High-temperature furnaces are essential tools across various industries—from metallurgy and ceramics to electronics and materials science. In these furnaces lies a critical component: the heating element. But what exactly are high-temperature furnace heating elements? How do they work? And which element is best for your application?
This blog brings together key foundational knowledge to guide you through everything you need to know—from types and materials to temperature capabilities and performance considerations.
What Are High-Temperature Furnace Heating Elements?
By applying electrical energy, heating elements produce heat through resistance, a process referred to as Joule heating. In high-temperature furnaces, these elements can reach temperatures of 1600°C to 1800°C or even higher, depending on the material.
They are typically mounted inside the furnace chamber and are responsible for providing uniform, controlled heat to treat or process materials such as metals, ceramics, glass, and more.
How Do High-Temperature Heating Elements Work?
High-temperature heating elements operate by resisting the flow of electric current. When electricity passes through the element, resistance generates heat. A material’s electrical resistivity, thermal conductivity, and melting point all influence its performance.
For reliable and extended use, materials used in heating elements must be capable of withstanding:
- Oxidation
- Thermal cycling (frequent heating and cooling)
- Chemical reactivity with furnace atmospheres
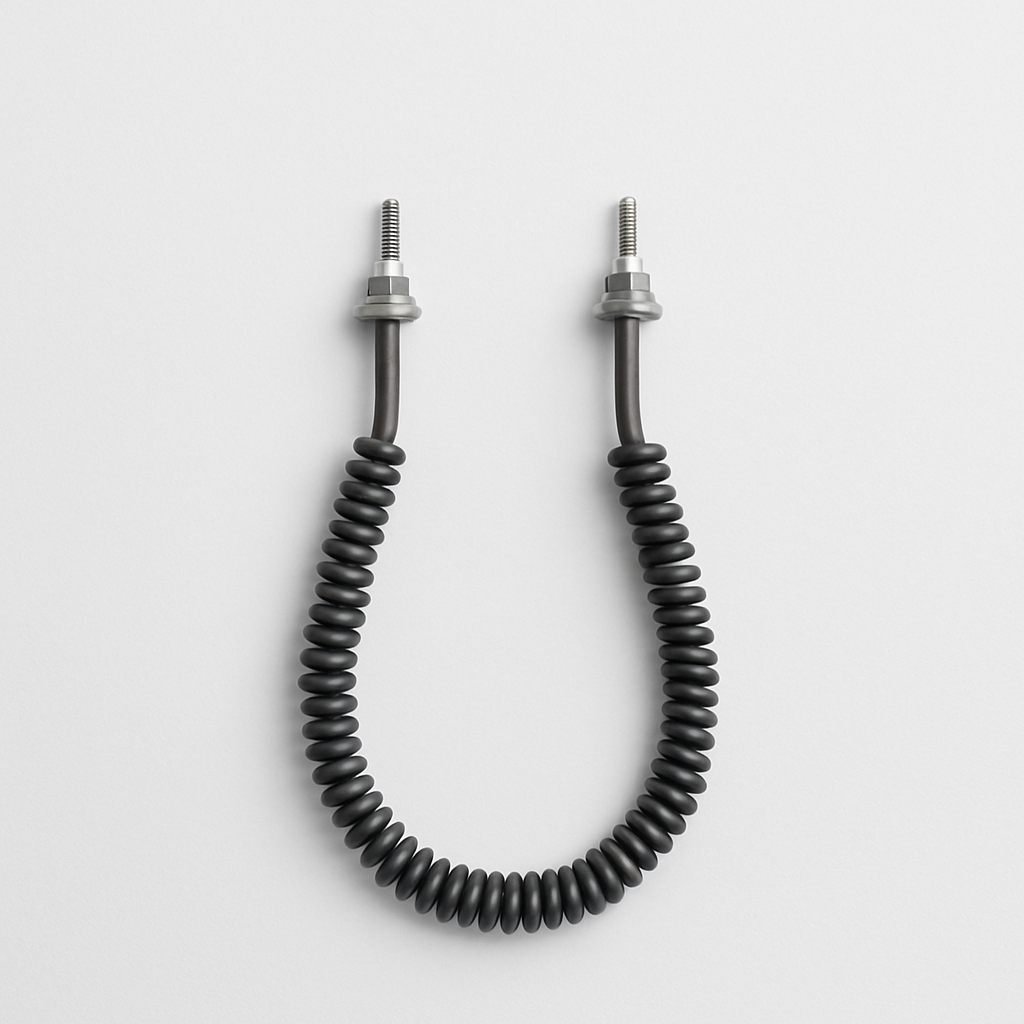
Types of Heating Elements: Which One Is Right for You?
High-temperature furnace heating elements come in various materials, each suited for specific applications based on thermal and chemical properties.
- Silicon Carbide (SiC):
Industrial furnaces often use silicon carbide (SiC) heating elements due to their ability to tolerate temperatures up to 1600°C.They offer good mechanical strength and work well in oxidizing atmospheres. However, they are somewhat brittle and may degrade with repeated thermal cycling. - Molybdenum Disilicide (MoSi₂):
Molybdenum disilicide (MoSi₂) elements are capable of operating at temperatures as high as 1800°C while offering strong resistance to oxidation. They form a protective silica layer that stabilizes them in oxidizing environments. Less brittle than SiC, MoSi₂ is ideal for high-end laboratory and industrial applications. - Kanthal (FeCrAl alloy):
A cost-effective heating element material that performs well in oxidizing environments, Kanthal can withstand temperatures up to 1400°C. While it may not handle extremely high temperatures, it remains a durable choice for standard industrial furnace applications. - Graphite/Carbon:
Capable of operating up to 3000°C, graphite elements are used in inert or vacuum atmospheres only, as they oxidize rapidly in air. They are commonly employed in specialized processes such as high-temperature sintering under controlled conditions.
Choosing the right heating element depends on factors such as required temperature, furnace atmosphere, mechanical durability, thermal cycling, and cost.
Understanding Temperature Ratings
Each type of heating element is engineered to operate within a defined temperature range. Exceeding these limits can cause material degradation, failure, or inconsistent heat distribution.
General Temperature Guide:
- Kanthal (FeCrAl): Up to 1400°C
- SiC: Up to 1600°C
- MoSi₂: Up to 1800°C
- Graphite/Carbon: Up to 3000°C (only in vacuum or inert gas)
Ensure your element choice aligns with both your application temperature and furnace atmosphere.
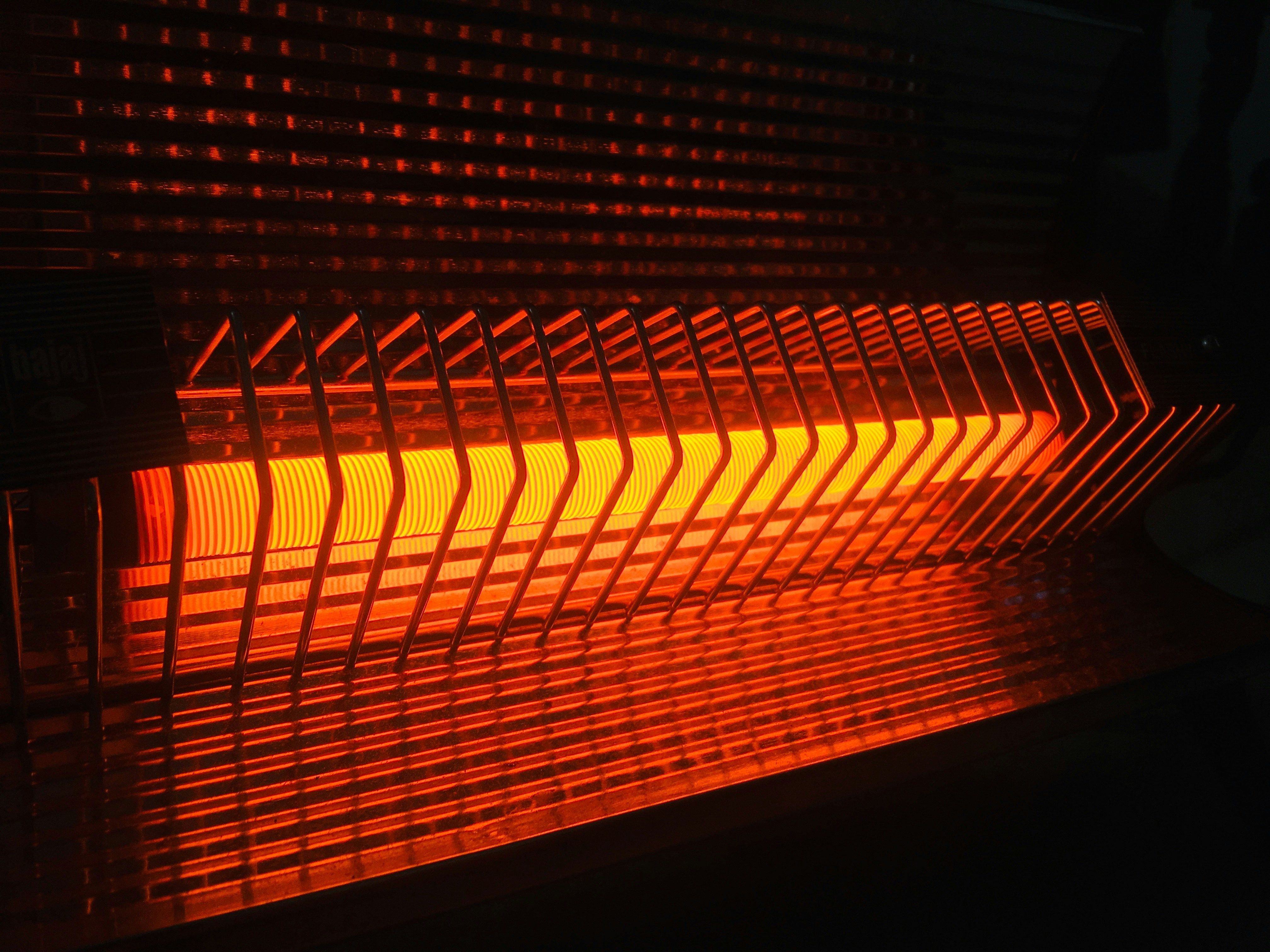
Key Takeaways
- Choose MoSi₂ when your process involves extreme heat and requires materials that withstand oxidizing environments.
- Select silicon carbide (SiC) when moderate to high temperatures are required, along with reliable strength and long-lasting performance.
- Kanthal offers an economical solution for typical applications requiring temperatures under 1400°C.
Additional Heating Element Options for High-Temperature Furnaces
In addition to the common options, other specialized heating elements are used in specific applications:
Tungsten (W):
- Max Temp: 3400°C (in vacuum/inert gas)
- Use: Crystal growing, vacuum furnaces
- Limitation: Cannot be used in air; very brittle
Tantalum (Ta):
- Max Temp:2400°C
- Use: Ultra-high vacuum/inert atmospheres
- Strength: Excellent creep resistance
- Limitation: Expensive; reacts with oxygen
Platinum & Platinum Alloys:
- Max Temp: 1700°C
- Use: Laboratory applications (DTA/DSC, glass melting)
- Strength: Chemically stable in oxidizing environments
- Limitation: Very expensive, sensitive to contamination
Nickel-Chromium (NiCr/Nichrome):
- Max Temp: 1100°C
- Use: Lab ovens, kilns, small furnaces
- Strength: Affordable, stable
- Limitation: Not suitable for aggressive or ultra-high temp environments
Iron-Chromium-Nickel (NiCrFe) Alloys:
- Max Temp: 1200–1250°C
- Use: General-purpose industrial heating
- Strength: Durable, cost-effective
- Limitation: Limited to moderate temperatures
Ceramic-Coated Metallic Elements:
- Description: Metal core with ceramic coating for corrosion resistance
- Use: Harsh environments requiring both chemical and thermal durability
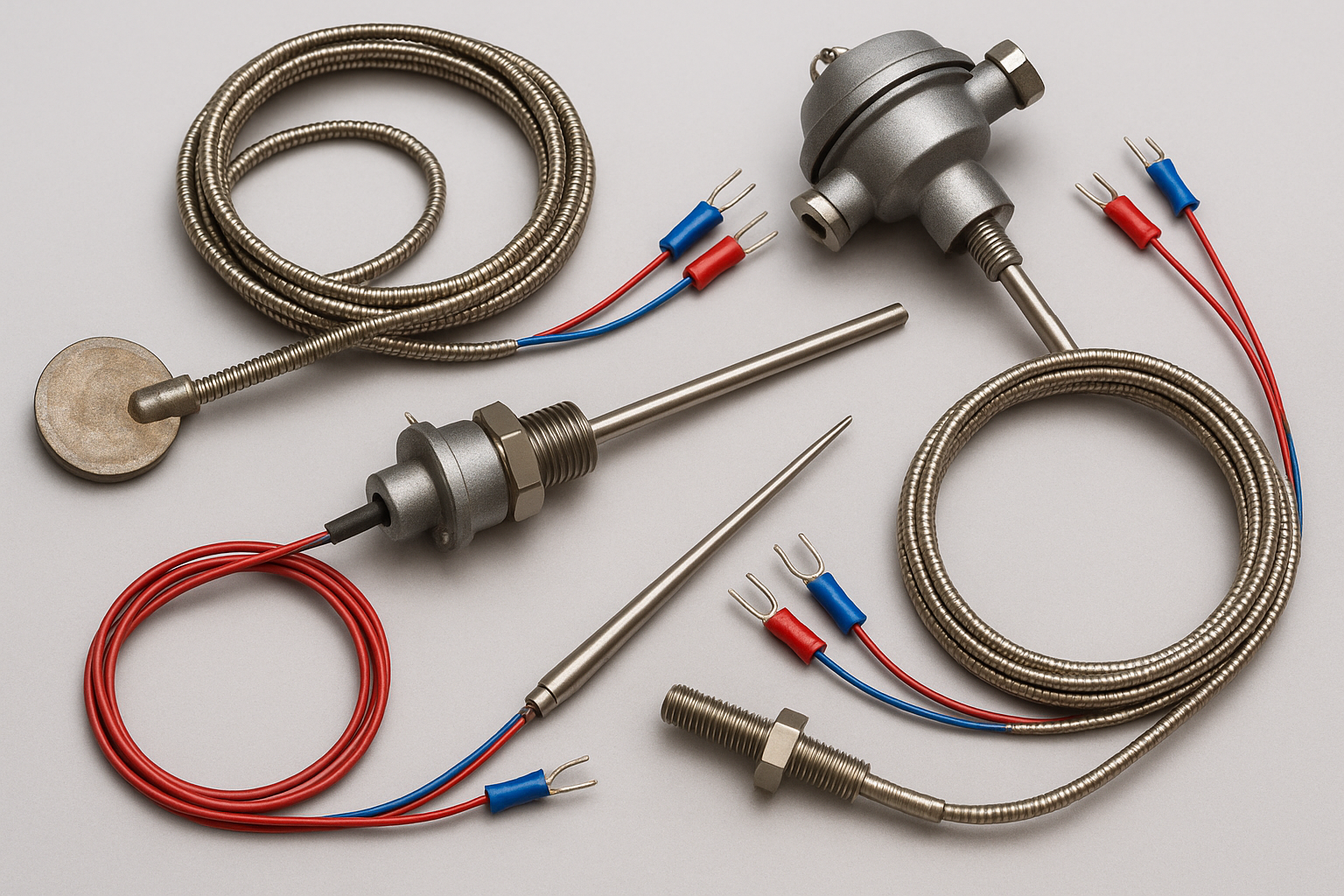
To select the best heating element for high-temperature use, consider these key aspects:
- Operating temperature
- Furnace atmosphere (oxidizing, inert, vacuum)
- Thermal cycling frequency
- Mechanical strength requirements
- Budget and availability
By understanding how heating elements function and how materials behave at high temperatures, you can make informed decisions that lead to longer element life, energy efficiency, and consistent thermal performance in your applications.