Muffle furnaces play a vital role in both laboratory and industrial environments, delivering high-temperature heat for tasks such as material analysis, ashing, thermal treatment, and ceramic fabrication. Choosing the right muffle furnace depends on factors such as temperature range, chamber size, and application requirements. In this blog, we’ll explore the different types of muffle furnaces to help you make an informed decision.
1. Box Muffle Furnaces
Box muffle furnaces are the most common type, featuring a rectangular heating chamber enclosed by insulation. These furnaces are widely used for general laboratory applications such as sample drying, ashing, and material testing. They are available in different temperature ranges, typically between 1000°C and 1800°C, making them versatile for a variety of processes. Many models come with digital controllers for precise temperature management, ensuring accuracy in experimental and industrial setups. Box muffle furnaces are commonly used for various applications where a lab muffle furnace is required.
Ideal for:
- Material testing and heat treatment
- Universities and research laboratories
- General-purpose heating applications
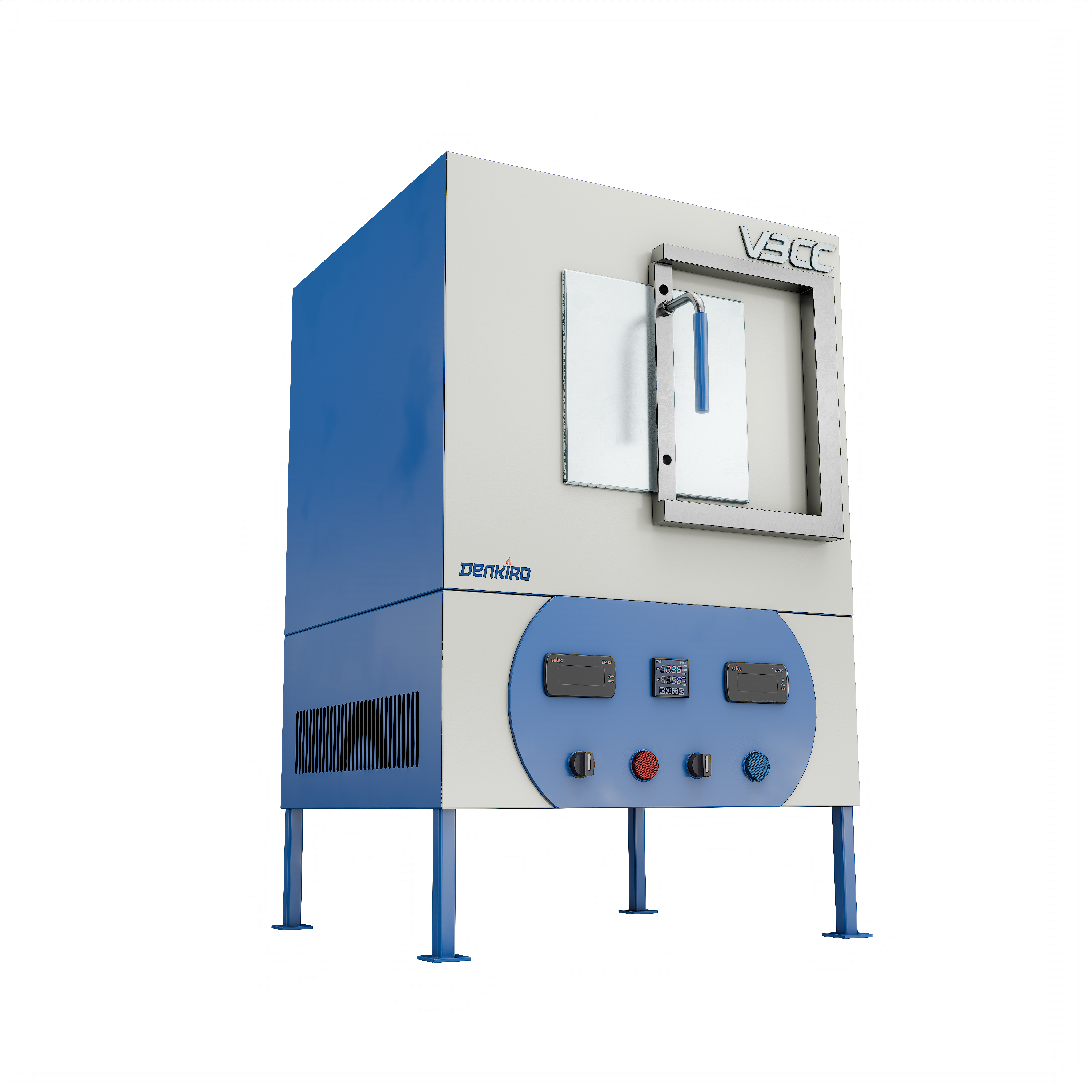
2. Tube Muffle Furnaces
Tube furnaces consist of a cylindrical heating chamber and are designed for continuous processing of samples. They allow controlled atmospheres by passing gases through the tube, making them ideal for chemical synthesis and thermal processing. These furnaces are commonly used in applications requiring uniform heating across the length of a sample, such as catalyst testing, gas-solid reactions, and diffusion studies. They are available in single-zone, multi-zone, and split tube designs to cater to different heating needs. When considering muffle furnace price, tube furnaces tend to be more expensive due to their advanced capabilities.
Ideal for:
- Sintering and annealing
- Controlled atmosphere applications
- Chemical and material research
3. Vacuum Muffle Furnaces
These furnaces operate under reduced pressure or vacuum conditions to prevent oxidation and contamination of samples. They are commonly used in metallurgy, semiconductor processing, and high-purity material production. Vacuum muffle furnaces are essential for applications that demand an oxygen-free environment to ensure material integrity. They typically feature advanced sealing systems, inert gas compatibility, and digital vacuum control for precise atmospheric regulation. A high-temperature muffle furnace with vacuum capability is ideal for specialized industrial applications.
Ideal for:
- Heat treatment of metals
- Semiconductor and electronics industry
- Applications requiring oxidation-free processing
4. Microwave Muffle Furnaces
Microwave furnaces use electromagnetic waves to heat substances, offering quicker processing times and greater energy efficiency. They are particularly useful for ashing, sintering, and drying applications. Microwave muffle furnaces are designed to significantly reduce heating cycles compared to conventional models, improving overall productivity. They also allow selective heating of materials, minimizing thermal damage to sensitive samples. These furnaces are widely used in ceramics, polymer research, and material science laboratories. If you are looking for a muffle furnace used for fast heating cycles, microwave models are a great choice.
Ideal for:
- Fast heating cycles
- Low energy consumption applications
- Ceramic and polymer research
5. High-Temperature Muffle Furnaces
Designed for applications requiring extremely high temperatures (up to 1800°C or more), these furnaces are used in advanced material research, metallurgy, and refractory testing. They are built with high-quality insulation and durable heating elements to withstand extreme thermal conditions while maintaining energy efficiency. High-temperature muffle furnaces are indispensable in the development of new materials, aerospace engineering, and metal processing industries. Many models feature programmable controllers for precise thermal profiles, ensuring repeatability in experimental setups. Crucibles such as alumina and silicon carbide, used in these furnaces, are capable of withstanding extreme thermal stress
Ideal for:
- High-temperature sintering and melting
- Advanced material research
- Aerospace and defence industries
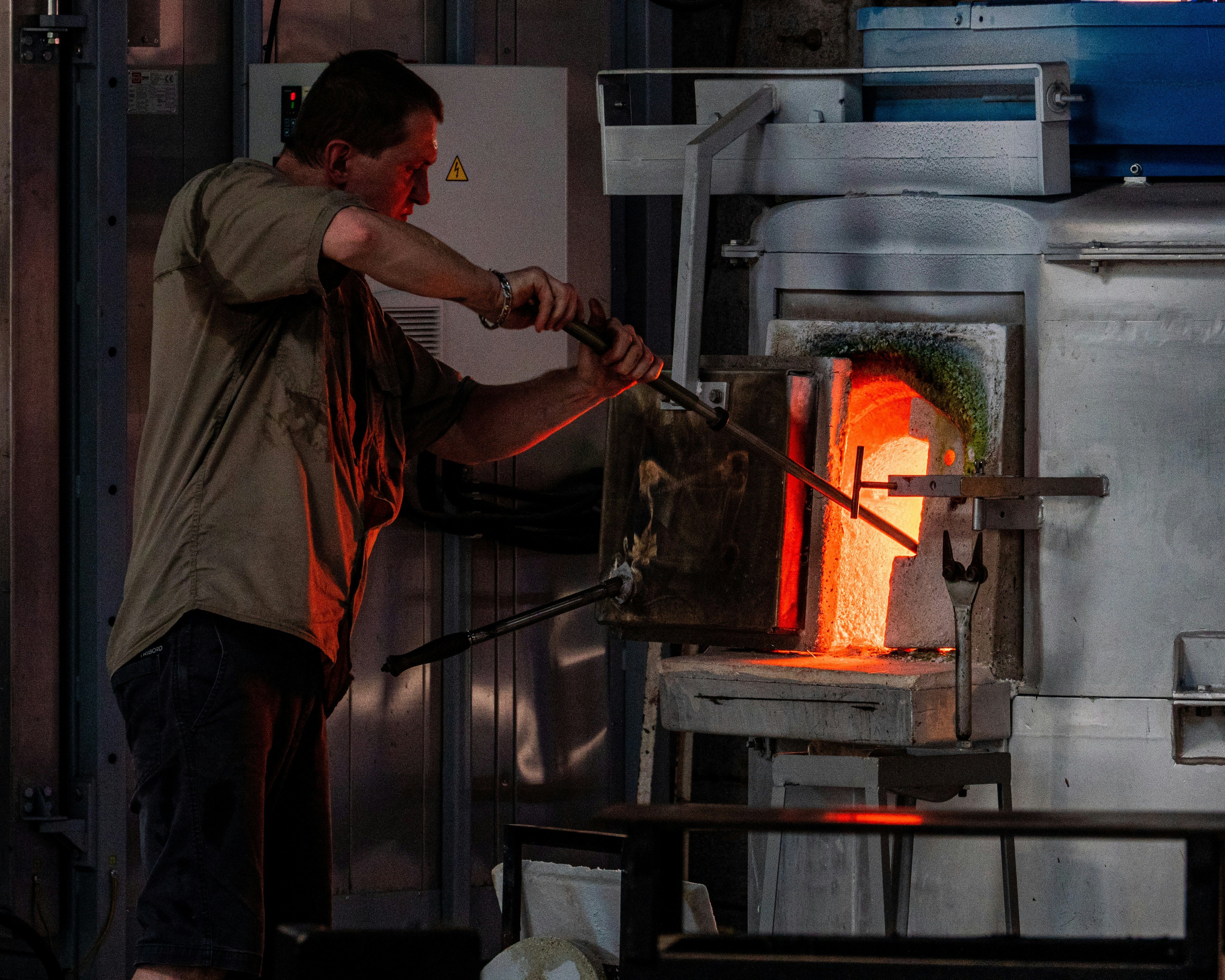
Choosing the Right Muffle Furnace
When selecting a muffle furnace, consider the following factors:
- Temperature Range: Ensure the furnace meets your required operating temperatures
- Chamber Size: Choose an appropriate chamber size based on your sample volume
- Atmosphere Control: If your application requires an inert or vacuum atmosphere, select a compatible model
- Heating Rate & Energy Efficiency: Fast heating cycles and energy efficiency can impact operational costs
- Application-Specific Needs: Match the furnace type with your specific industrial or research needs
Muffle furnaces are available in a range of designs to meet the specific needs of various industries and scientific disciplines. Understanding the specific requirements of your application will help you choose the right furnace for optimal performance and efficiency. Whether you need a general-purpose box furnace or a high-temperature vacuum furnace, investing in the right equipment ensures precision and reliability in your heating processes. If you’re considering a muffle furnace price, compare models based on features, durability, and efficiency.