In the world of high-temperature laboratory processes, the choice of furnace can significantly affect the quality, consistency, and safety of your results. Two common contenders are vacuum furnaces and conventional furnaces—each with distinct advantages and ideal use cases. But which one truly delivers better results for your lab work?
Let’s break down the differences and see which furnace best fits your application.
What Is a Vacuum Furnace?
A vacuum furnace is a type of high-temperature furnace that operates in a sealed chamber with a controlled vacuum or inert gas atmosphere. The lack of oxygen prevents unwanted chemical reactions such as oxidation, making it ideal for processing sensitive materials.
Key Features:
- Operates under low or no oxygen
- Excellent temperature uniformity
- Often includes programmable temperature control
- Compatible with inert gases like argon or nitrogen

What Is a Conventional Furnace?
A conventional furnace (often called an atmospheric or air furnace) heats materials in ambient air. This includes muffle furnaces, box furnaces, and tube furnaces that aren't sealed or atmosphere-controlled.
Key Features:
- Easy to use and maintain
- Operates in open air
- Suitable for basic thermal processing tasks, including ashing procedures
- More cost-effective and accessible
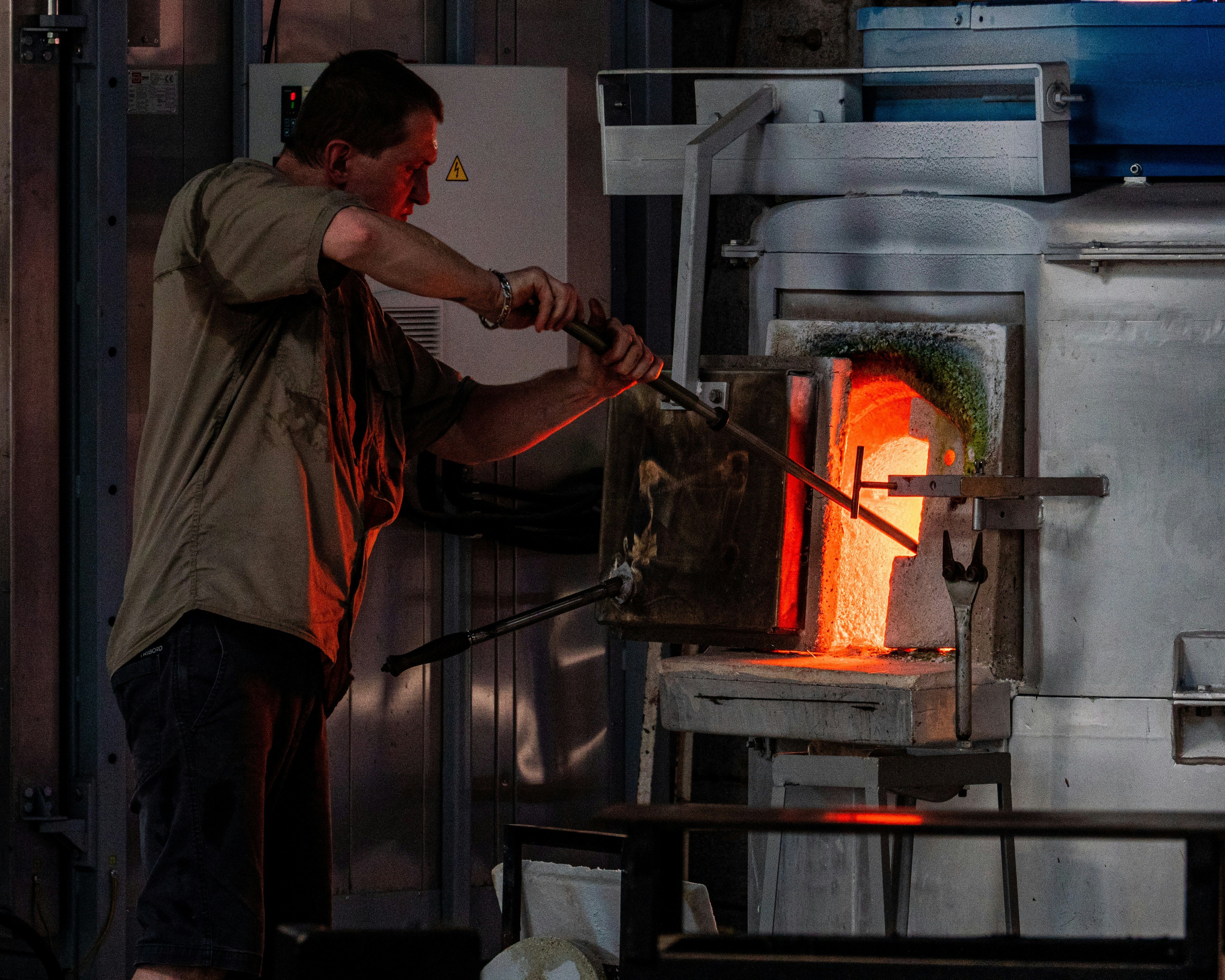
Vacuum Furnace vs. Conventional Furnace: Head-to-Head
To truly understand which furnace type delivers better results, it’s important to go beyond the surface and evaluate them across key performance and operational criteria. Here's an in-depth look at how vacuum furnaces and conventional furnaces compare:
1. Atmosphere Control
- Vacuum Furnace:
Designed to operate in a sealed environment, vacuum furnaces can remove air and oxygen from the chamber, or fill it with an inert gas like argon, nitrogen, or helium. This controlled atmosphere is essential for processes where chemical stability and oxidation prevention are critical. - Conventional Furnace:
Operates in the ambient atmosphere of the laboratory, usually with no protection from oxygen or moisture. This makes them unsuitable for materials that oxidize, corrode, or react with air at high temperatures.
2. Oxidation and Contamination
- Vacuum Furnace:
The vacuum or inert atmosphere prevents oxidation, decarburization, and other unwanted reactions. This is vital when working with reactive metals, such as titanium or nickel alloys, or when ultra-clean surfaces are needed post-processing. - Conventional Furnace:
High temperatures combined with oxygen exposure often result in oxidation or scale formation. This can compromise the integrity and purity of sensitive samples or precision components.
3. Temperature Uniformity and Precision
- Vacuum Furnace:
Known for excellent temperature uniformity due to multiple heating zones, reflective chamber linings, and precise control systems. This consistency is crucial for complex processes like heat treatment, annealing, or sintering where deviations can lead to defects. - Conventional Furnace:
Offers decent temperature control, but may have hotspots or uneven heating—especially in older or budget models. Adequate for general heating but not ideal for processes requiring narrow thermal tolerances.
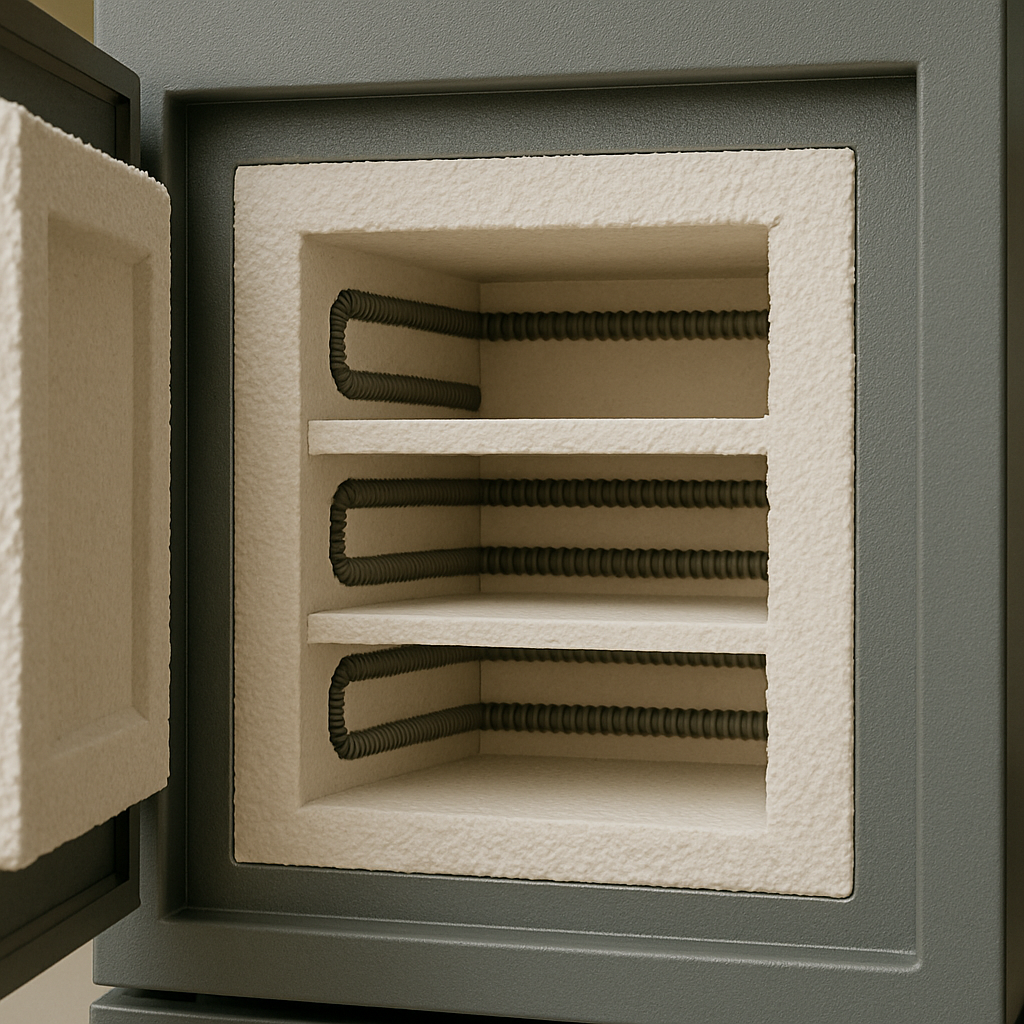
4. Material Compatibility
- Vacuum Furnace:
Suitable for a wide range of materials, including high-purity metals, specialty alloys, ceramics, and sensitive electronic components. They are well-suited for treating intricately shaped components that demand consistent temperature exposure throughout the entire part. - Conventional Furnace:
"It is effective for processing durable materials such as ceramics, glass, and certain organic compounds. Commonly used for ashing, calcining, and general heating—not recommended for materials that oxidize or degrade in air.
5. Process Complexity and Customization
- Vacuum Furnace:
Highly programmable with multi-step heating profiles, ramp rates, dwell times, and controlled cooling. Often integrated with PLC systems or digital controllers for repeatable processes. - Conventional Furnace:
Simpler interfaces, with manual or basic digital controls. Ideal for straightforward heating tasks but lacks the complexity needed for advanced thermal processes.
6. Operating Cost and Maintenance
- Vacuum Furnace:
Vacuum furnaces tend to have higher initial and operational expenses due to their complex systems, including vacuum pumps, sealed chambers, and gas control components. They also demand routine upkeep and experienced personnel to maintain efficiency and reliability. - Conventional Furnace:
Economical to purchase and operate. Lower maintenance requirements and easy to use, making them ideal for educational labs, small-scale research, or facilities with limited budgets.
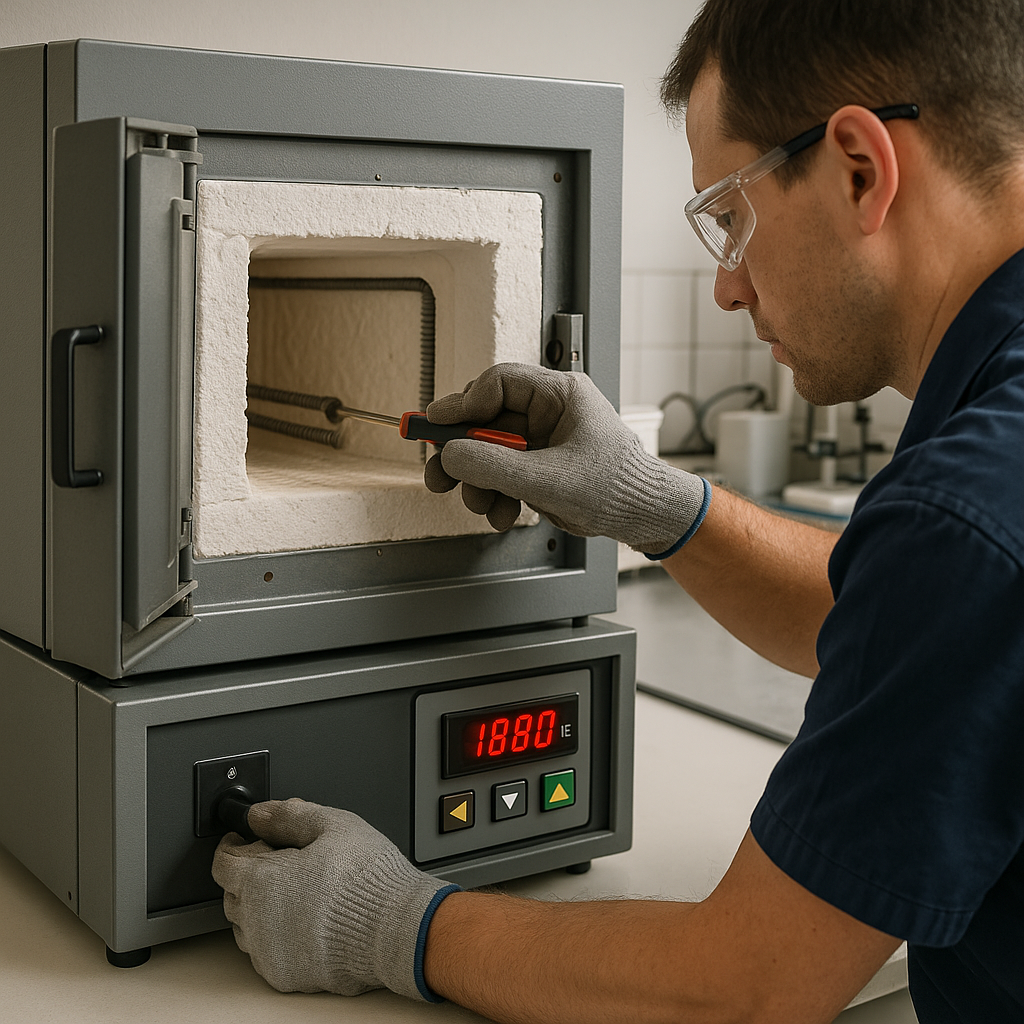
7. Application Suitability
- Vacuum Furnace:
Used extensively in aerospace, defence, medical device manufacturing, and advanced research. Ideal for applications like vacuum brazing, diffusion bonding, and heat-treating high-end alloys. - Conventional Furnace:
Common in academic labs, general chemistry or materials testing, and basic thermal processing where air exposure isn’t a concern.
So, Which Offers Better Results?
- If your goal is precision, purity, and oxidation-free environments, a vacuum furnace offers far superior results.
- If you're focused on basic heating, material durability, or cost-efficiency, a conventional furnace gets the job done effectively.
Bottom line: Choose the furnace based on your material’s sensitivity, your process requirements, and your lab’s budget.
Investing in the right furnace isn't just about specs—it’s about aligning your equipment with your lab’s objectives. For advanced research and high-performance material processing, a vacuum furnace is worth the investment. For routine lab work and general applications, a conventional furnace remains a dependable workhorse.