A High Temperature Furnace is the heart of many industrial processes—whether it's heat treatment in metallurgy, sintering in ceramics, or component manufacturing in aerospace. Operating at extreme thermal levels, these furnaces demand consistent maintenance to ensure optimal performance, safety, and energy efficiency.
Failing to perform regular maintenance may result in poor temperature regulation, unexpected shutdowns, and potentially hazardous situations. Whether you're an operator or a plant engineer, here are the top 10 maintenance tips to keep your High Temperature Furnace in peak condition.
1. Perform Regular Visual Inspections
Regular visual checks are among the easiest and most reliable methods for keeping a High Temperature Furnace in good working condition. Over time, components may show early signs of failure such as:
- Noticeable surface cracks or discoloration on the refractory lining
- Dust build-up or residue deposits
- Warped door hinges or frame deformities
Identifying problems in their early stages can help prevent major breakdowns and expensive fixes in the future. Always inspect when the high temp furnace is cool and safely shut down.
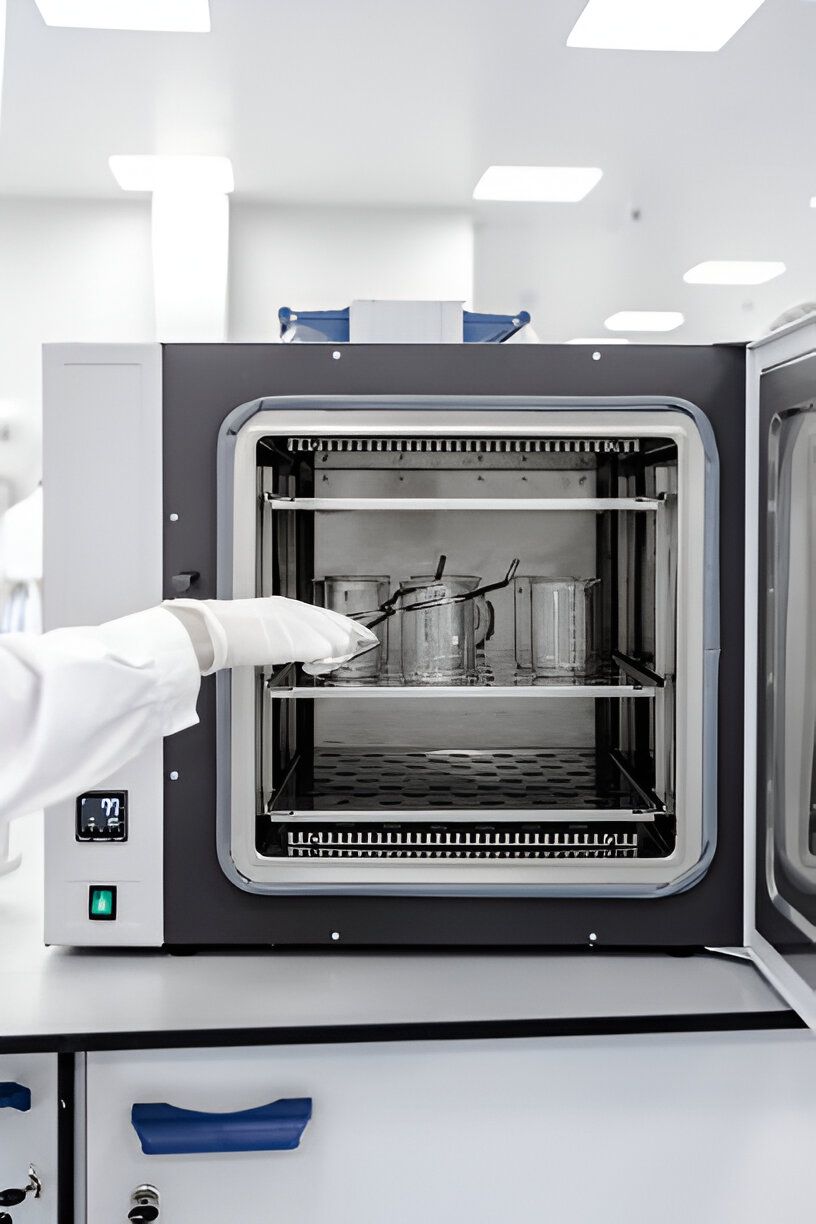
2. Monitor Furnace Temperature Consistently
Maintaining consistent product quality depends on accurately regulating the furnace temperature. If your readings start to fluctuate, it could point to deeper issues like sensor failure or insulation degradation.
Best practices include:
- Using multiple calibrated sensors to verify readings
- Setting up automated alerts for temperature anomalies
- Keeping historical temperature logs for trend analysis
An inconsistent furnace temperature can lead to under- or over-processing of materials, reducing production quality and increasing energy costs.
3. Check Refractory Lining for Wear and Tear
The refractory lining is a vital thermal barrier inside your High Temperature Furnace. Over time, extreme heat cycles and mechanical loading degrade this layer, reducing efficiency and safety.
What to look for:
- Refractory bricks showing signs of cracking, chipping, or deformation
- Discoloration that indicates hot spots or damage
- Loose or misaligned panels
Conduct routine inspections and maintenance of the lining to maintain consistent heat distribution in high-temperature furnaces.
4. Calibrate Temperature Sensors Regularly
Thermocouples and infrared sensors degrade with prolonged exposure to heat. To maintain reliable furnace temperature control, calibration is essential.
Follow these guidelines:
- Calibrate sensors at least quarterly or as specified by the manufacturer
- Compare readings against a certified standard or reference device
- Replace faulty sensors immediately
Precision is key—especially when working with a High Temperature Furnace where even minor variances can affect product outcomes.
5. Lubricate Moving Parts and Components
While a high temp furnace has fewer mechanical parts than other industrial equipment, components like loading doors, hinges, and actuators still require lubrication to operate smoothly.
Maintenance suggestions:
- Use high-temperature-rated grease or lubricants
- Clean off old residue before applying new lubricant
- Maintain lubrication routines based on the timing specified by the original equipment maker
Applying lubrication correctly helps minimize wear and avoid expensive breakdowns during use.
6. Clean Burners and Heating Elements
Whether your High Temperature Furnace is electric or gas-fired, cleaning heating elements and burners is crucial for optimal thermal efficiency.
Maintenance tasks include:
- Removing soot or residue from gas burners
- Brushing or vacuuming electric heating elements
- Inspecting for corrosion or uneven heating patterns
Clean components heat faster, maintain a more stable furnace temperature, and consume less energy.
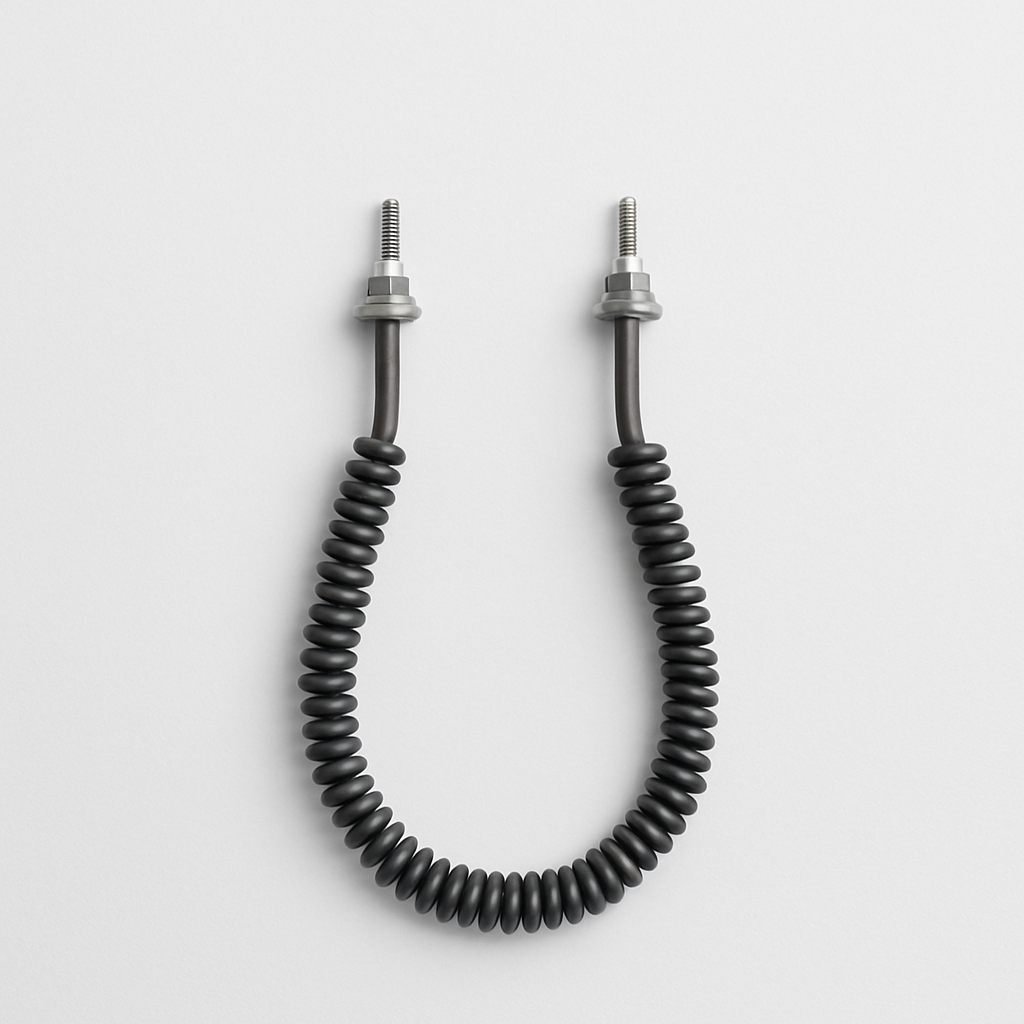
7. Replace Worn Seals and Gaskets
Air leaks from damaged seals and gaskets compromise both energy efficiency and internal atmosphere control. In a high temp furnace, maintaining exact conditions is crucial for reliable and efficient operation.
What to do:
- Check door seals for flattening or cracking
- Look for telltale heat marks indicating leakage
- Install new seals as soon as any deterioration is noticed
Tight seals help your High Temperature Furnace maintain consistent operating conditions and reduce energy waste.
8. Review the Control System Software
Modern High Temperature Furnaces rely on advanced control systems to manage heating cycles, alarms, and temperature profiles. Ensuring your software is updated in a timely manner plays a key role in maintaining consistent and trouble-free furnace performance.
Maintenance tasks include:
- Backing up settings regularly
- Installing firmware updates from the OEM
- Reviewing furnace logic and settings for optimization
Software issues can cause erratic furnace temperature control, which could result in product inconsistencies or safety hazards.
9. Maintain a Clean Work Area
An organized and clean environment around your High Temperature Furnace minimizes risk and simplifies inspections.
Best practices:
- Store flammable materials away from any heat-emitting equipment or surfaces
- Remove surrounding dirt and debris to prevent it from entering the furnace
- Keep all control panels, interfaces, and emergency switches easily accessible at all times
A clean work zone contributes to the safety and longevity of your furnace and enhances efficiency during maintenance checks.
10. Keep a Detailed Maintenance Log
Tracking maintenance activities helps you understand wear patterns and predict future service needs. For a High Temperature Furnace, documentation is not just helpful—it's essential.
Your maintenance log should include:
- Dates of inspections, repairs, and calibrations
- Technician notes and photos of issues
- Parts replaced and upcoming service schedules
Good recordkeeping supports ISO compliance, improves diagnostics, and helps avoid repeat issues.
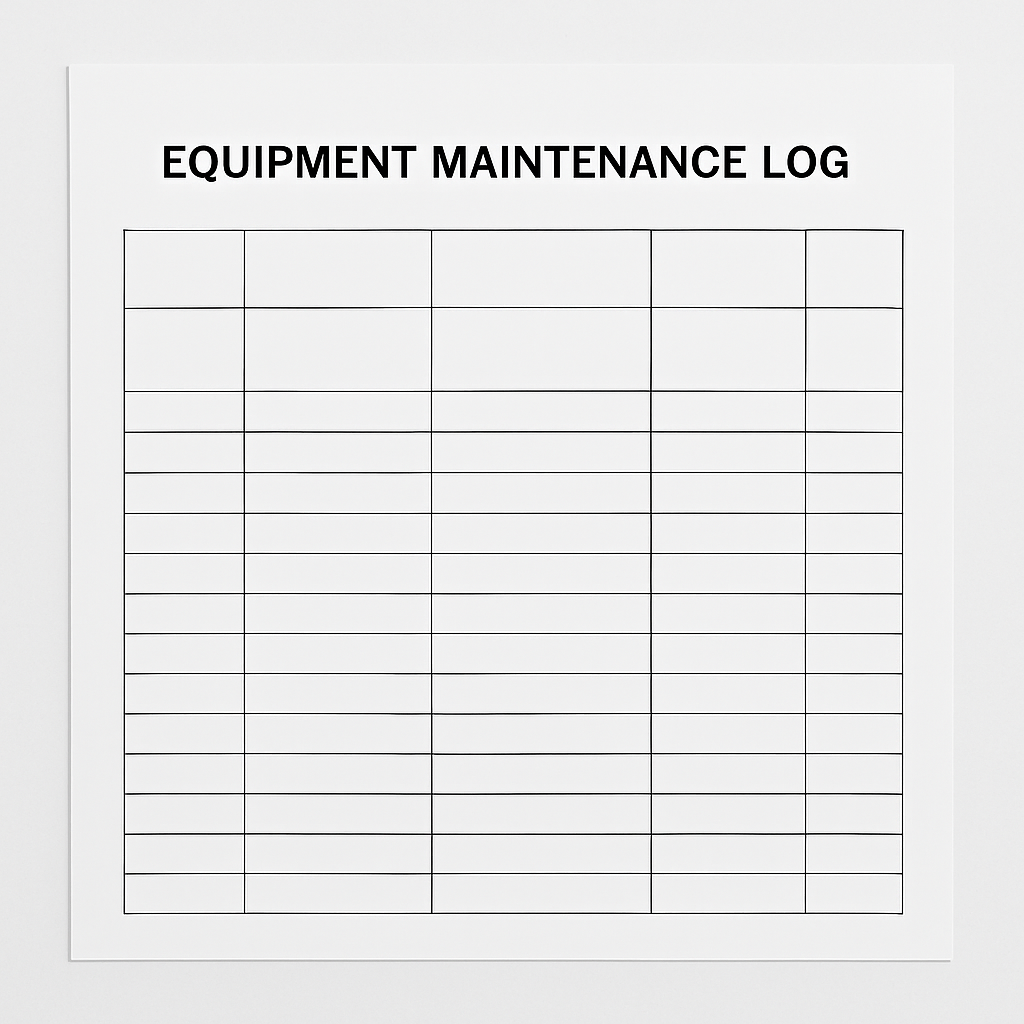
Your High Temperature Furnace is a mission-critical piece of equipment—one that requires proactive care and detailed attention. By applying these ten tips consistently, you’ll extend the furnace’s lifespan, ensure stable furnace temperature conditions, and maintain high productivity with fewer interruptions.
Preventive maintenance isn’t just a best practice—it’s a strategic investment in quality, safety, and long-term savings.