In industries where precision coating is essential, spin coating and dip coating are two widely used techniques for applying thin films. Both methods offer unique advantages depending on the application, material properties, and desired coating thickness. Now let’s compare these two techniques, exploring their working principles, advantages, and industry-specific applications to know which one is the best fit for your needs.
Understanding Spin Coating
Spin coating is a widely used method for applying thin films by spreading a liquid coating solution across a substrate using centrifugal force. The spin coating machine applies the liquid, and the substrate is rotated at high spin speed, allowing excess material to be flung off, leaving behind a uniform layer.
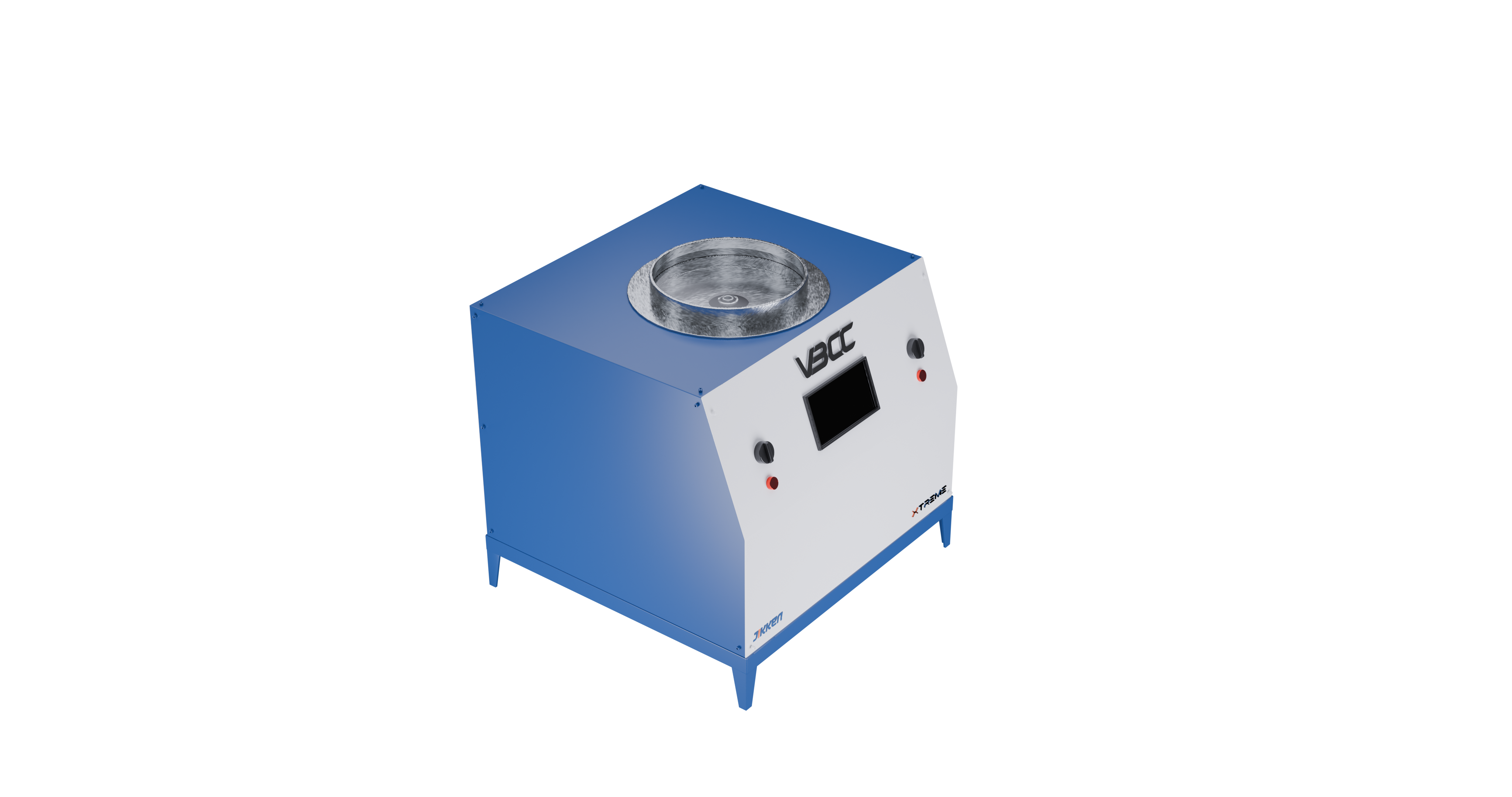
Advantages of Spin Coating:
- Highly uniform coatings – Ideal for applications requiring precision
- Controlled thickness – Thickness can be adjusted by modifying spin speed and solution viscosity
- Fast processing – A single coating cycle takes only a few seconds
Applications of Spin Coating:
- Semiconductor Industry: Used for depositing photoresists in microfabrication. This technique is critical in creating intricate microcircuit patterns on semiconductor wafers, ensuring high-resolution and defect-free coatings.
- Optoelectronics: Essential for applying uniform coatings on OLED displays. It is used in the fabrication of LEDs, solar cells, and optical coatings to enhance efficiency and durability.
- Biomedical Field: Used for coating biosensors and lab-on-chip devices. The ability to deposit bio-compatible and functional coatings makes spin coating a crucial process in drug delivery systems and diagnostic equipment.
- Nanotechnology: Used for preparing nanostructured thin films in research and development. Researchers use spin coating to fabricate thin-film coatings for applications in nanoelectronics, plasmonics, and MEMS devices.
- Photovoltaic Industry: Utilized in the development of thin-film solar cells. By ensuring an even distribution of active materials, spin coating enhances the efficiency of solar energy conversion.
Understanding Dip Coating
Dip coating involves immersing a substrate into a liquid solution and then slowly withdrawing it, allowing a film to form as the solvent evaporates. The thickness of the coating depends on several factors, including immersion time, withdrawal speed, and solution viscosity. A complete dip-coating cycle consists of immersion, dwelling, withdrawal, and drying.
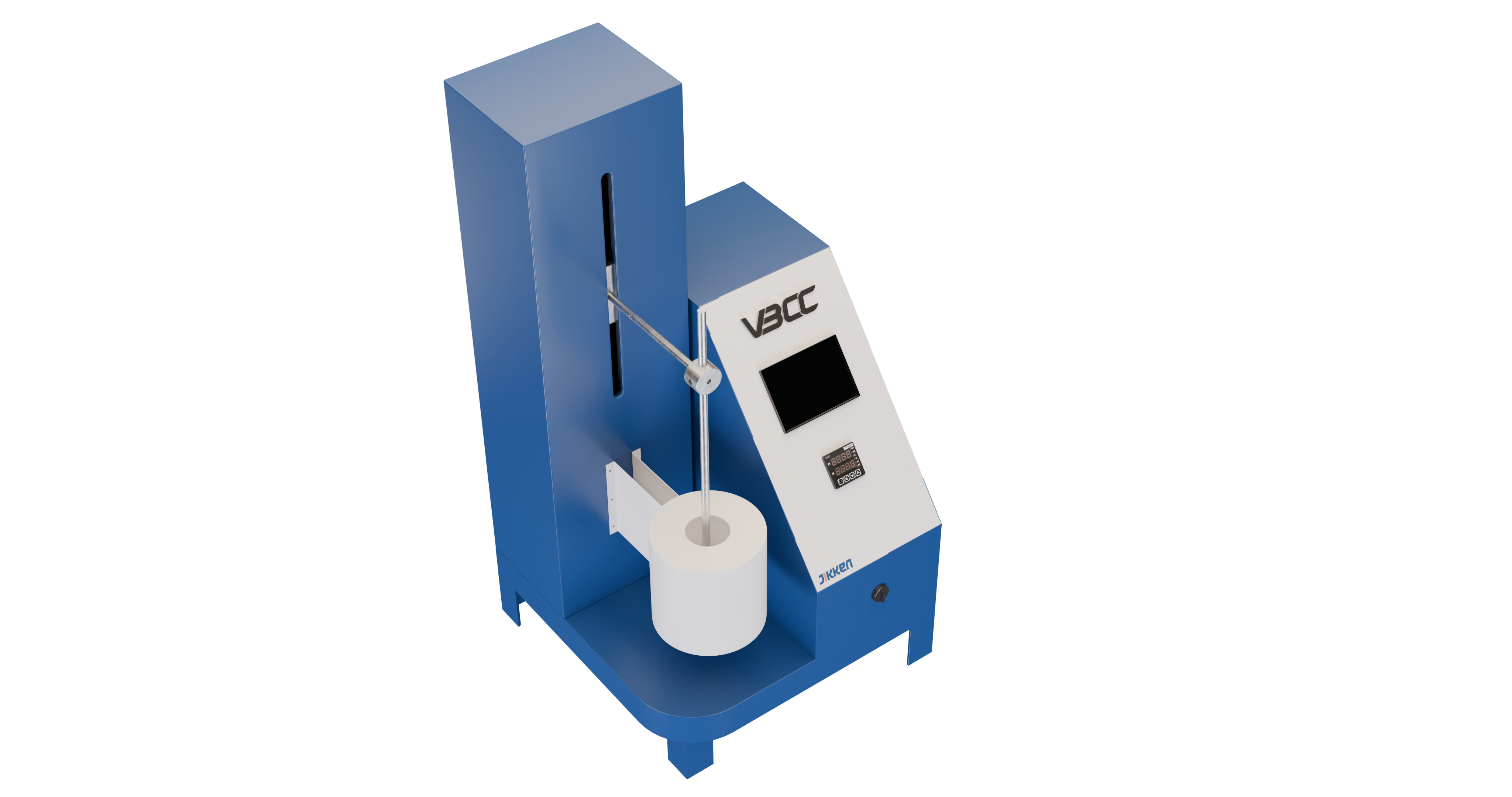
Advantages of Dip Coating:
- Scalability – Suitable for large-area coatings and bulk production
- Better material utilization – Less waste compared to spin coating
- Ability to coat complex geometries – Ideal for 3D structures
Applications of Dip Coating:
- Automotive Industry: Used for anti-corrosion coatings on metal parts. Dip coating is widely applied to automotive components such as chassis, fasteners, and underbody protection to prevent rust and enhance durability.
- Glass Manufacturing: Commonly used for anti-reflective and hydrophobic coatings. It improves the optical clarity of lenses, windows, and mirrors while also providing water-repellent properties.
- Medical Devices: Applied for biocompatible coatings on implants and surgical tools. Dip coating ensures an even and controlled deposition of antimicrobial or drug-eluting coatings for implants like stents and catheters.
- Textile Industry: Used for functional coatings such as water repellency and antimicrobial properties. Dip-coated fabrics are used in protective clothing, outdoor gear, and medical textiles.
- Electronics Industry: Applied for conformal coatings on circuit boards to protect against moisture and contaminants. Dip coating helps extend the lifespan and reliability of sensitive electronic components.
Key Differences Between Spin Coating and Dip Coating
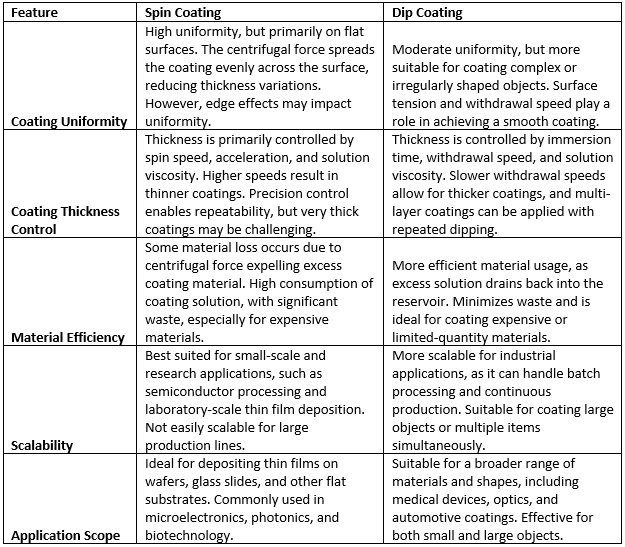
Which Coating Technique Should You Choose?
The choice between spin coating and dip coating depends on your specific requirements:
- Choose Spin Coating If: You need precise, ultra-thin, and highly uniform coatings, especially in semiconductor and optoelectronics industries.
- Choose Dip Coating If: You require scalable, cost-effective coatings on large or irregular surfaces, such as automotive parts and medical devices.
Both spin coating and dip coating are essential techniques for thin film applications, each excelling in different industrial contexts. Whether you prioritize uniformity, efficiency, or scalability, understanding the core differences will help you select the right method for your needs.