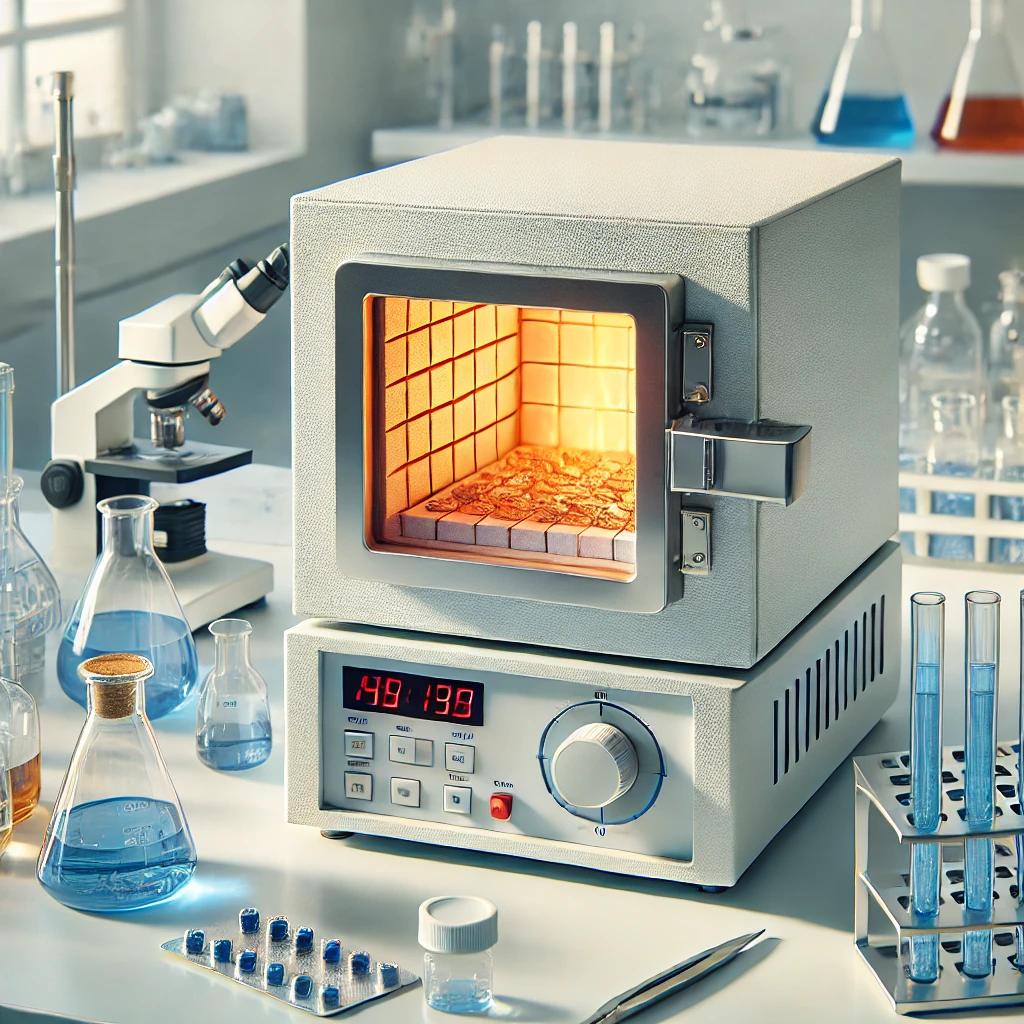
Factors Affecting Muffle Furnace Price
When purchasing a muffle furnace, pricing varies based on several factors:
- Temperature Range: Higher temperature models cost more due to advanced materials
- Size & Capacity: Larger furnaces with higher volume chambers are priced higher
- Heating Element Type: MoSi2 and silicon carbide elements increase durability but also impact the cost
- Control System: Digital programmable controllers add to the price
Choosing the Right Muffle Furnace
Key factors to evaluate when choosing a muffle furnace include:
- Your required temperature range and application
- Energy efficiency and insulation quality
- Access to replacement parts and dependable maintenance services
A muffle furnace is an indispensable tool for laboratories and industries requiring precise high-temperature processing. Understanding the muffle furnace working principle helps in selecting the right model for your needs. If you are exploring options, compare specifications, price, and features from leading muffle furnace manufacturers to make an informed decision.