Laboratory furnaces play a crucial role in scientific research, materials testing, and industrial applications. Whether used for annealing, ashing, calcination, or sintering, maintaining precise temperature control in a laboratory furnace is essential for accurate and reproducible results. This blog explores the key aspects of temperature control in laboratory furnaces, common challenges, and best practices for achieving optimal performance.
The Importance of Temperature Control
Temperature control in a laboratory furnace ensures consistent and uniform heating, which is vital for applications requiring precise thermal conditions. Inconsistent temperatures can lead to incorrect experimental results, material degradation, and compromised safety. Proper temperature regulation not only improves energy efficiency but also extends equipment life and enhances the quality of outputs. Precise control helps maintain the integrity of materials, ensures repeatability in experiments, and optimizes process efficiency in industrial applications.
Key Components of Temperature Control
1. Thermocouples and Sensors
Thermocouples are the most commonly used temperature sensors in a laboratory furnace. These devices measure temperature based on voltage changes resulting from heat exposure. Different types of thermocouples, such as Type K, Type S, and Type R, offer varying degrees of accuracy and temperature range capabilities. Other sensors, such as resistance temperature detectors (RTDs) and infrared sensors, are also used for specific applications requiring high accuracy and fast response times.
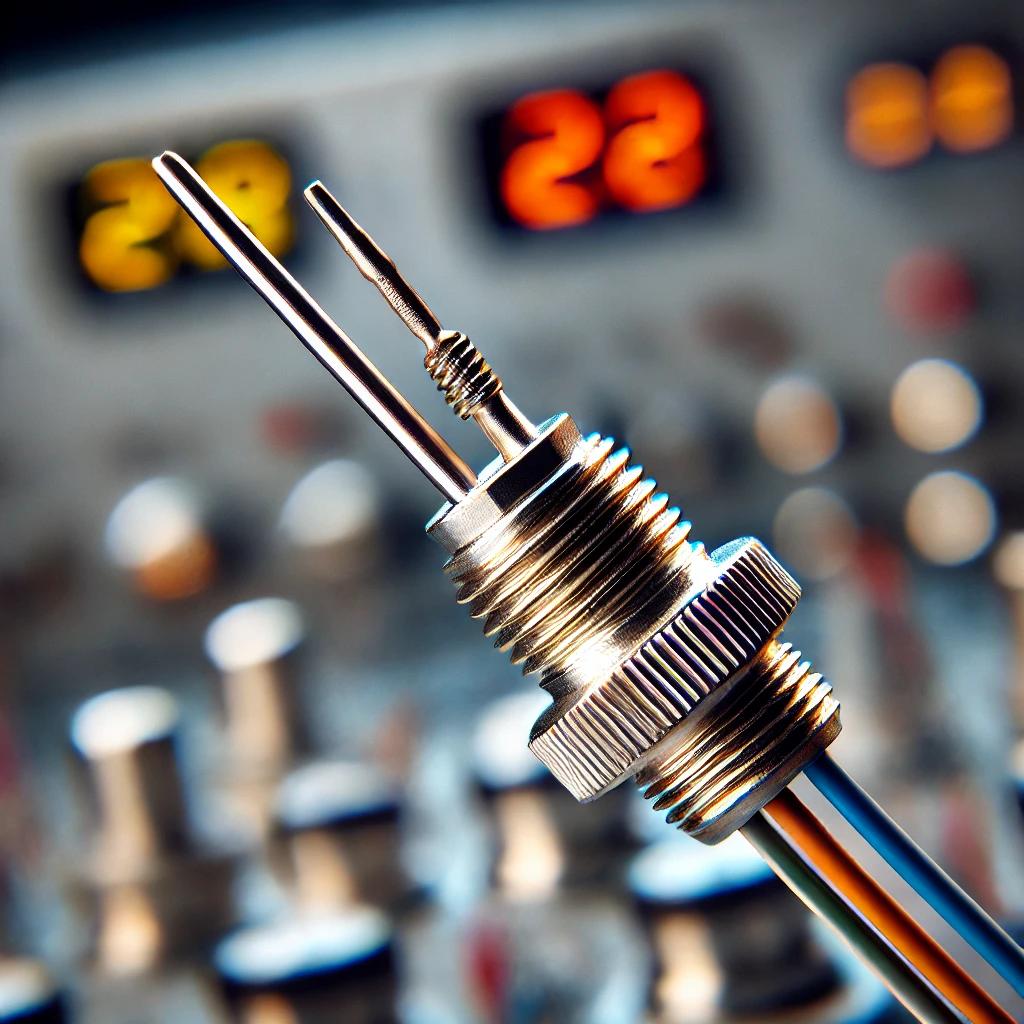
2. PID Controllers
Proportional-Integral-Derivative (PID) controllers regulate laboratory furnace temperature by adjusting heating elements based on real-time feedback from sensors. PID controllers minimize temperature fluctuations, ensuring stability and precision. These controllers work by continuously calculating the difference between the desired temperature setpoint and the actual furnace temperature, adjusting the power supply to the heating elements accordingly. Advanced PID controllers offer programmable temperature profiles, data logging, and remote monitoring capabilities.
3. Heating Elements
Heating elements are essential for generating the thermal energy required for furnace operation and are commonly made from materials such as:
- Silicon Carbide (SiC): Known for its durability and oxidation resistance, it is suitable for high-temperature applications.
- Molybdenum Disilicide (MoSi₂): With excellent oxidation resistance, it is ideal for extreme temperature conditions.
- Kanthal Wire: A blend of iron, chromium, and aluminium, this material is widely used for medium-temperature applications.
The selection of a heating element depends on factors like the required temperature range, specific application, and material compatibility. Choosing the right element ensures efficient heating performance and enhances the longevity of the laboratory furnace.
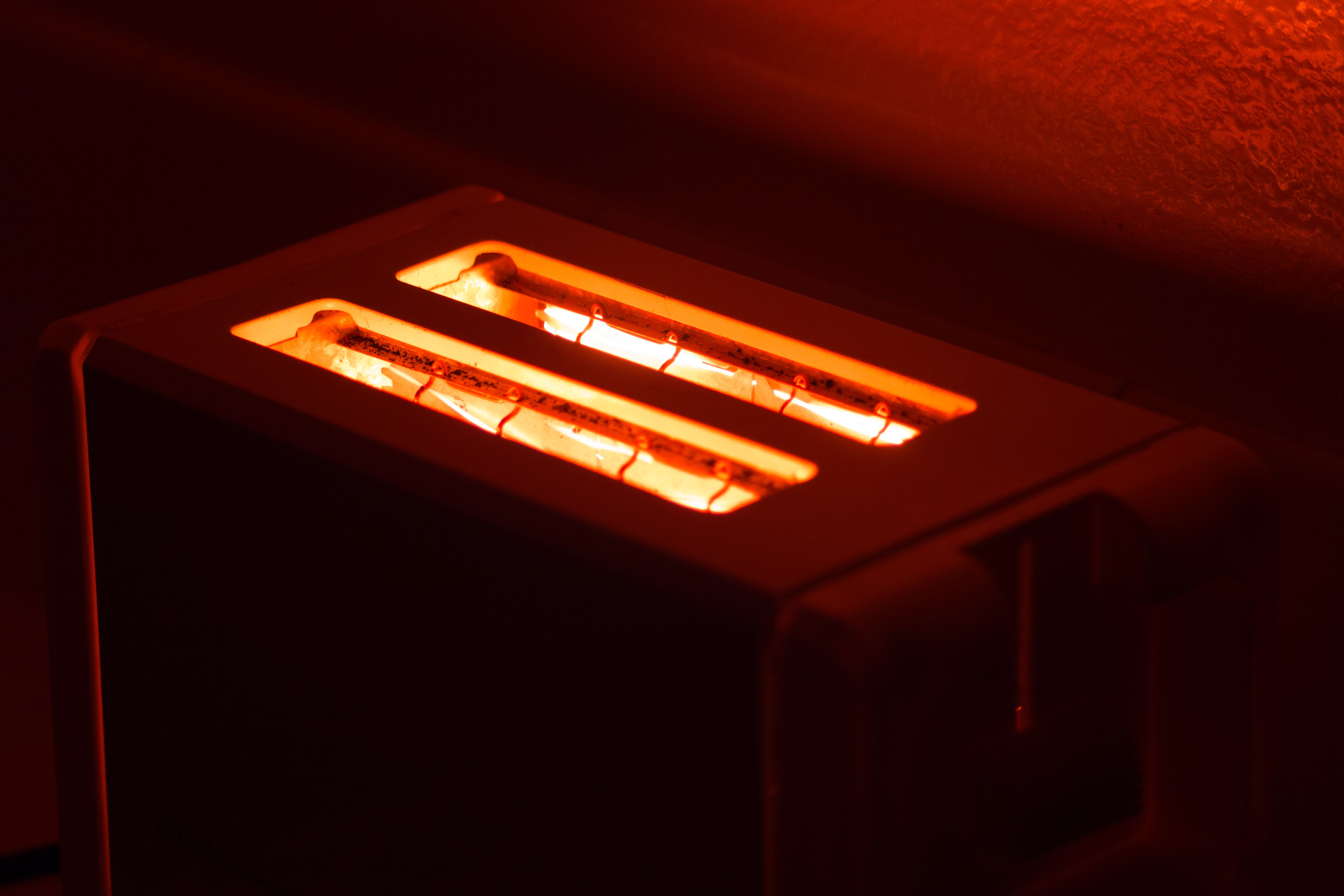
4. Insulation Materials
High-quality insulation materials, such as ceramic fibre and alumina bricks, help maintain temperature uniformity and prevent heat loss in a laboratory furnace. Proper insulation enhances furnace efficiency and minimizes energy consumption. Insulation also contributes to safety by reducing the external surface temperature of the furnace, minimizing the risk of burns or heat damage to nearby equipment.
Common Temperature Control Challenges
1. Temperature Uniformity Issues
Variations in temperature across the laboratory furnace chamber can impact experimental outcomes and material properties. Several factors contribute to non-uniform heating, including improper thermocouple placement, uneven insulation, and incorrect loading of materials. Using multiple thermocouples to monitor different zones within the furnace can help address this issue.
2. Overshooting and Undershooting
Incorrect PID settings can cause temperature overshooting (exceeding the setpoint) or undershooting (not reaching the setpoint). This can affect material integrity and experimental accuracy. Fine-tuning PID parameters ensures smooth temperature transitions, preventing sudden fluctuations that can lead to thermal stress or inconsistent processing.
3. Sensor Calibration Errors
Improperly calibrated sensors can lead to inaccurate temperature readings, affecting process outcomes. Regular calibration of thermocouples, RTDs, and infrared sensors is necessary to maintain accuracy. Calibration should be performed using certified reference standards to ensure consistency and reliability in measurements.
4. External Environmental Factors
Ambient temperature, airflow, and humidity can influence laboratory furnace performance. Placing the furnace in a controlled environment minimizes these external impacts. Additionally, maintaining proper ventilation and ensuring adequate spacing between furnaces and other equipment can reduce thermal interference and improve overall performance.
Best Practices for Optimal Temperature Control
To ensure effective temperature control and enhance laboratory furnace performance, consider the following best practices:
Regular Calibration: Periodically calibrate sensors and controllers to ensure accuracy and reliability in temperature measurements.
Proper Furnace Loading: Avoid overloading or unevenly distributing materials, as this can lead to temperature gradients and inconsistent heating.
Monitor and Adjust PID Settings: Continuously monitor temperature profiles and adjust PID parameters if necessary to maintain stability.
Use Quality Insulation: High-performance insulation reduces heat loss, enhances energy efficiency, and ensures uniform heating.
Preventative Maintenance: Routine inspections and maintenance of heating elements, sensors, and insulation prevent unexpected failures and prolong laboratory furnace lifespan.
Data Logging and Monitoring: Implement systems for recording temperature data over time to analyse performance trends and detect potential issues before they become critical.
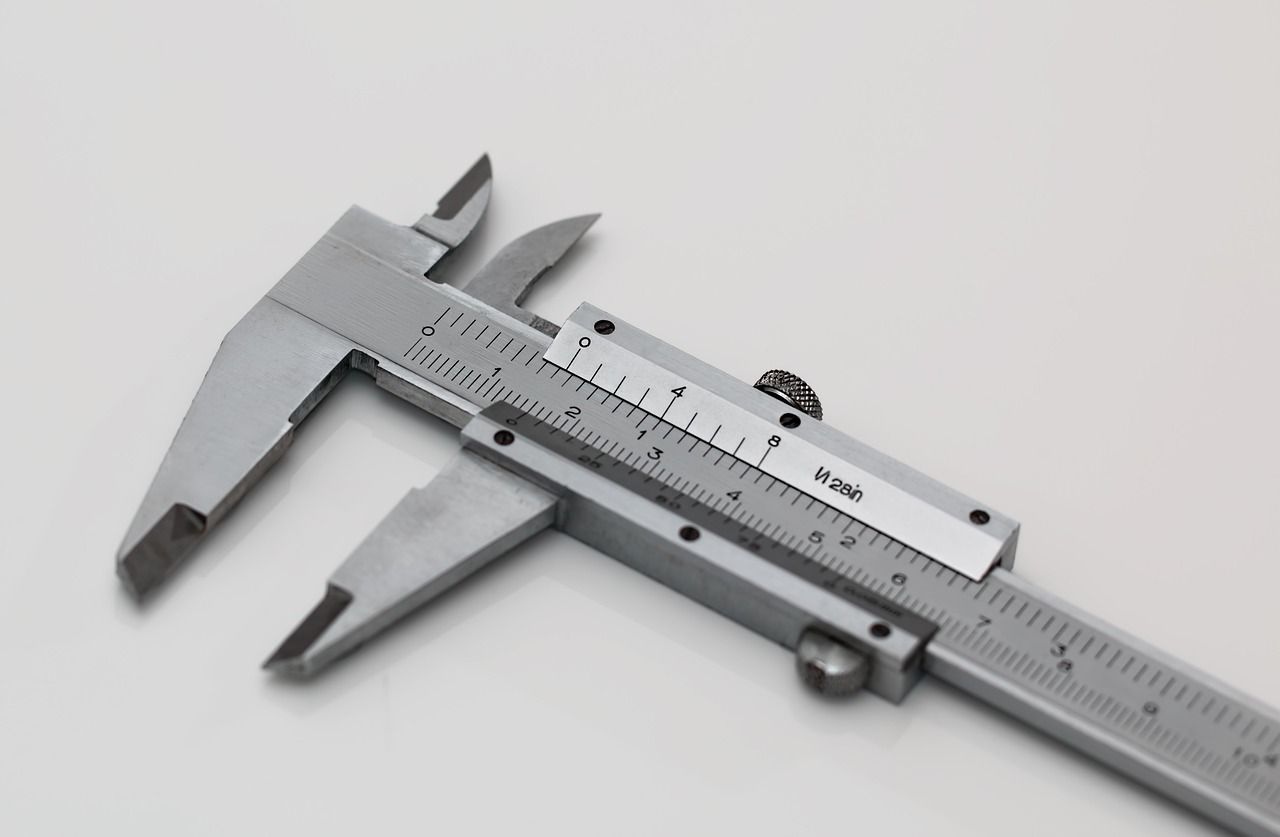
Effective temperature control in a laboratory furnace is critical for achieving precise and reliable results. By understanding the key components, addressing common challenges, and following best practices, users can enhance furnace performance and ensure consistent outcomes in their experiments and industrial applications. Investing in high-quality equipment, proper calibration, and regular maintenance further improves efficiency and longevity, making temperature control a cornerstone of successful laboratory operations.
Laboratory professionals and researchers should prioritize temperature management strategies to maximize efficiency, reduce energy consumption, and ensure the integrity of their scientific or industrial processes. With advanced technologies such as PID controllers, high-precision sensors, and smart monitoring systems, achieving optimal temperature control in a laboratory furnace has become more attainable than ever before.