Laboratory furnaces are essential equipment used in various fields, including scientific studies, manufacturing, and experimental work. They are commonly relied upon for tasks like materials analysis, thermal processing, and sintering, where accurate, consistent, and repeatable temperature control is crucial. However, as with any complex equipment, lab furnaces are prone to specific issues—especially under heavy usage or poor maintenance practices.
Whether you're operating a muffle furnace, tube furnace, or chamber furnace, understanding the common problems and how to address them is key to minimizing downtime, ensuring safety, and preserving the integrity of your experiments.
In this in-depth blog post, we’ll explore the most frequent lab furnace issues, their root causes, and detailed troubleshooting solutions.
1. Inaccurate or Fluctuating Temperature Readings
Symptoms:
- The temperature shown on the display differs from the actual internal furnace temperature
- Furnace overshoots or undershoots setpoints
- Irregular thermal cycles
Possible Causes:
- Aging or damaged thermocouples
- Calibration drift over time
- Loose or corroded thermocouple connections
- Faulty temperature controller or internal sensor board issues
- Signal interference caused by nearby electronic devices or unstable electrical sources
Solutions:
- Check and replace the thermocouple: Thermocouples degrade over time, especially at high temperatures. Replace with the correct type (e.g., Type K, R, S) specified by the manufacturer.
- Recalibrate the system: Use a certified reference thermometer to check and calibrate the furnace’s reading.
- Check all wiring and terminals for looseness or corrosion, as these can lead to unstable readings.
- Use shielding or grounding: Ensure proper grounding and consider shielding thermocouple cables to prevent electromagnetic interference.
- Update controller firmware or replace it if there are persistent issues with PID control or display glitches.
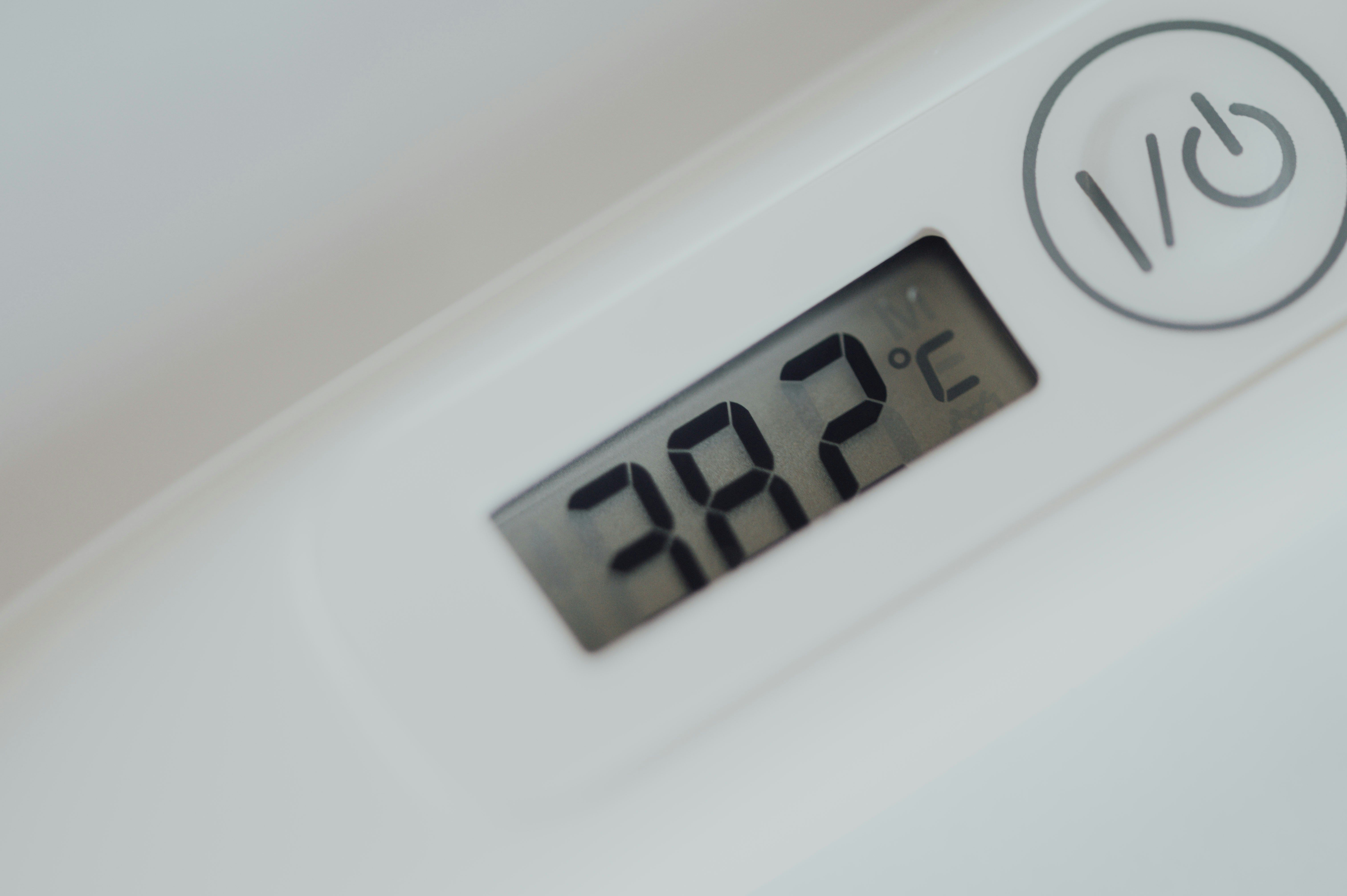
2. Heating Element Failure
Symptoms:
- Furnace fails to heat
- Heats slowly or unevenly
- Visible damage or breakage in elements (especially in exposed-element models)
Possible Causes:
- Heating elements may fail from prolonged use or repeated exposure to high temperatures
- Operating above maximum rated temperature
- Short circuits or power surges
- Accumulated contamination degrading element material
Solutions:
- Perform a visual check and test for continuity to identify cracks, discoloration, or warping. Use a multimeter to measure the electrical resistance of the heating elements.
- Replace damaged elements: Always use manufacturer-recommended replacements to maintain proper watt density and heating profile.
- Install surge protection: Helps prevent element damage from voltage spikes.
- Avoid contaminant exposure: Some materials (e.g., chlorides, sulfur compounds) can corrode elements—use crucibles and clean up residues promptly.
3. Door Seal or Insulation Problems
Symptoms:
- Heat leakage around the furnace door
- Difficulty maintaining high temperatures
- Exterior casing becoming unusually hot
Possible Causes:
- Worn or cracked door gasket/seal
- Warped door due to thermal stress
- Internal insulation breakdown
- Improper door alignment or latch tension
Solutions:
- Inspect the door gasket or fibre seal: Replace if it shows signs of brittleness or cracking.
- Re-align the door: Adjust hinges or latching mechanism to ensure tight closure.
- Check internal insulation: Damaged ceramic fibreboard or firebrick can be replaced sectionally.
- Clean sealing surfaces: Remove debris or residues that could prevent a complete seal.
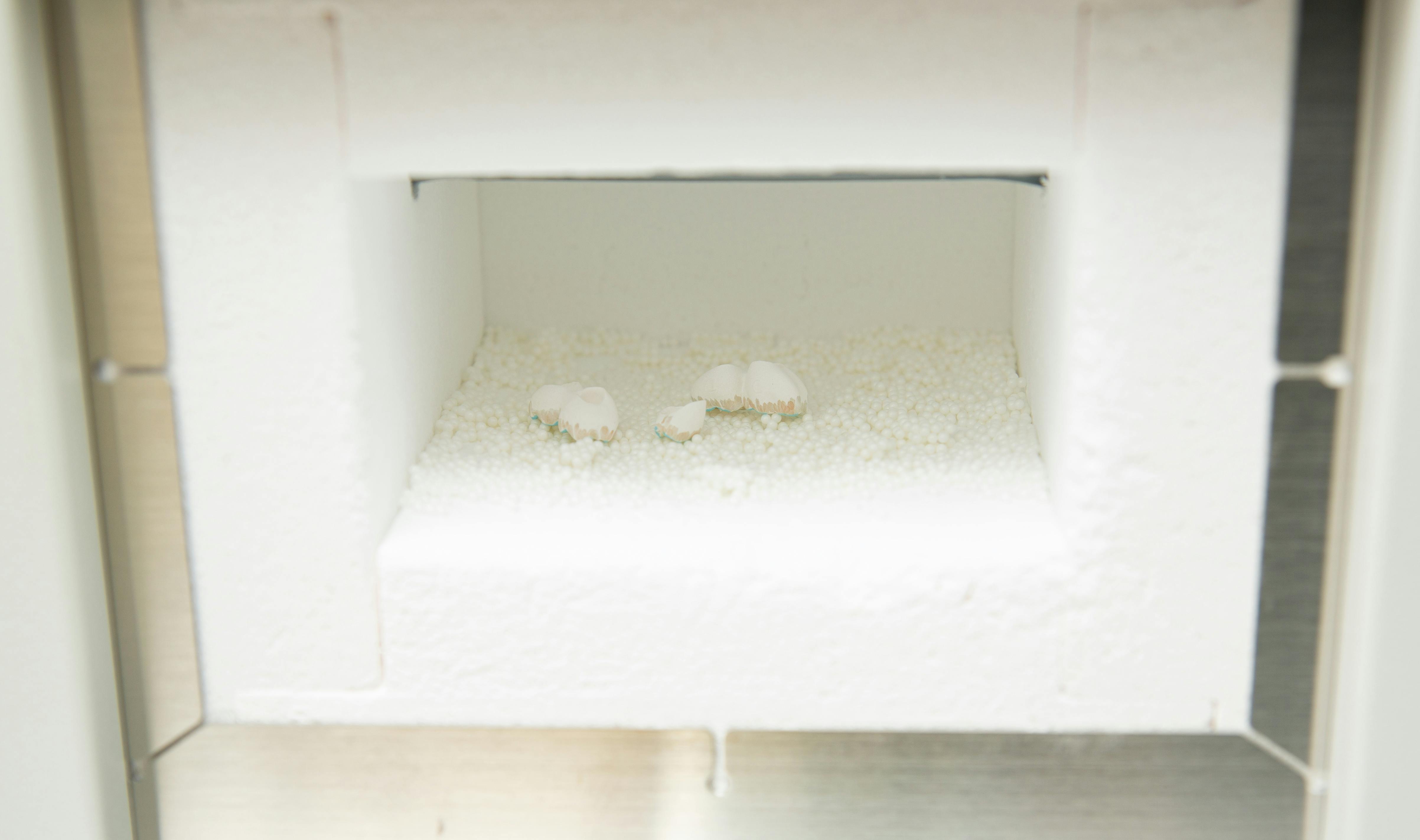
4. Controller or Display Malfunctions
Symptoms:
- Blank or frozen display
- Unresponsive control buttons
- Erroneous error codes or spontaneous resets
- Loss of user-defined programs
Possible Causes:
- Firmware glitches or memory corruption
- Electrical surges or faulty power supply
- Moisture ingress or corrosion inside controller housing
- Defective internal components (e.g., microcontroller, relay boards)
Solutions:
- Reset the controller: Follow the manufacturer’s reset or power-cycle procedure.
- Firmware updates: Check for controller firmware updates from the OEM.
- Backup and restore programs: Many controllers allow settings to be saved externally for easy recovery.
- Replace the controller unit if repeated issues occur, and have a technician verify electrical supply consistency.
5. Uneven Heating or Cold Spots
Symptoms:
- Samples placed in different areas of the chamber show varying results
- Temperature mapping reveals inconsistent heat distribution
- Crucibles not reaching target process temperatures evenly
Possible Causes:
- Aging or partially failed heating elements
- Poor airflow in convection-assisted furnaces
- Compromised insulation or heat leakage
- Uneven loading of materials inside the chamber
Solutions:
- Install new heating elements or adjust their placement, as degraded ones may provide uneven heating.
- Conduct a thermal profile test: Use multiple thermocouples to detect and diagnose hot/cold zones
- Ensure symmetrical loading: Distribute materials evenly and avoid blocking airflow paths.
- Upgrade or service insulation: Heat loss through compromised walls can disrupt uniformity.
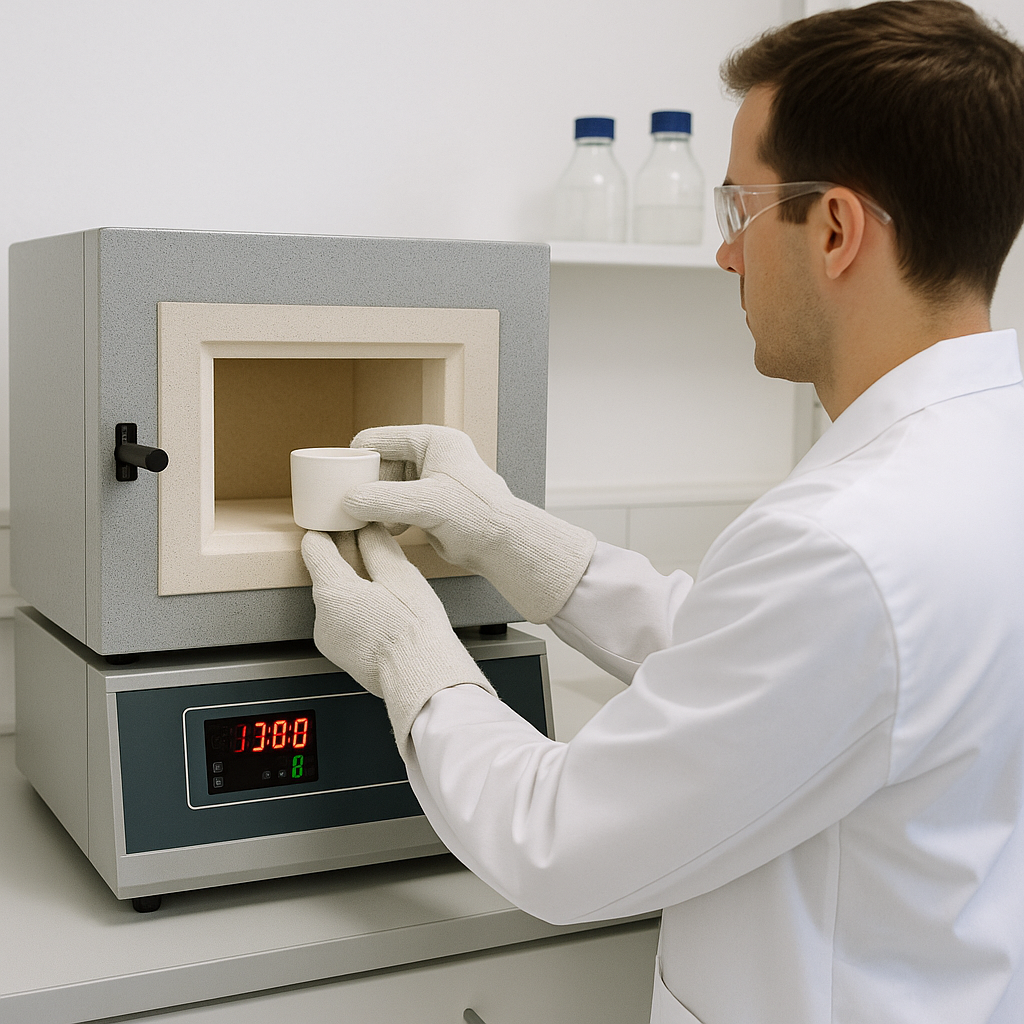
6. Unusual Noises or Burning Smells
Symptoms:
- Buzzing, humming, clicking, or scraping sounds
- Burnt or chemical smell during operation
- Trip hazards or circuit breaker trips
Possible Causes:
- Fan or blower motor issues (in forced-air models)
- Electrical arcing or short circuits
- Material contamination or off-gassing
- Dust or debris igniting at high temperatures
Solutions:
- Shut down immediately if odour or smoke appears.
- Inspect electrical components: Check wiring, relays, contactors, and power supplies.
- Clean chamber thoroughly: Burn off residues during a controlled bake-out if needed.
- Service motorized components and replace worn bearings or misaligned fans.
Preventive Maintenance Best Practices
Preventing furnace problems is always better than troubleshooting them after failure. Here’s a checklist to extend the life of your lab furnace:
Daily:
- ·Visually inspect for damage or residue build-up
- ·Check door seals and latch alignment
Weekly:
- Verify accurate temperature readings with an external probe
- Check for abnormal noises or unexpected smells during operation
Monthly:
- Perform a basic calibration check
- Check heating elements and insulation for any wear, cracks, or other visible issues
Quarterly:
- Test backup power systems (if applicable)
- Clean and inspect controller and electrical terminals
Annually:
- Full system calibration by a certified technician
- Swap out deteriorated parts like gaskets or insulation panels as required
Keeping a maintenance logbook is also recommended for tracking service intervals, replacements, and performance issues.
Lab furnaces are rugged yet sensitive pieces of equipment. Proactively identifying and resolving common issues like temperature inconsistencies, heating element failures, and control panel glitches can ensure smooth operation and reliable results.
With the right knowledge and maintenance practices, you can reduce downtime, improve furnace longevity, and avoid costly equipment replacements.
If you're facing persistent problems or need expert help, don’t hesitate to contact your furnace supplier or service technician. Many issues can be resolved quickly with the proper guidance and parts.