In today’s fast-evolving industrial landscape, automation and precision engineering are driving faster production, higher quality, and improved safety. One key piece of equipment central to this transformation is the hydraulic press—specifically, the automatic hydraulic press.
Whether you're stamping metal panels or moulding advanced composites, automatic hydraulic presses deliver unparalleled efficiency and accuracy. But what makes them so powerful?
The Technology Behind Automatic Hydraulic Press Systems
Before diving into the industries that rely on them, it's important to understand how automatic hydraulic presses work—and what sets them apart.
Core Components of an Automatic Hydraulic Press:
- Hydraulic Power Unit (HPU): Generates and supplies fluid energy to operate the ram by directing hydraulic fluid through the system.
- Programmable Logic Controller (PLC): The system’s brain, automating sequences, monitoring performance, and ensuring consistency.
- Sensors and Feedback Loops: Monitor force, position, and temperature in real time, allowing automatic adjustments during operation.
- Human-Machine Interface (HMI): A touchscreen or software interface for setting parameters and monitoring system health.
- Safety Systems: Includes light curtains, pressure relief valves, and emergency stop mechanisms for operator protection.
Key Advantages of Automatic Hydraulic Press Technology:
- Precision Control: Easily set exact pressure, timing, and stroke parameters.
- Repeatability: Essential for mass production with strict quality standards.
- Data Logging: Tracks cycle data, fault logs, and maintenance schedules.
- Smart Factory Integration: Compatible with Industry 4.0 systems, including IoT devices and centralized monitoring platforms.
Automated hydraulic presses, featuring advanced technology, are widely employed in various industries. Below are ten major industries that extensively depend on these machines:
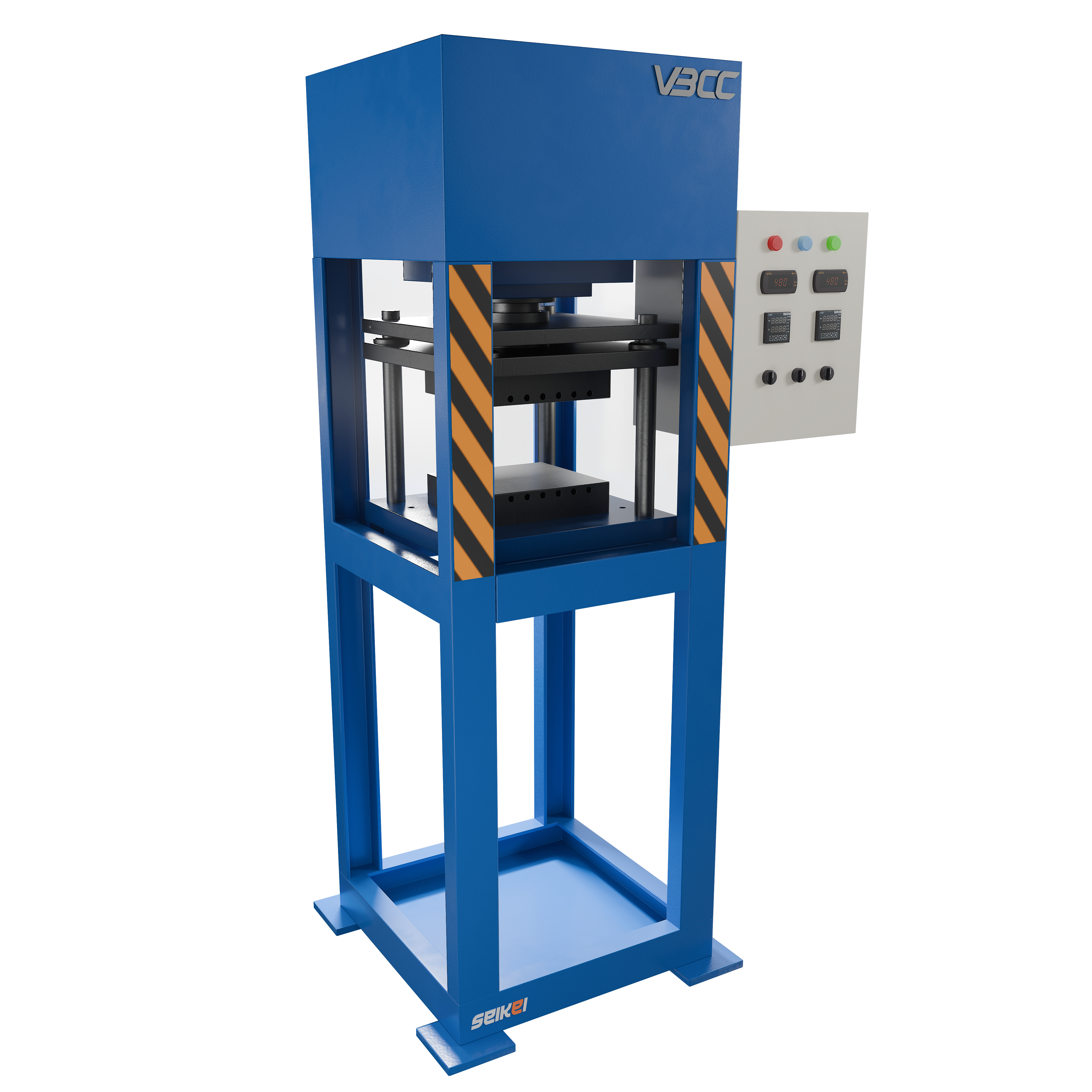
1. Automotive Industry
The automotive sector is a major user of automatic hydraulic presses. These machines are essential for:
- Stamping car body panels
- Assembling engine components
- Moulding interior parts
- Compacting brake pads and clutch plates
Why it matters: Speed and consistency are critical in automotive manufacturing. Automatic presses ensure high-volume output with minimal error, enhancing both productivity and safety.
2. Aerospace Industry
In aerospace, precision is non-negotiable. Automatic hydraulic presses are used to:
- Develop cutting-edge materials with enhanced strength properties, including titanium-based alloys and advanced composite components.
- Manufacture aircraft structural components
- Join composite layers using regulated heat and pressure conditions
Why it matters: Automatic controls maintain the tight tolerances and repeatability required for flight-certified components.
3. Electronics Industry
Modern electronics demand miniature, high-precision components. Presses are used for:
- Laminating printed circuit boards (PCBs)
- Encapsulating electronic parts
- Assembling connectors and switches
Why it matters: These presses deliver micro-level accuracy and support cleanroom-compatible processes—vital in electronics production.
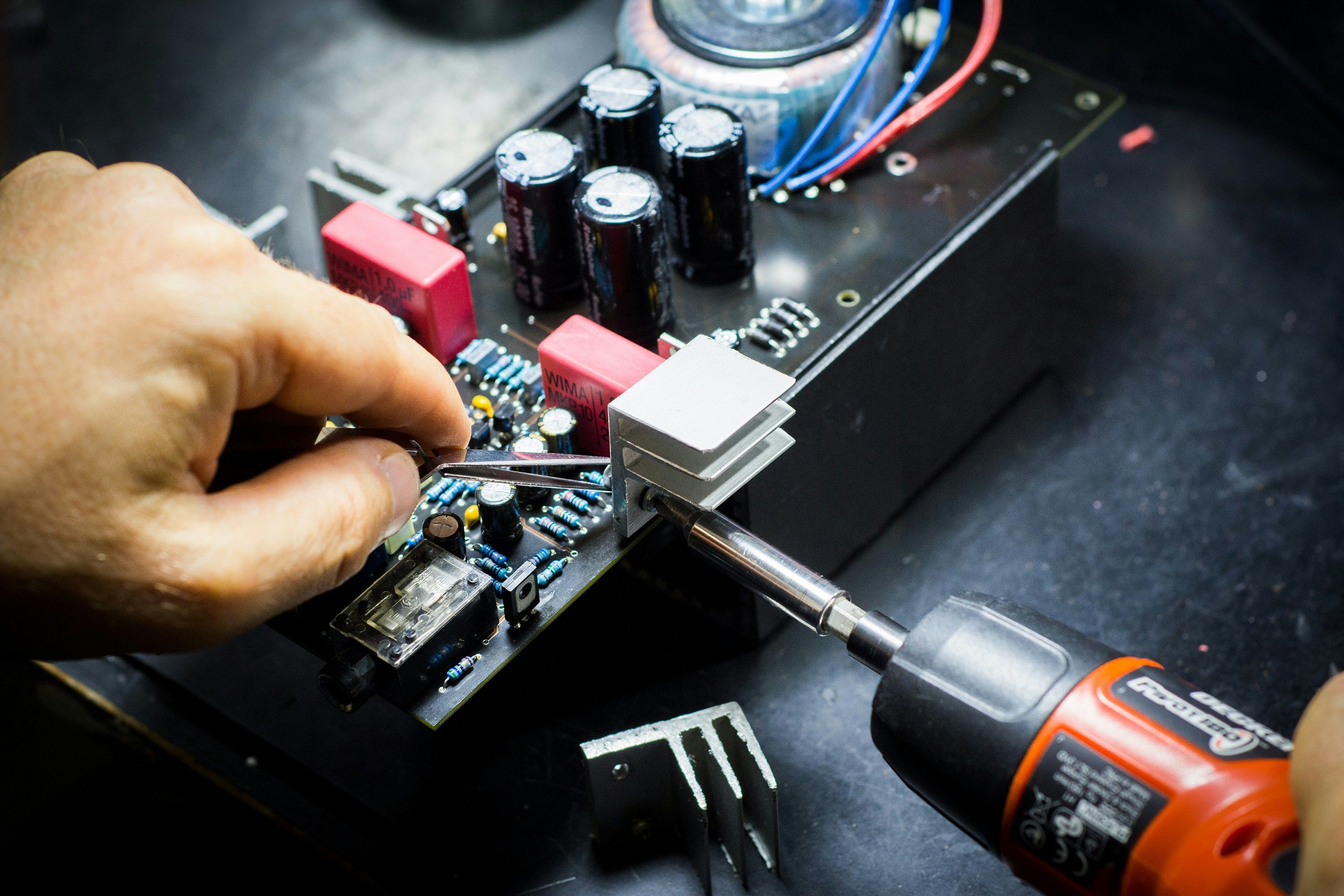
4. Appliance Manufacturing
Appliances—from washing machines to microwaves—contain stamped or moulded components. Hydraulic presses are used for:
- Forming sheet metal for housings and panels
- Embossing logos and control indicators
- Moulding plastic parts
Why it matters: Automation reduces manual labour and increases efficiency in high-volume production lines.
5. Medical Device Industry
Cleanliness and precision are paramount in medical manufacturing. Presses are used for:
- Assembling surgical instruments
- Moulding plastic components like syringe bodies and device housings
- Compressing materials for prosthetics and implants
Why it matters: Automated systems ensure sterile, error-free production in compliance with FDA and ISO standards.
6. Powder Metallurgy and Sintering Industry
This industry uses hydraulic presses to compact powdered metals into specific shapes before sintering. Applications include:
- Tooling inserts
- Gears and bearings
- Structural parts for automotive and aerospace
Why it matters: High tonnage and consistency are crucial for the structural integrity and quality of sintered parts.

7. Plastic and Rubber Moulding
In this sector, automatic hydraulic presses are used for:
- Compression moulding of gaskets, seals, and O-rings
- Producing plastic parts for consumer and industrial applications
Why it matters: Automation ensures consistent cycles, uniform pressure, and energy-efficient curing processes.
8. Packaging Industry
Hydraulic presses support high-speed packaging operations by:
- Forming and sealing packaging materials
- Cutting die patterns from plastic or cardboard
- Laminating multilayer barrier materials
Why it matters: Automation is key to meeting high-volume demands, particularly in food and pharmaceutical packaging.
9. Construction and Building Materials
These presses are used in manufacturing:
- Precast concrete elements
- Bricks, tiles, and pavers
- Laminated wood or fibreboard panels
Why it matters: They offer uniform compaction and can easily handle heavy-duty materials for structural use.
10. Defence and Military Equipment
This sector requires tough, reliable components. Hydraulic presses are used for:
- Shaping armor panels
- Forming explosive casings
- Manufacturing firearm and ammunition parts
Why it matters: Automatic presses ensure strength, consistency, and safety in critical defence applications.
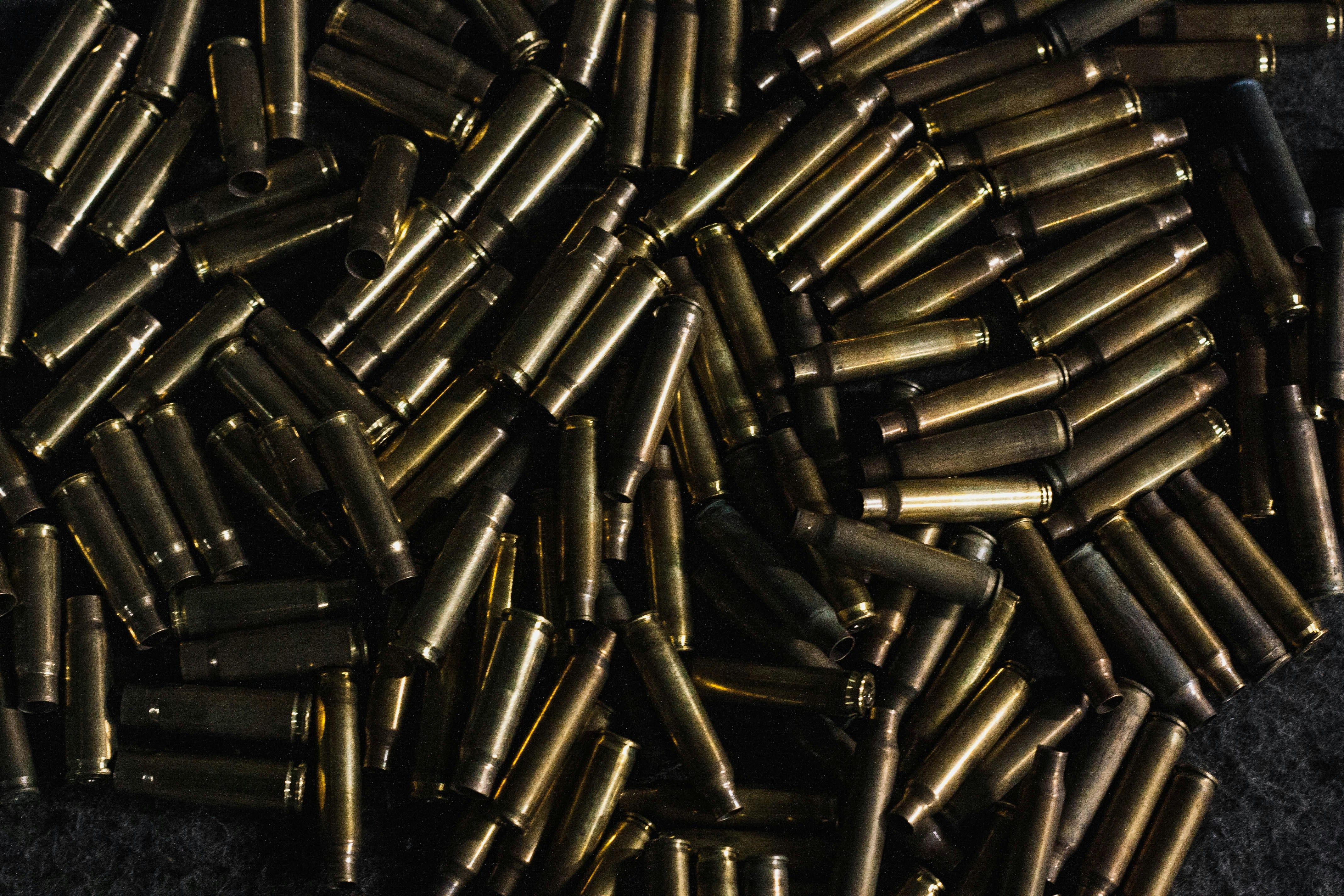
The rise of automatic hydraulic presses has transformed modern manufacturing. With embedded sensors, PLCs, and intelligent control systems, they deliver unmatched power, accuracy, and reliability at scale.
As industries increasingly adopt smart manufacturing and digital integration, automatic hydraulic presses have become indispensable to next-generation production lines.