Extruders are indispensable tools in material processing, transforming raw materials into uniform profiles with precision and efficiency. From industrial manufacturing to artisanal applications, extruders come in various types to meet diverse needs. Among these, manual, automatic, and vacuum extruders stand out as key categories. Let’s dive into what sets them apart and where they shine.
Manual Extruders
Manual extruders are the simplest and most cost-effective option. They rely on hand or foot power to push material through a die, creating a specific shape. These extruders are typically compact and lightweight, making them portable and easy to use. Designed for versatility, they can handle a range of materials, including clay, polymers, and other malleable substances. Due to their straightforward operation, manual extruders are widely used by hobbyists, artists, and small-scale manufacturers seeking affordable and reliable solutions.
Applications:
- Ceramics and Pottery: Ideal for small-scale operations, such as crafting decorative tiles or intricate clay designs.
- Prototyping: Useful in low-volume production runs where flexibility and precision are essential.
Advantages:
- Affordable and easy to maintain
- Well-suited for handling limited production volumes and personalized projects
- Simple to operate, requiring no electricity or complex setup
Limitations:
- Limited output capacity
- Requires significant manual effort, making it unsuitable for large-scale production
Automatic Extruders
Automatic extruders are powered by electric or hydraulic systems, automating the extrusion process. They offer consistent output with minimal human intervention, making them a popular choice for medium to large-scale operations. These machines are designed to handle a wide variety of materials with precision, ensuring uniformity in shape and size. With programmable settings and advanced features, automatic extruders are perfect for manufacturers seeking efficiency, scalability, and versatility in their production lines.
Applications:
- Industrial Manufacturing: Used for producing large volumes of products like plastic pipes, food products, or pharmaceutical components
- Material Processing: Effective in industries that demand consistent quality and high-speed production
Advantages:
- High throughput and efficiency
- Minimal labour required, reducing operational costs
- Capable of handling a wide range of materials and die shapes
Limitations:
- Higher initial investment compared to manual extruders
- Requires regular maintenance and skilled operators
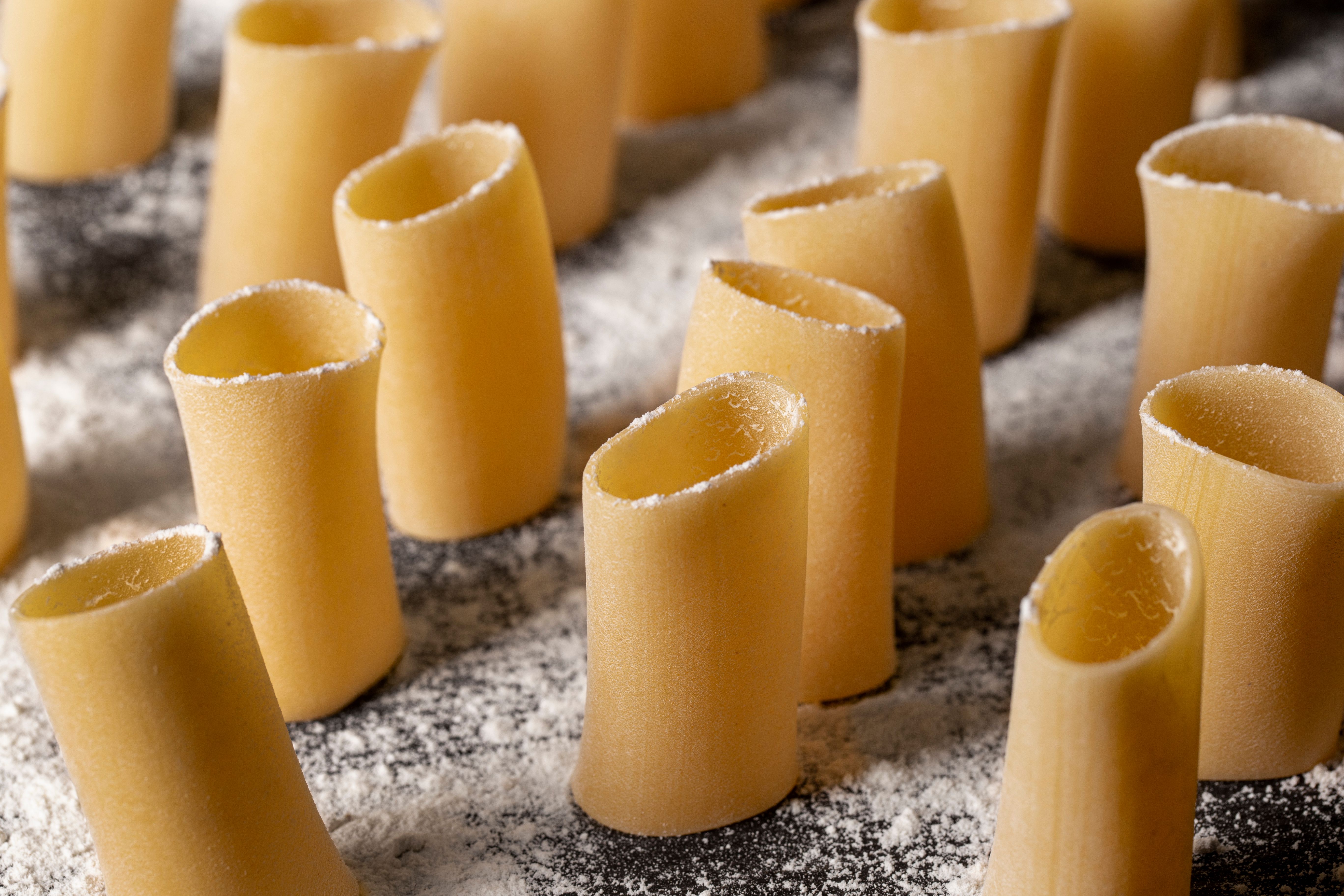
Vacuum Extruders
Vacuum extruders take material processing to the next level by incorporating a vacuum system to remove air pockets from the material. This results in a denser, more uniform output, essential for applications where precision and strength are critical. These extruders are specifically engineered for high-quality production, enabling the creation of defect-free products with exceptional durability. Vacuum extruders are widely used in industries that require meticulous attention to detail, making them indispensable in applications like advanced ceramics, brick manufacturing, and aerospace materials.
Applications:
- Ceramics and Bricks: Commonly used in producing high-quality bricks, tiles, and ceramic components
- Specialized Manufacturing: Ideal for industries where material integrity and consistency are paramount, such as aerospace or advanced ceramics
Advantages:
- Eliminates air pockets, reducing the risk of defects
- Produces stronger, more durable products
- Suitable for complex shapes and fine details
Limitations:
- Expensive to purchase and maintain
- Requires skilled operators and specific infrastructure
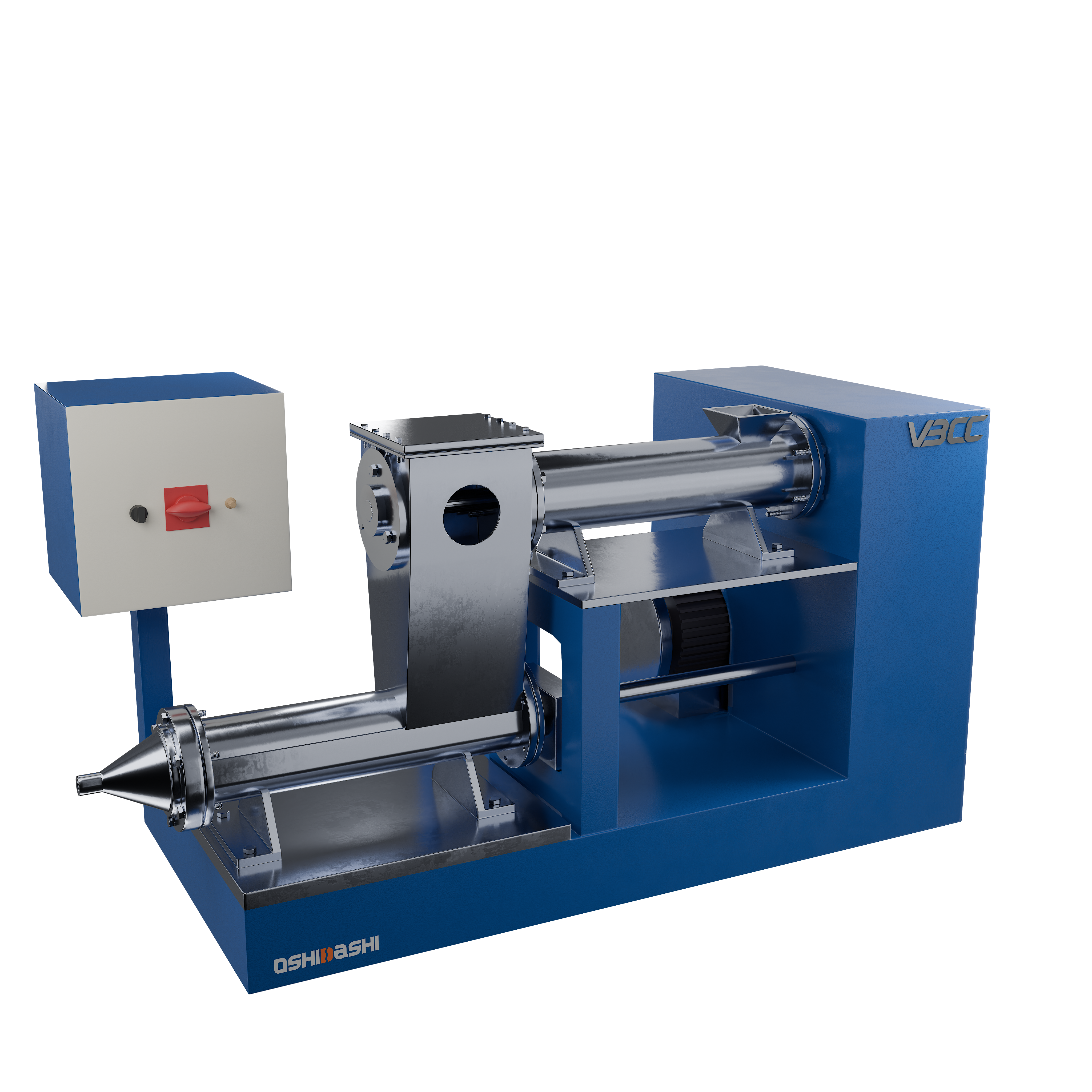
Key Considerations for Choosing Extruders:
- Budget: Assess initial investment costs alongside long-term maintenance and operational expenses
- Production Volume: Match the extruder's output capacity with your production requirements
- Material Properties: Ensure the extruder is compatible with the material's characteristics, such as viscosity, texture, or malleability
- End-Product Requirements: Consider factors like precision, durability, and the complexity of shapes needed for your application
- Infrastructure and Expertise: Account for available space, power supply, and the skill level of your workforce
By aligning these factors with your operational goals, you can choose an extruder that not only meets but exceeds your expectations.
Extruders are a cornerstone of material processing, each type offering unique benefits and capabilities. By understanding their differences, you can make an informed decision that aligns with your operational needs and production goals. Whether you’re crafting custom ceramics, manufacturing industrial components, or pushing the boundaries of advanced materials, there’s an extruder designed to meet your challenges.