Selecting the right furnace for your laboratory or industrial application is crucial to ensure efficiency, safety, and reliability. Whether you’re conducting material testing, sintering, or heat treatment, the furnace you choose can impact both the quality of your results and the longevity of your equipment. Here’s a guide on key factors to consider when selecting the right furnace for your needs.
1. Determine the Temperature Range
One of the foremost things to do is to determine the temperature range that your furnace will need to achieve. Different applications require different temperature limits.
- Low-temperature applications (e.g., drying, annealing) may require furnaces with a range of 200°C to 500°C.
- High-temperature applications (e.g., sintering, material testing) often demand furnaces capable of reaching temperatures above 1000°C, such as muffle furnaces or tube furnaces.
- For extreme temperatures (up to 2000°C or more), specialized furnaces such as high-temperature furnaces or vacuum furnaces may be necessary
Tip: Be sure to select a furnace with a temperature range that comfortably exceeds the highest temperature you'll need to ensure safe and reliable operation.
2. Furnace Type: Choose Between Muffle, Tube, or Box
Furnace type plays a significant role in the application for which it’s suited.
- Muffle furnaces: Best for sample ashing, sintering, and heat treatment due to their enclosed heating chamber that ensures uniform temperature distribution.
- Tube furnaces: Ideal for material testing and chemical reactions under controlled atmospheres, such as vacuum or inert gas conditions. Tube furnaces can handle smaller, cylindrical sample sizes.
- Box furnaces: Offer a larger chamber for batch processing and are well-suited for heat treatment of bulk materials.
Tip: Assess the type of sample processing you need, as this will influence which furnace type is best. Tube furnaces are great for small-scale, precise testing, while box furnaces are ideal for larger batches.
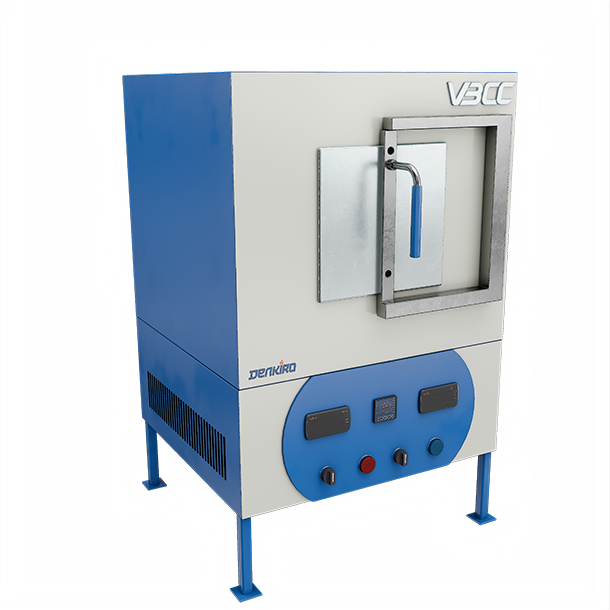
3. Choose Based on Atmosphere Control Requirements
Some applications require precise control over the furnace atmosphere to prevent oxidation or contamination.
- If your application demands a controlled atmosphere (e.g., an inert gas or vacuum), a vacuum furnace or a tube furnace with controlled gas flow might be your best option.
- For high-temperature material processing or chemical reactions, furnaces with atmosphere control features allow you to customize the environment within the furnace chamber
Tip: If your application involves sensitive materials that must be protected from oxidation or other reactions, look for a furnace that can handle specific atmospheric conditions.
4. Material and Chamber Size
Consider the material size and chamber size based on the amount and type of material you will be heating. The chamber should be large enough to fit your samples without overcrowding, which could lead to uneven heating.
- Small laboratories or research applications may require compact, bench-top furnaces with a smaller chamber size.
- Industrial applications that handle larger quantities of materials may need furnaces with larger, more durable chambers.
Tip: Always account for the size of your largest sample or batch, as overloading a furnace can lead to inconsistent heating and even damage to the furnace.
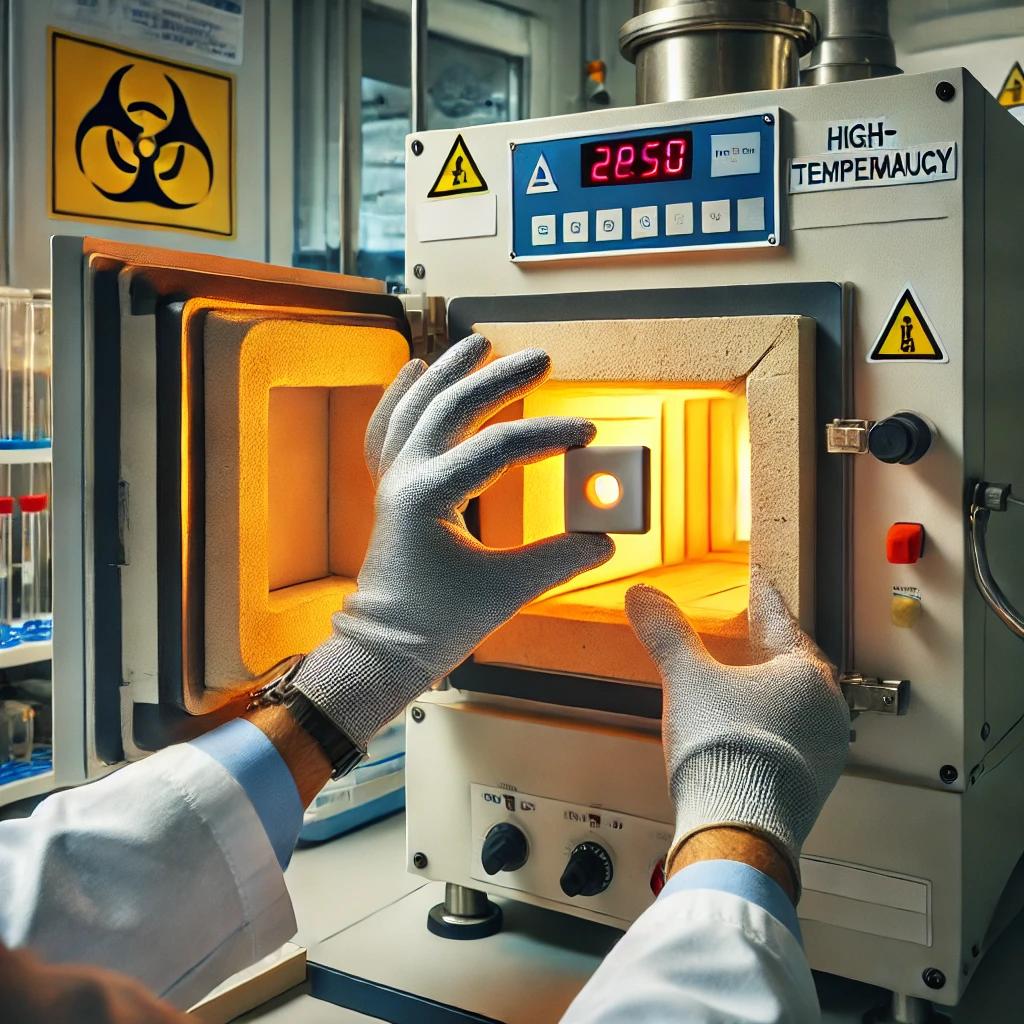
5. Consider the Heating Method
Furnaces utilize different heating methods depending on their design and purpose.
- Electric furnaces are common for laboratory use, providing precise temperature control and consistency.
- Gas-fired furnaces are more commonly used in large-scale industrial settings, offering higher temperature ranges and energy efficiency.
Tip: Electric furnaces tend to be more suitable for laboratories due to their precision and ease of use. For large-scale operations, gas-fired or even oil-fired furnaces might be more efficient.
6. Energy Efficiency and Operational Costs
A furnace is a long-term investment, and energy consumption is an important consideration in minimizing operational costs.
- Electric furnaces can be more energy-efficient and easier to maintain, but they might have higher initial costs depending on their features.
- Gas or oil furnaces are typically used for higher-temperature applications but may incur additional fuel costs and require more maintenance.
Tip: When considering energy efficiency, calculate not only the upfront costs but also the long-term energy consumption to get a true picture of the total cost of ownership.
7. Safety Features
Safety is crucial when dealing with high temperatures and potentially hazardous materials. Ensure that the furnace you choose has the appropriate safety features, such as:
- Over-temperature protection
- Automatic shut-off features
- Proper ventilation
- Insulated exteriors to prevent burns
Tip: Always opt for furnaces with advanced safety features, especially when working with highly volatile or hazardous materials.
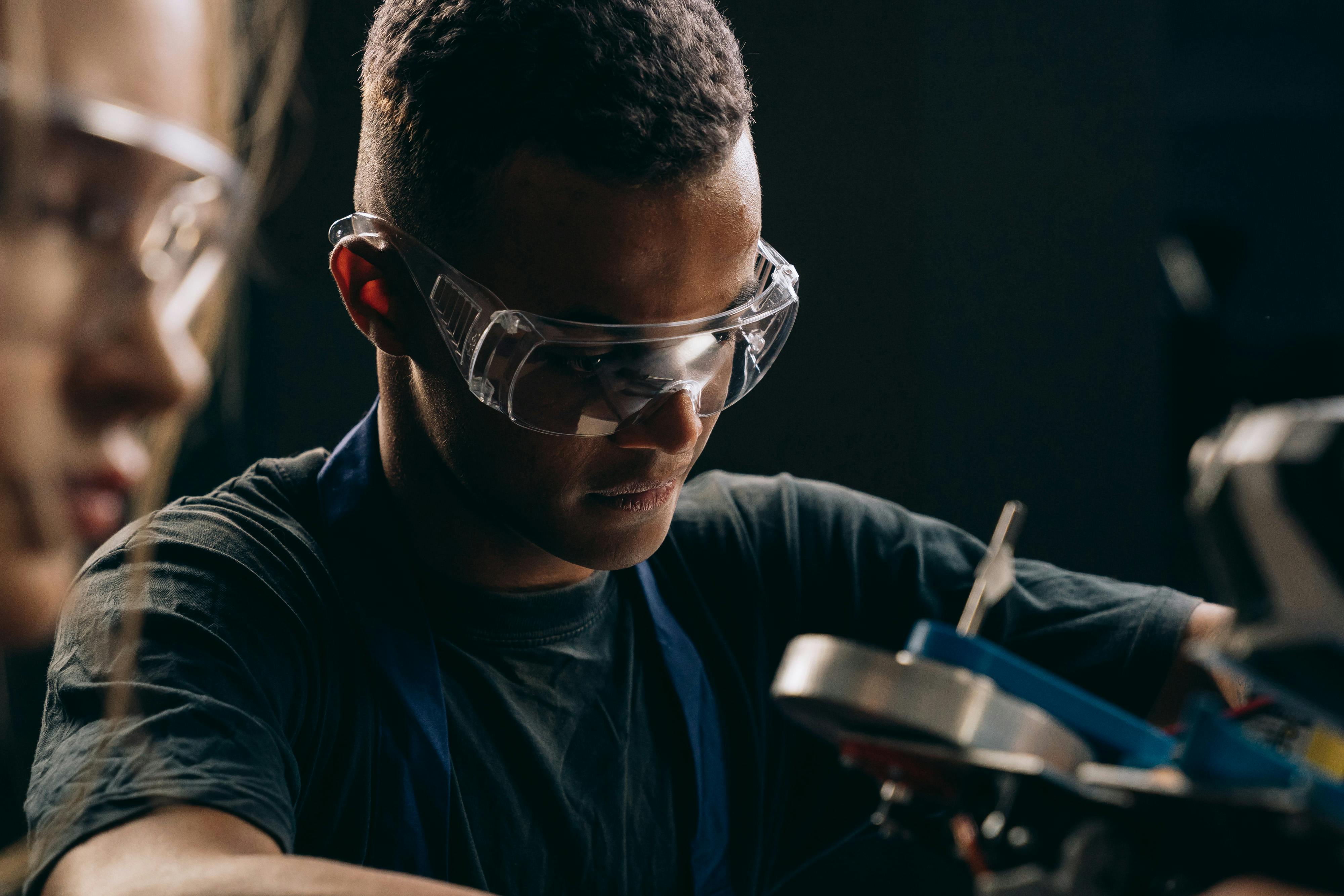
Choosing the right furnace for your laboratory or industrial application requires a balance of several key factors, including temperature range, furnace type, atmosphere control, chamber size, and safety features. Understanding your specific needs and selecting a furnace that can meet them will help ensure efficient and reliable operation, ultimately saving you time and money.