In high-performance industries like aerospace, automotive, electronics, and materials science, precision matters. One of the key processes in these fields is thermal cycling—the repeated heating and cooling of materials to specific temperatures in a controlled environment. To carry out this process effectively, a specialized piece of equipment is used: the thermal cycling furnace.
But what exactly is a thermal cycling furnace, and how does it work? Let’s break it down.
What Is a Thermal Cycling Furnace?
A thermal cycling furnace is a type of industrial furnace designed to rapidly and repeatedly heat and cool materials. Unlike traditional furnaces that focus on steady, uniform heating, thermal cycling furnaces are engineered for dynamic temperature changes, often reaching extreme highs and lows within short timeframes.
These furnaces are used to test the durability and performance of materials under thermal stress, simulate real-world operating conditions, or improve material properties through thermal treatment.
Key Features of Thermal Cycling Furnaces
- High Temperature Capability: Most units operate up to 1200°C or higher.
- Rapid Heating and Cooling Rates: Some furnaces can achieve heating and cooling ramps as fast as 50–100°C per minute.
- Temperature Uniformity: Maintains consistent temperatures throughout the chamber to ensure reliable results.
- Programmable Controllers: Advanced models include digital controllers with customizable temperature profiles and cycling parameters.
- Robust Construction: Built to withstand frequent thermal shocks and long operating hours.
How Does a Thermal Cycling Furnace Work?
The basic working principle of a thermal cycling furnace involves heating a material to a specific temperature, holding it for a set period, and then cooling it down, sometimes to sub-zero temperatures. This cycle is repeated multiple times, depending on the application.
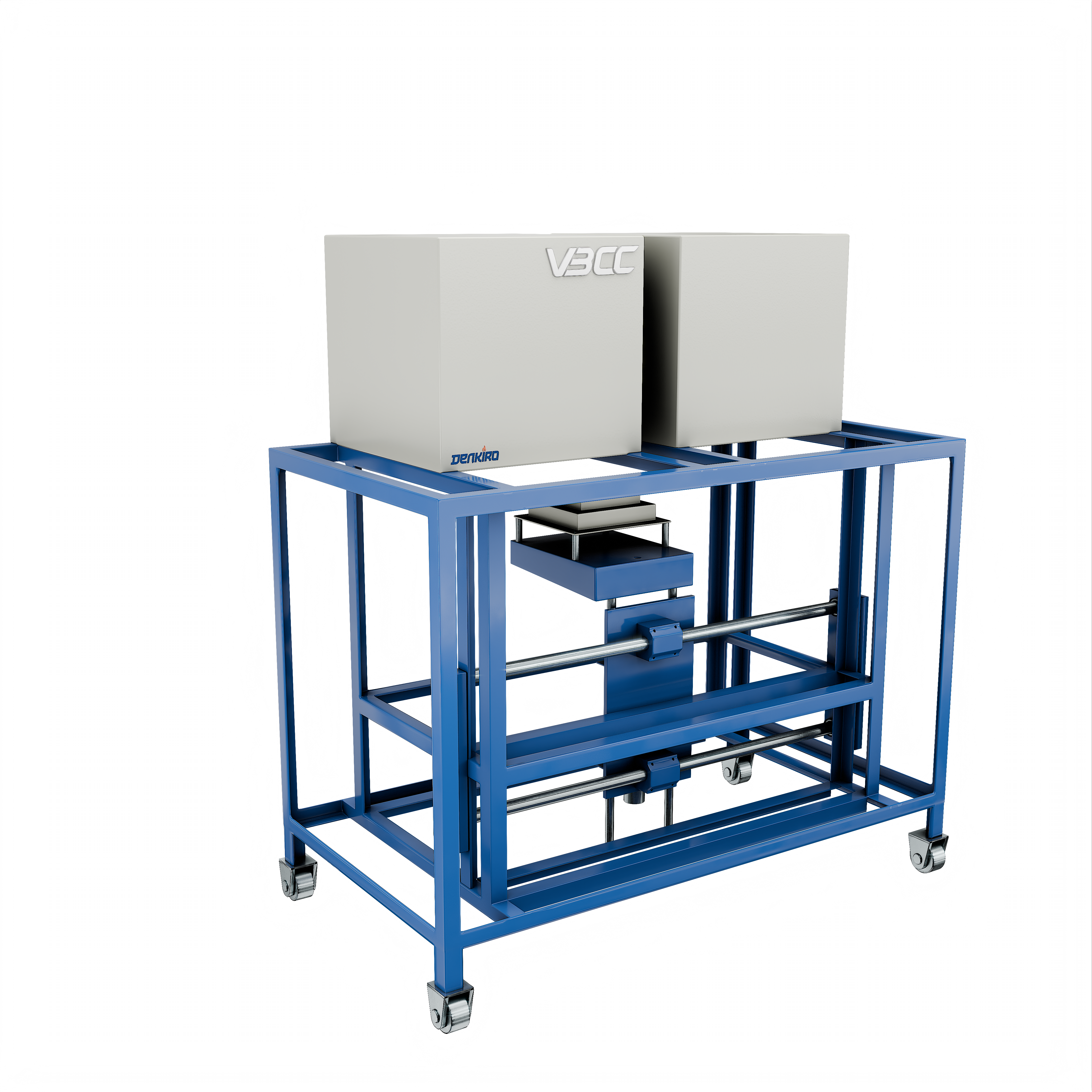
Step-by-Step Process:
1. Programmable Temperature Profiles
Operators can define heating and cooling cycles through a digital controller. These profiles specify parameters like:
- Peak temperature
- Minimum temperature
- Ramp rates (how quickly the temperature changes)
- Dwell times (how long the furnace stays at a particular temperature)
- Number of cycles
2. Heating Phase
High-performance heating elements—such as molybdenum disilicide or silicon carbide—rapidly raise the temperature. The system ensures even heat distribution, critical for consistent material exposure.
3. Cooling Phase
Once the target temperature is reached and held, the furnace begins to cool. Cooling methods can include:
- Forced air
- Water-cooled jackets
- Liquid nitrogen injection (for ultra-fast cooling)
This transition is often as vital as the heating phase, especially for stress-testing sensitive components.
4. Data Logging & Monitoring
Advanced furnaces offer real-time data tracking, allowing users to monitor temperatures, cycle completion, and anomalies. This information is invaluable for research, quality control, and regulatory compliance.
Applications of Thermal Cycling Furnaces
- Thermal Shock Testing: Evaluating how materials react to rapid temperature changes.
- Fatigue Testing: Assessing long-term durability under fluctuating temperatures.
- Stress Relief and Annealing: Improving material performance by removing residual stresses.
- Semiconductor Manufacturing: Used for rapid thermal processing of wafers.
- Composite and Metal Testing: Validating the performance of aerospace and automotive components.
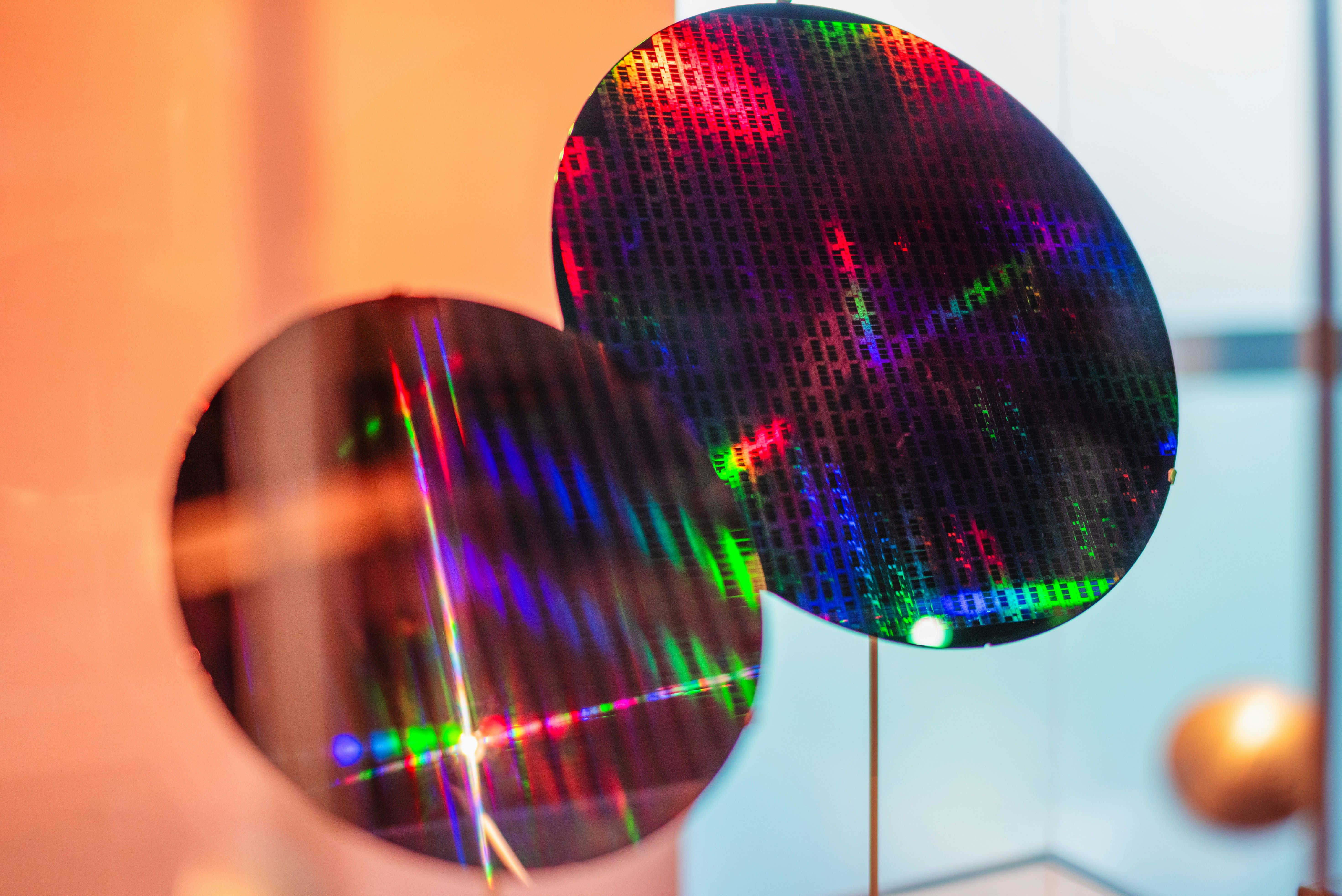
Why Thermal Cycling Matters
Thermal cycling can reveal hidden weaknesses in materials and components that wouldn’t be noticeable under steady conditions. It simulates extreme operating environments and ensures products will perform reliably over time.
By investing in thermal cycling furnaces, companies gain valuable insights into material behaviour, product lifespan, and safety, ultimately helping bring more resilient, high-performance products to market.
Whether you’re testing new aerospace alloys or validating electronic components, a thermal cycling furnace is a critical tool for ensuring performance and reliability under thermal stress. With programmable controls, rapid cycling capabilities, and precise temperature management, these furnaces bring laboratory testing closer to real-world conditions than ever before.
Looking to implement thermal cycling in your operations? Make sure you choose a furnace that meets your specific temperature range, cycling speed, and sample size requirements.