In today’s advanced manufacturing landscape, precision and efficiency are key factors in producing high-quality laminated products. One of the most effective technologies used in industries such as electronics, solar panel manufacturing, and composite material processing is the vacuum lamination press. But what exactly is a vacuum lamination press, and how does it work? Let’s explore the fundamentals of this essential manufacturing tool.
Understanding Vacuum Lamination Press
A vacuum lamination press is a machine that applies heat, pressure, and vacuum to bond multiple layers of materials together. Unlike traditional lamination processes, which rely solely on heat and pressure, vacuum lamination removes air and moisture, creating a strong, uniform bond without bubbles or defects.
How Does a Vacuum Lamination Press Work?
The vacuum lamination process involves several critical steps:
Material Preparation – The materials to be laminated, such as films, glass, or circuit boards, are cleaned and stacked in the correct order. Proper alignment is essential to ensure uniform bonding and avoid material displacement during the process.
Loading into the Press – The stacked materials are placed inside the vacuum chamber of the press. The chamber is sealed tightly to create a controlled environment for the lamination process. Depending on the machine type, multiple layers can be processed simultaneously to improve production efficiency.
Vacuum Application – The machine removes air from the chamber, eliminating any trapped moisture or bubbles that could compromise the lamination quality. This step is crucial for achieving a defect-free laminate, as air pockets can cause weak spots or delamination over time. Advanced vacuum lamination presses use precision-controlled vacuum pumps to achieve optimal conditions. The vacuum level must be carefully maintained to ensure consistent bonding and prevent material imperfections.
Heating, Heat, and Pressure Application – Once the vacuum is achieved, heating elements raise the temperature to the required level, and pressure is applied to activate the adhesive and bond the layers together. The platen temperature plays a crucial role in ensuring optimal adhesion and consistency in the lamination process. The press maintains a uniform temperature across the platen to ensure even curing of the adhesive. Depending on the material type, different temperature and pressure settings are required to achieve the best results.
Cooling and Curing – The laminated product is cooled to set the bond before being removed from the press. Proper cooling ensures that the adhesive stabilizes and prevents warping or material distortion. Some advanced vacuum lamination presses include controlled cooling systems to expedite the process while maintaining high-quality results.
Final Inspection – The finished product is inspected for quality assurance, ensuring it meets the required specifications. Manufacturers check for defects such as air bubbles, misalignment, or incomplete bonding. High-precision industries, such as electronics and solar panel production, often use automated inspection systems for accuracy.
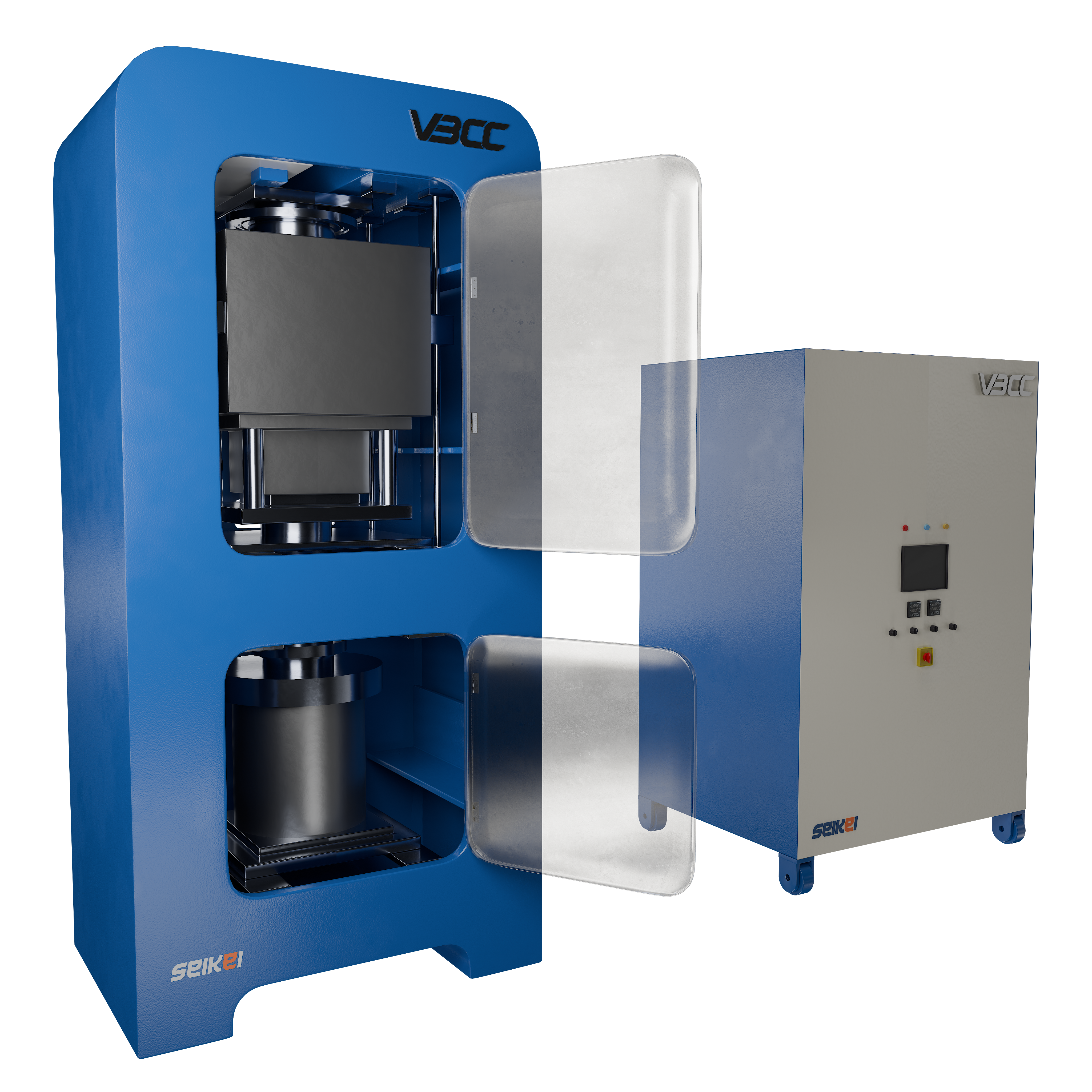
Key Benefits of Vacuum Lamination Press
A vacuum lamination press offers several advantages over traditional lamination methods:
- Eliminates Air Bubbles and Defects – The vacuum process ensures a flawless, even bond.
- Enhances Adhesion Strength – Removing air and moisture creates a stronger, more durable laminate.
- Improves Product Quality – Ideal for high-precision industries such as electronics and solar panels.
- Energy-Efficient and Cost-Effective – Reduces material wastage and enhances production efficiency.
Common Applications of Vacuum Lamination Press
Vacuum lamination presses are widely used in various industries, including:
- Electronics Manufacturing – Used in the production of printed circuit boards (PCBs) and flexible electronics.
- Solar Panel Production – Essential for encapsulating photovoltaic (PV) cells to enhance efficiency and longevity.
- Automotive Industry – Used for laminating interior panels, composite materials, and protective coatings.
- Glass and Composite Materials – Helps in bonding safety glass, decorative laminates, and structural composites.
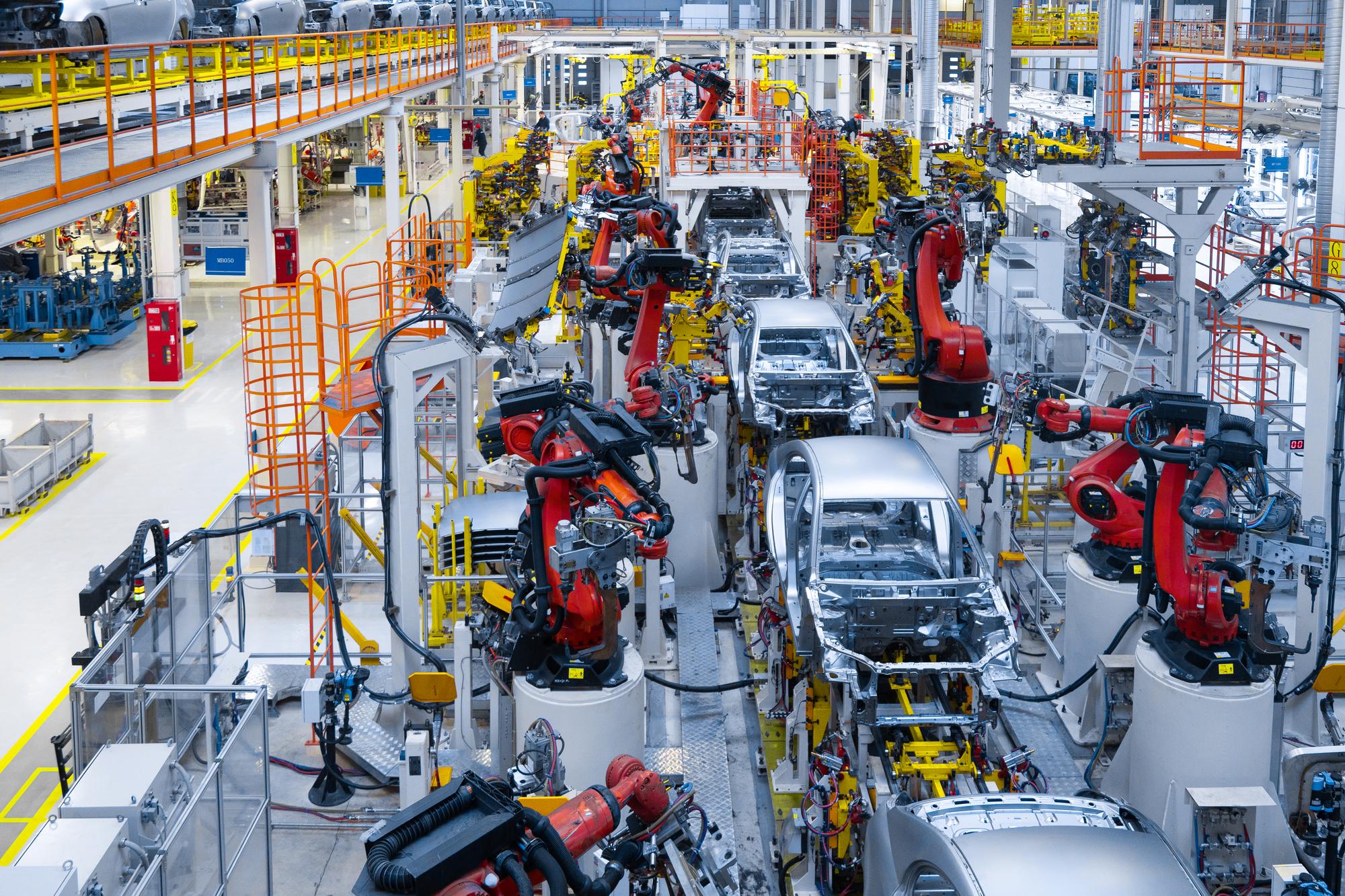
Choosing the Right Vacuum Lamination Press
When selecting a vacuum lamination press, consider factors such as:
- Size and Capacity – Ensure the machine can handle the dimensions of your materials.
- Heating Technology – Choose between infrared, thermal oil, or electrical heating based on your application.
- Platen Temperature Control – Look for precise temperature regulation to maintain consistent quality and prevent material damage.
- Vacuum Level Control – Ensuring the right vacuum level is maintained during the process is critical for achieving optimal bonding results.
- Automation Features – Look for advanced features like programmable controls, real-time monitoring, and automatic vacuum adjustments.
- Material Compatibility – Make sure the press is suitable for the materials you work with.
A vacuum lamination press is a powerful tool that enhances the quality and durability of laminated products across multiple industries. Whether you’re in electronics manufacturing, solar energy, or composite materials, understanding this technology can help you optimize your production process and achieve superior results. If you’re considering investing in a vacuum lamination press, evaluate your needs carefully and choose a machine that meets your specific requirements.