Electrospinning is a fascinating process that utilizes electrical forces to produce ultra-fine fibers from a liquid polymer solution or melt. This innovative technology has gained widespread attention due to its versatility in various fields, including biomedical engineering, filtration, and nanotechnology. But what exactly is electrospinning, and how does it work? Let’s dive into the science behind this ground-breaking technique.
What Is Electrospinning?
Electrospinning is a fibre production technique that employs an electrostatic force to draw charged threads of polymer solutions or melts into nanometre- or micrometre-scale fibres. Unlike conventional fibre production methods, electrospinning can create extremely fine fibres with high surface-area-to-volume ratios, making them ideal for specialized applications. The Electro Spinner plays a crucial role in ensuring precise control over fibre formation and deposition.
The Basic Principles of Electrospinning
The electrospinning process is based on the interaction between electrical charges and the fluid dynamics of polymer solutions. The fundamental elements required for an electrospinning setup are:
A High-Voltage Power Supply – This provides the necessary electric field to initiate fibre formation.
A Polymer Solution or Melt – A carefully prepared liquid polymer solution or molten polymer serves as the raw material for fibre production.
A Syringe and Needle or Spinneret – The polymer solution is loaded into a syringe and pushed through a fine needle or nozzle to form a droplet.
A Collector (Grounded Substrate) – As fibres are drawn out, they are collected on a surface, forming a nonwoven mat or structured nanofibrous material.
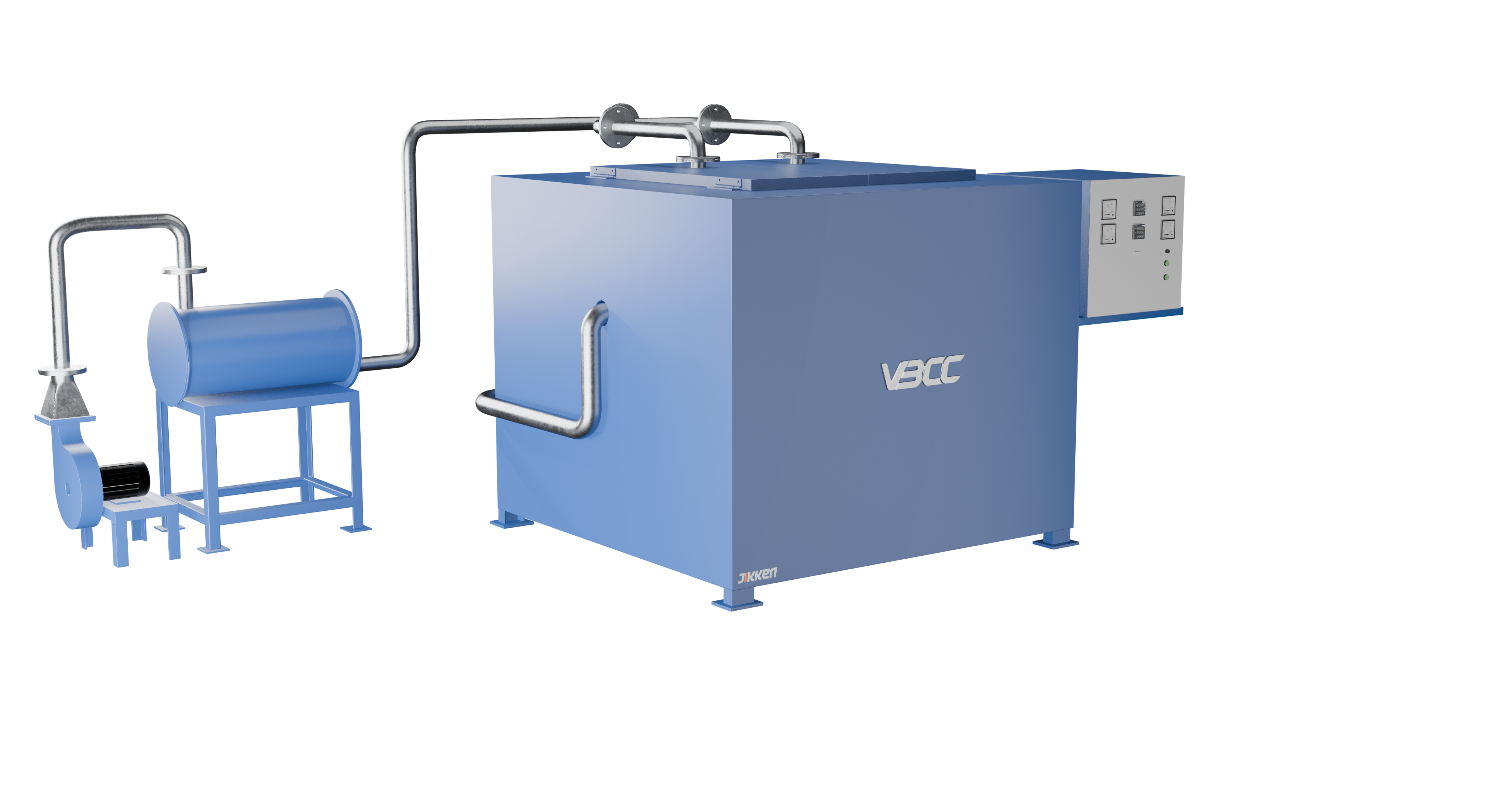
The Electrospinning Process: Step-by-Step
The process of electrospinning involves the following key stages:
Charge Induction: A high-voltage power supply creates an electric field between the polymer solution and the collector.
Formation of a Taylor Cone: As the voltage increases, electrostatic forces overcome surface tension, and the polymer droplet at the needle tip elongates into a cone-like shape, known as a Taylor cone.
Jet Initiation and fibre Formation: A charged polymer jet is ejected from the tip of the Taylor cone. As it travels through the air, it undergoes stretching and elongation due to electrostatic repulsion.
Solvent Evaporation or Solidification: As the fibre travels toward the collector, the solvent evaporates (or, in the case of melts, cools and solidifies), forming continuous fibres.
Deposition on the Collector: The nanofibers accumulate on the grounded collector, creating a nonwoven fibrous mat or other structured formations.
Factors Influencing Electrospinning
Several parameters affect the outcome of the electrospinning process, including:
Solution Properties: Polymer concentration, viscosity, and conductivity play a crucial role in fibre formation.
Voltage: Higher voltage generally results in thinner fibres but must be optimized to avoid jet instability.
Flow Rate: The rate at which the polymer solution is fed into the system affects fibre diameter and morphology.
Distance Between Needle and Collector: The gap between the spinneret and collector influences fibre uniformity and solvent evaporation.
Environmental Conditions: Temperature, humidity, and air flow can impact fibre formation and quality.
Applications of Electrospun fibres
The ability to create nanofibers with high porosity and surface area has led to numerous applications, including:
Biomedical Uses: Electrospun fibres are used in tissue engineering, wound dressings, and drug delivery systems.
Filtration: Nanofiber membranes enhance air and liquid filtration efficiency.
Energy Storage: Electrospun materials are employed in battery separators and fuel cell components.
Textiles: Smart and functional textiles benefit from the lightweight and breathable nature of electrospun fibres.
Sensors and Electronics: Conductive nanofibers are integrated into flexible electronic devices.
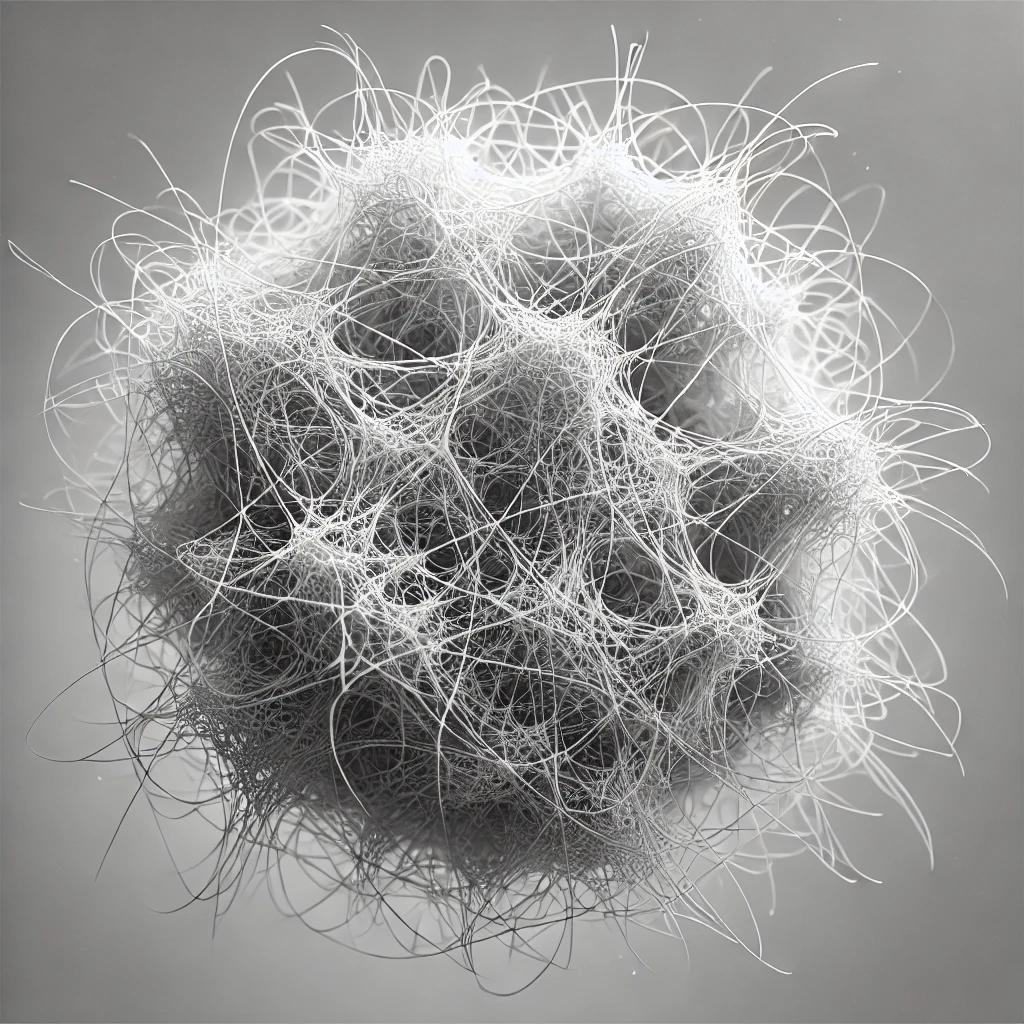
The Future of Electrospinning
Electrospinning continues to evolve, with researchers exploring new materials, hybrid structures, and scalable production techniques. Advances in 3D electrospinning, core-shell fibre structures, and bio-inspired designs are opening up new possibilities for this technology. The Electro Spinner is expected to play a key role in these advancements, offering greater precision and efficiency in nanofiber fabrication. As it matures, electrospinning is poised to revolutionize industries ranging from healthcare to environmental sustainability.
Electrospinning is a powerful and versatile technology with a solid scientific foundation. By leveraging electrostatic forces to create ultra-fine fibres, this technique has paved the way for ground-breaking innovations in medicine, filtration, energy storage, and beyond. As research continues, electrospinning is set to play an even more significant role in shaping the future of advanced materials and nanotechnology.