Plastic extrusion is widely utilized in manufacturing to produce a broad range of plastic parts and products. From pipes and tubing to sheets and films, extrusion plays a vital role in shaping everyday materials. This article walks you through how plastic extrusion works, where it's used, and why it's a valuable manufacturing method.
Understanding Plastic Extrusion
Plastic extrusion is a continuous manufacturing process where raw plastic material, usually in the form of pellets or granules, is melted, shaped, and solidified into a specific form. This technique is ideal for producing long, uniform plastic shapes such as tubes, films, profiles, and piping. The type of extruder used, such as a single screw extruder or a twin-screw extruder, determines the efficiency and precision of the process.
The Plastic Extrusion Process: Step by Step
The plastic extrusion process involves several critical stages that ensure the efficient transformation of raw plastic into finished products. Extruders play a crucial role in each step, determining the quality, durability, and precision of the final output.
1. Material Feeding
The extrusion process begins by loading plastic pellets into a hopper, which gradually feeds them into the system. Commonly used thermoplastics for this method include PVC, polyethylene (PE), polypropylene (PP), and polystyrene (PS).The choice between a single screw extruder and a twin-screw extruder depends on the material type and processing requirements. Single screw extruders are economical and work well with basic, consistent materials, whereas twin-screw extruders provide superior blending and processing control, making them more suitable for intricate or additive-heavy compounds.
2. Melting and Mixing
A rotating screw within the extruder pushes the plastic pellets along the barrel as they begin to melt.
- Heating: The barrel is divided into several heating zones, each designed to progressively raise the temperature and melt the plastic material.
- Compression & Mixing: The screw applies pressure, mixing the molten plastic evenly to remove inconsistencies.
- Shear Action: Friction between the screw and barrel further assists in melting and blending the plastic for a uniform consistency.
3. Shaping the Material
The melted plastic is forced through a die, a specially designed mould that gives the plastic its final shape. The die determines the cross-sectional profile of the extruded product, whether it’s a tube, sheet, or film. Precision in die design is essential to ensure product quality and minimize material waste. This process, also known as extrusion moulding, plays a crucial role in shaping high-quality plastic products.
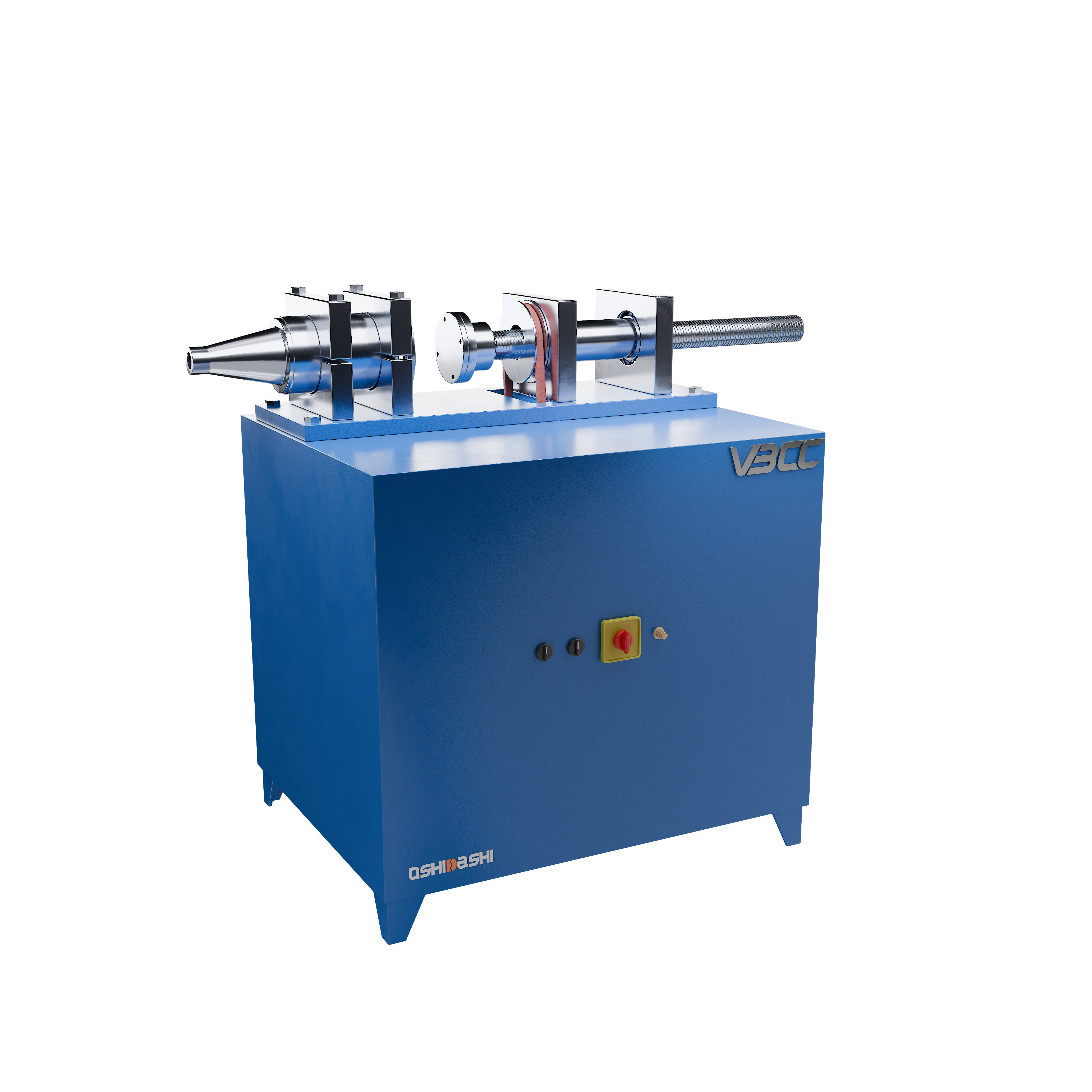
4. Cooling & Solidification
After exiting the die, the hot extruded plastic enters a cooling system, often involving:
- Water baths for rapid cooling and shape retention.
- Air cooling for gradual solidification, which is crucial for certain applications requiring controlled cooling.
- Vacuum Calibration (for specific applications) to maintain tight tolerances and structural integrity.
5. Cutting & Finishing
Once cooled, the extruded plastic is cut into desired lengths or wound into rolls, depending on the application. Additional finishing processes like:
- Trimming to remove excess material.
- Surface treatment for improved durability or aesthetics.
- Printing or coating for branding and functional enhancements.
Applications of Plastic Extrusion
Plastic extrusion finds applications across multiple sectors, such as:
- Construction: PVC pipes, window frames, and insulation materials
- Packaging: Plastic films, wraps, and sheets
- Automotive: Plastic trims, tubing, and protective covers
- Medical: IV tubes and other medical-grade plastic products
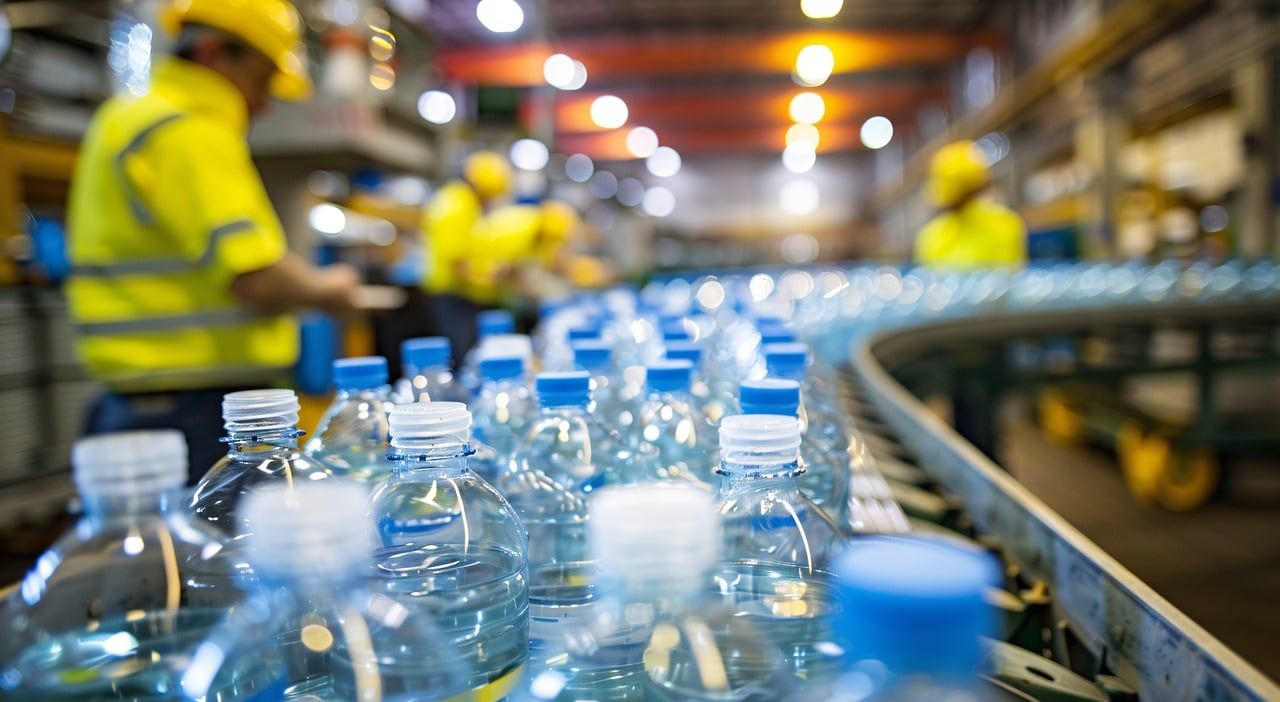
Benefits of Plastic Extrusion
- Cost-Effective: Minimal waste and efficient production make extrusion a budget-friendly process.
- High Efficiency: Continuous manufacturing allows large volumes to be produced quickly.
- Versatility: Can process various thermoplastics into complex shapes.
- Customization: Different dies and additives can create unique product properties.
Plastic extrusion is a highly efficient and versatile manufacturing process that converts raw pellets into functional products used in numerous industries. Whether utilizing a single screw extruder for simple applications or a twin-screw extruder for complex material processing, understanding the extrusion process helps manufacturers optimize quality, reduce costs, and innovate new applications. Extrusion moulding remains a cornerstone of modern plastic production, ensuring durability and precision in manufacturing.