Extrusion technology is at the core of modern manufacturing — from plastic pipes and films to food products and pharmaceuticals. Two of the most commonly used machines in this domain are the single screw extruder and twin-screw extruder. While both are essential in material processing, each is better suited for specific applications based on material complexity, throughput, and processing requirements.
This blog explores the design, operation, advantages, and use cases of both single screw extruder machines and twin-screw extruder machines to help you make an informed decision for your production line.
What is a Single-Screw Extruder?
A single screw extruder serves as a basic yet widely adopted tool in the field of polymer processing. It is primarily used to convert raw plastic or other thermoplastic materials into continuous shapes such as films, pipes, profiles, sheets, and granules through a process of melting, conveying, and shaping.
This equipment contains a single screw that rotates inside a barrel with regulated temperature. It’s simple yet effective design makes it ideal for applications requiring consistent output and minimal material complexity. For many standard applications, a single screw extruder machine offers a cost-effective and reliable solution.
Components of a Single-Screw Extruder
- Hopper – Serves as the starting point for raw materials like pellets, powder, or granules, which are gravity-fed into the barrel.
- Screw and Barrel – Divided into feed, compression, and metering zones for optimal melting and pressure control.
- Drive Motor and Gearbox – Provides variable torque and speed to enable accurate control of material flow.
- Heaters and Temperature Control – Ensures thermal stability along the barrel for consistent melt quality.
- Die Head – Shapes the material into its final product form.
- Cooling System – Manages temperature using air or water-cooling systems.
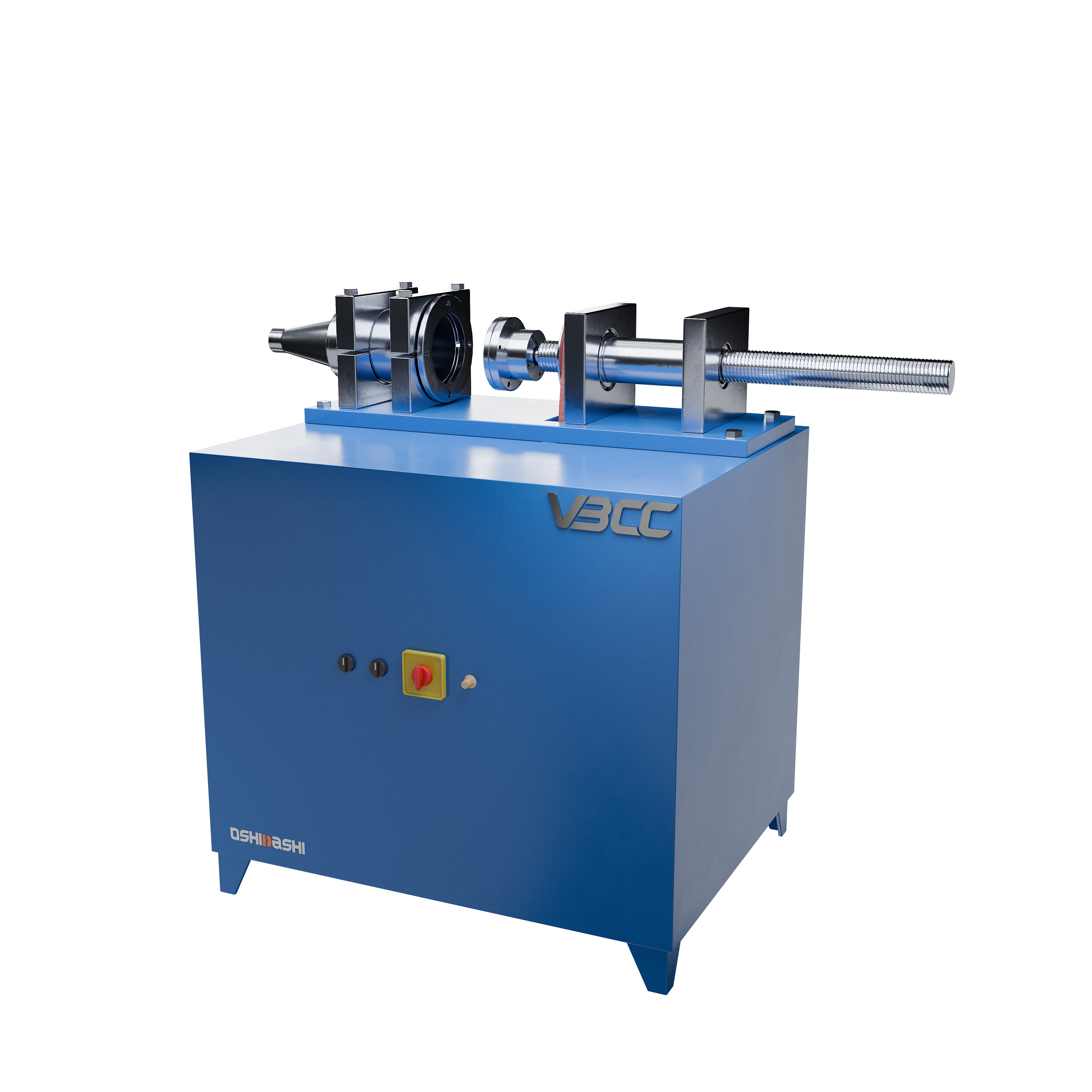
Working Principle
Raw material enters through the hopper and is driven along the barrel by the screw's rotation. As it progresses, it is compressed and melted through a combination of thermal energy and mechanical force. The processed material is driven through a custom die to mold it into its final shape.
Typical Applications
- Pipe and profile extrusion
- Film and sheet extrusion
- Granule and pellet production
- Basic plastic recycling
Many single screw extruder manufacturers cater to industries that need economical machines for high-throughput applications with simple raw materials. The single screw extruder price is generally lower than that of a twin-screw, making it attractive for start-ups and budget-conscious operations.
What is a Twin-Screw Extruder?
A twin-screw extruder operates with two interlocking screws that rotate within a barrel, allowing it to handle various types of materials efficiently. This type of extruder excels in mixing, compounding, devolatilization, and reactive processing, making it the preferred choice for advanced or multi-component formulations.
Twin-screw extruders are extensively utilized in various industries, including plastics, chemicals, food, pharmaceuticals, and biodegradable products, due to their versatility and accurate processing control. Leading twin screw extruder manufacturers offer machines tailored for specific processing needs, including co-rotating and counter-rotating designs.
Components of a Twin-Screw Extruder
- Twin Screws – Modular and intermeshing for superior mixing; available in co-rotating and counter-rotating configurations.
- Barrel – Designed with separate zones that can be customized for heating, cooling, and venting.
- Feed System – Allows for precise multi-material input through gravimetric or volumetric feeders.
- Drive Motor and Gearbox – Regulates the torque and rotational speed of the screws.
- Temperature Regulation – Ensures consistent heat distribution and thermal stability throughout the barrel.
- Venting Zones – Removes volatiles, moisture, and gases for high-quality melt.
- Die Head – Shapes the output into strands, sheets, pellets, or direct products like food shapes or pharmaceutical forms.
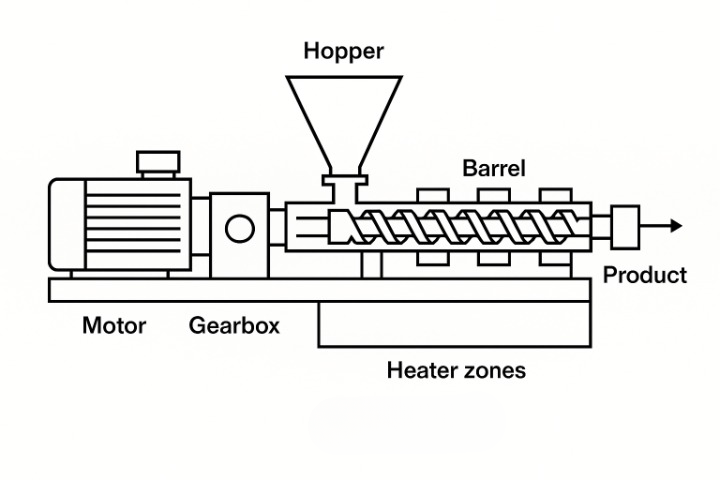
Working Principle
Material is fed into the twin barrel system and is transported, sheared, and mixed by the two screws. The system promotes better dispersion, homogenization, and degassing compared to single-screw machines. Final shaping is done through the die as the material exits.
Typical Applications
- Compounding and masterbatch production
- Biopolymers and heat-sensitive materials
- Reactive extrusion processes
- Food and pet food manufacturing
- Pharmaceutical extrusion
While the twin screw extruder price is typically higher, the machine offers unmatched process control, modularity, and mixing efficiency— essential for sophisticated applications.
Advantages of Single-Screw Extruders
- Lower cost and simpler design
- Easy maintenance and operation
- Ideal for homogeneous material processing
- Energy-efficient for basic extrusion needs
Advantages of Twin-Screw Extruders
- Superior mixing, dispersing, and melting
- Modular design allows for process customization
- Handles heat-sensitive or filler-heavy formulations
- Excellent venting and devolatilization capability
- Enhanced adaptability for complex or reactive multi-stage processing
When to Choose Which?
Choose a Single-Screw Extruder if:
- You're working with basic thermoplastics
- Your products include pipes, films, sheets, or simple profiles
- You need a cost-effective solution with low maintenance
- Priority is given to output volume over formulation intricacy
Choose a Twin-Screw Extruder if:
- You're processing blends, additives, or filled materials
- You need high mixing efficiency and thermal precision
- You’re in food, pharma, or biodegradable plastics sectors
- You require advanced control features like venting, multiple feeders, or reactive zones
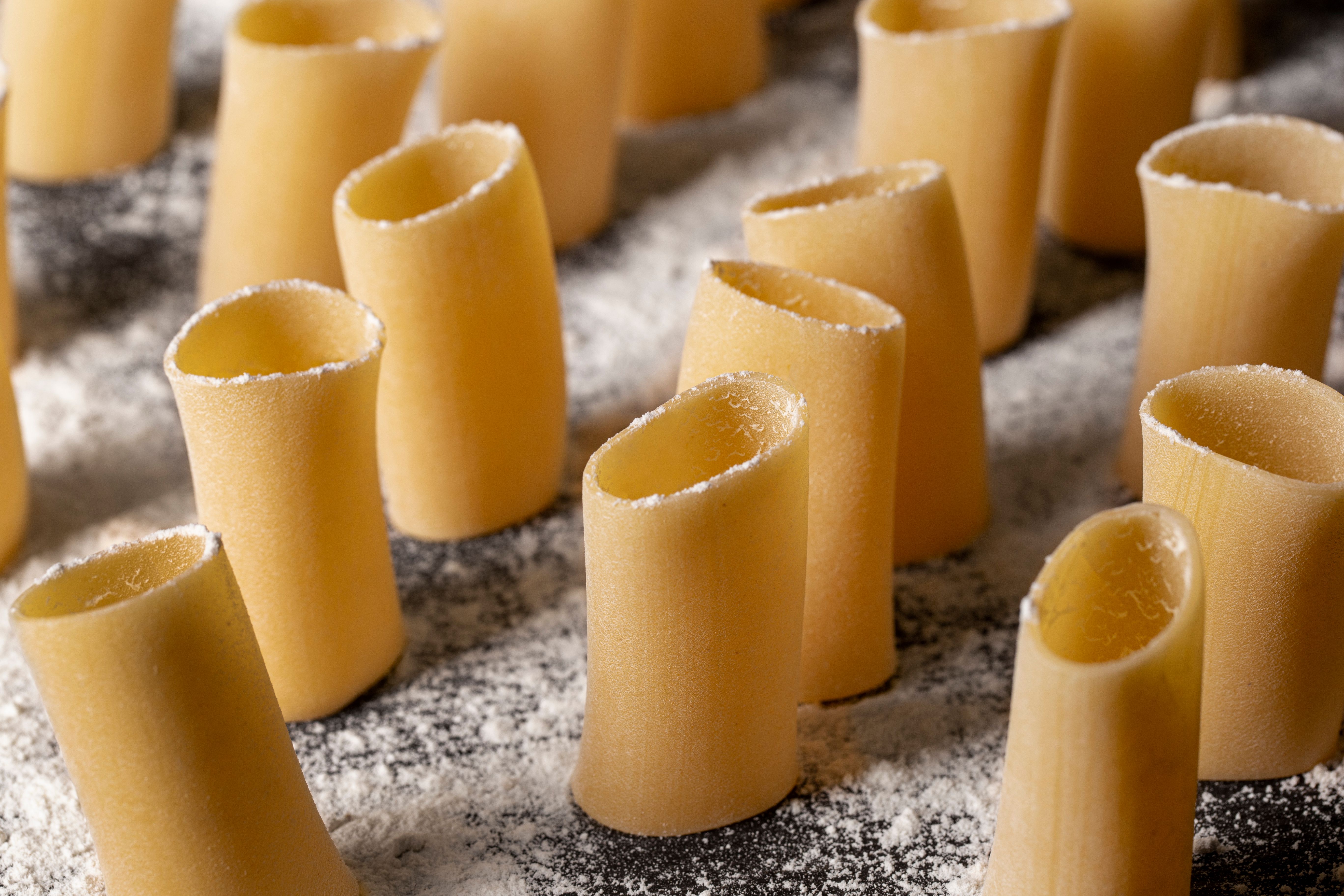
Emerging Trends in Extrusion
- The shift toward sustainable materials (e.g., recycled plastics and biopolymers) is increasing the demand for twin-screw systems.
- Smart extruders equipped with IoT and AI capabilities are being developed for predictive maintenance and real-time optimization.
- High-speed single screw extruder machines with enhanced screw geometries are evolving to improve output and reduce energy consumption.
Both single-screw and twin-screw extruder systems each play a vital role in today’s manufacturing processes. Selecting the appropriate option relies on your unique production requirements, material characteristics, and long-term objectives.
While single screw extruder machines offer simplicity and cost-effectiveness, twin screw extruder machinesprovide superior performance for complex, multi-phase processes. Whether you're comparing the twin screw extruder price for a high-end compounding line or researching single screw extruder manufacturers for a standard extrusion setup, understanding the capabilities of each system is key to choosing the best solution for your operation.