Rotary Tubular Furnaces are essential for high-temperature material processing, offering uniform heating and continuous operation. Choosing the right furnace for your application ensures efficiency, precision, and cost-effectiveness. In this guide, we will explore the key factors to consider when selecting a Rotary Tubular Furnace.
1. Understand Your Application Requirements
Before selecting a Rotary Tubular Furnace, it’s crucial to have a clear understanding of your specific application. This involves assessing various factors such as the type of material you are processing, the required process, and the scale of production. Key considerations include:
- Material Type: The type of material being processed significantly influences the furnace choice. Materials such as metals, ceramics, powders, and composites each have different heating requirements. For instance, metals often require higher temperatures and controlled atmospheres to prevent oxidation, while ceramics may require different temperature profiles and support for sintering processes.
- Process Type: Identify the type of process the furnace will be used for, such as sintering, calcination, heat treatment, or drying. These processes can vary greatly in temperature range, atmosphere control, and duration, all of which will influence furnace selection.
- Atmosphere Control: Consider whether your process requires an inert, oxidizing, or reducing atmosphere. Inert atmospheres are often used for materials sensitive to oxidation, while reducing atmospheres are needed for applications like carburization or metal reduction.
- Throughput & Production Scale: Determine the scale of your operations and the furnace’s required throughput. If you are scaling up production, a Rotary Tubular Furnace with a higher processing capacity and automation features will be necessary to meet demand without compromising quality or speed.
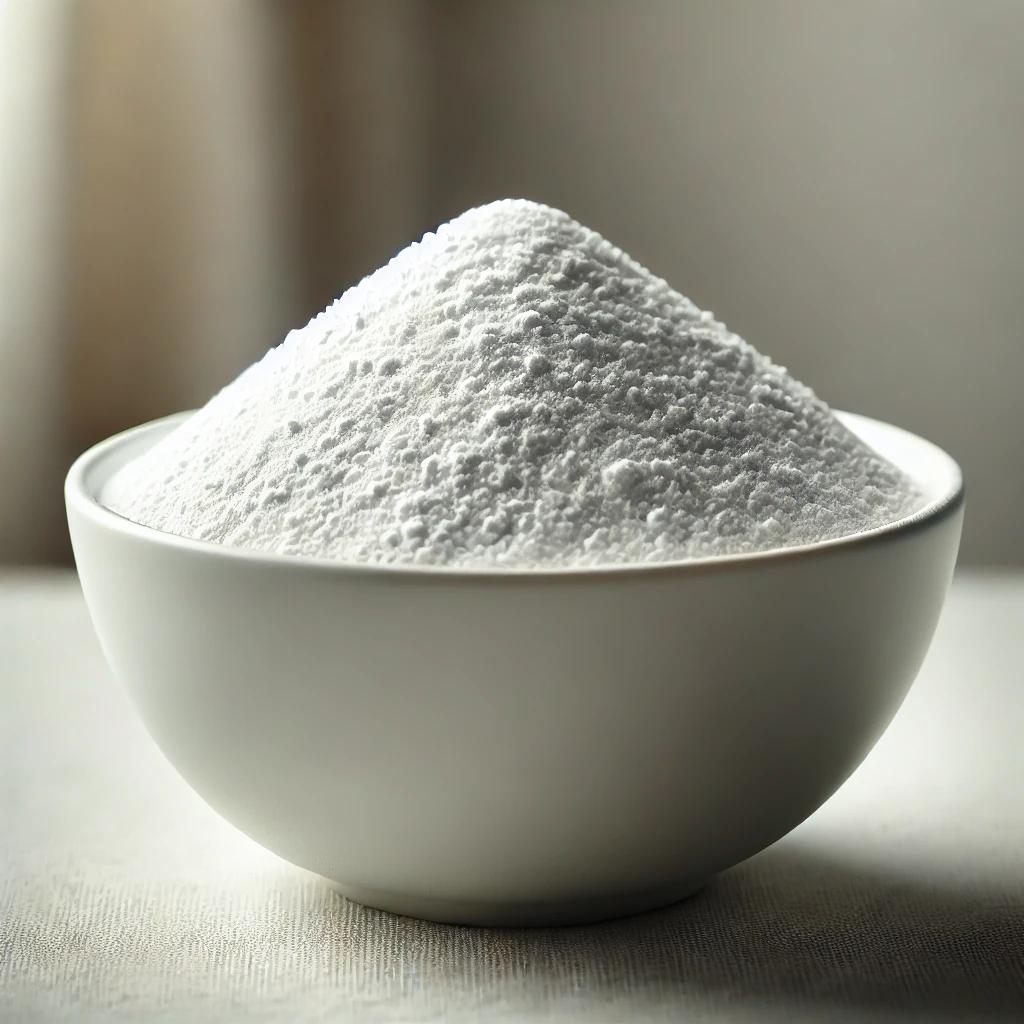
2. Temperature Range and Heating Elements
The temperature range needed for your application directly impacts the type of Rotary Tubular Furnace and heating elements you should choose. Different furnaces are suited for different temperature requirements:
- Low-Temperature Furnaces (Below 1000°C): Suitable for applications like drying, low-temperature treatments, and some sintering processes that don't require high heat.
- Medium-Temperature Furnaces (1000–1300°C): Ideal for processes like sintering, catalyst processing, or heat treatment of certain metals and ceramics.
- High-Temperature Furnaces (Above 1300°C): Needed for high-performance materials, advanced ceramics, and powder metallurgy processes that demand precise temperature control at elevated temperatures.
The heating elements used in these furnaces also vary according to the temperature range. Options include:
- Silicon Carbide: Commonly used for medium to high-temperature applications.
- Molybdenum Disilicide: Effective for high-temperature applications but can be more expensive.
- Tungsten: Used for extremely high-temperature processes but has limitations based on material and atmosphere compatibility.
3. Tube Design & Rotation Mechanism
The design of the rotary tube plays a key role in ensuring the furnace’s efficiency, as it directly impacts material flow, uniform heating, and consistency of the process. Key factors to consider include:
- Tube Material: Choose materials that are compatible with the specific chemical nature of the materials being processed. Quartz tubes are often used for their inertness, while ceramic or metal tubes may be selected for their higher temperature resistance.
- Tube Diameter & Length: These dimensions influence the residence time of materials inside the furnace and the effectiveness of heat distribution. Larger diameters are suited for materials that require longer processing times or need more space for mixing.
- Rotation Speed & Angle: The tube’s rotation speed and angle are crucial for ensuring uniform mixing of the materials inside. Adjustability is important to prevent material sticking or uneven heating, which can lead to inconsistent results.
4. Atmosphere & Gas Flow Control
Many processes require a controlled atmosphere to either prevent oxidation or to enable specific reactions. A Rotary Tubular Furnace should offer the following features for optimal control:
- Inert Atmosphere (Nitrogen, Argon): Required for materials that are reactive with oxygen, such as metals in powder form.
- Reducing Atmosphere (Hydrogen, CO/CO2 Mix): Needed for applications like metal reduction or carburization, where a reducing environment helps to achieve the desired chemical transformation.
- Controlled Gas Flow System: A robust gas distribution system ensures that the desired atmosphere is uniformly maintained throughout the process. Look for features such as gas flow regulation and contamination prevention to ensure consistent results.
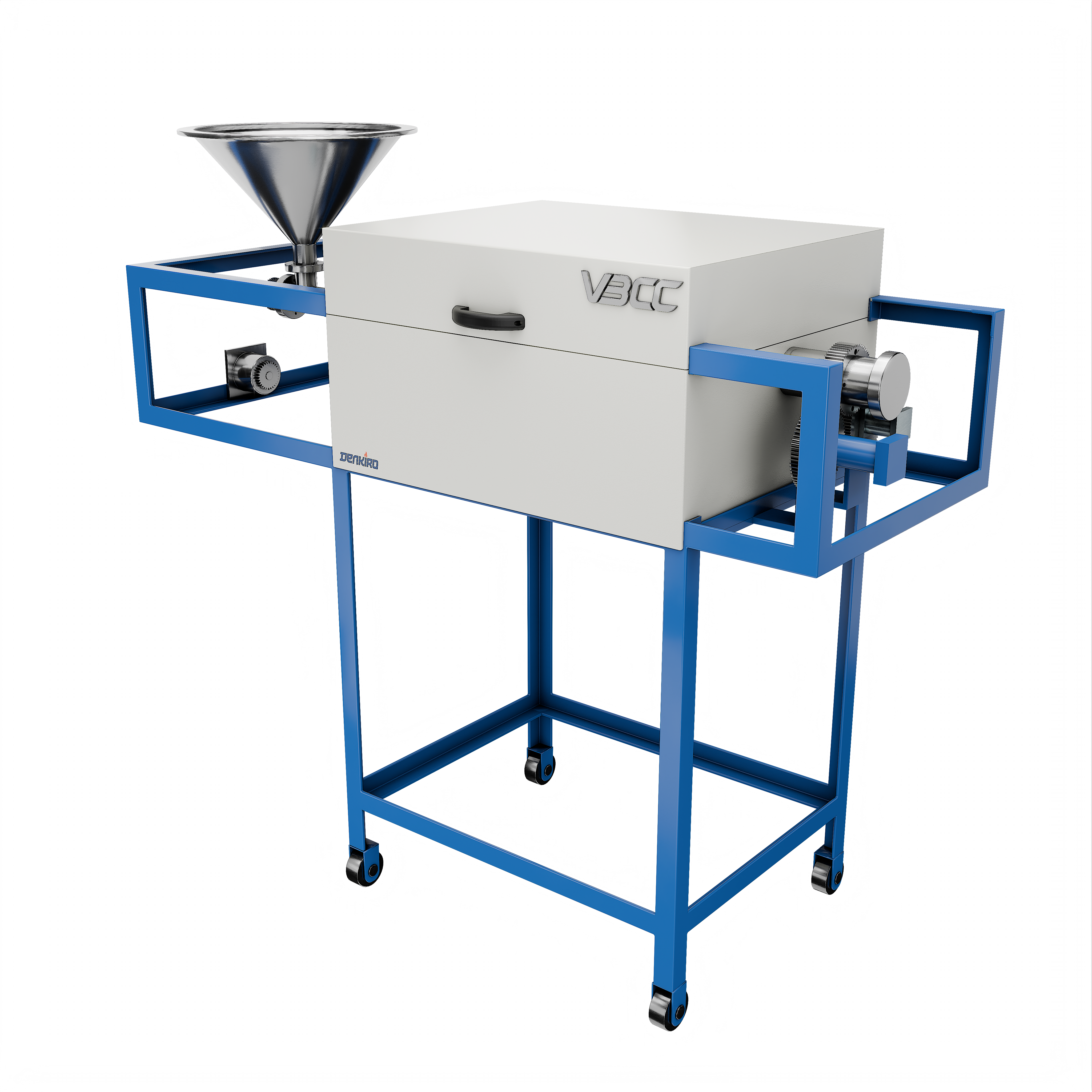
5. Automation & Process Control
Automation and advanced process control features enhance the precision and efficiency of Rotary Tubular Furnaces. Consider the following:
- Programmable Logic Controllers (PLC): PLCs enable precise control of temperature, speed, and other process parameters. They offer flexibility and precision, helping to optimize the furnace’s performance and reduce human error.
- Touchscreen Interfaces: Modern furnaces often come with user-friendly interfaces that allow for real-time monitoring and easy adjustments. These systems provide clear displays of operational parameters and can help streamline workflow.
- Data Logging & Remote Access: Many advanced Rotary Tubular Furnaces are equipped with data logging systems that track performance over time. Remote access options allow operators to monitor the furnace from a distance, ensuring quick responses to potential issues and better performance tracking.
6. Energy Efficiency & Cost Considerations
Energy efficiency is a critical factor when selecting a Rotary Tubular Furnace, as it can have a significant impact on operational costs. Factors to consider include:
- Efficient Insulation: A well-insulated furnace minimizes heat loss, improving thermal efficiency and reducing energy consumption. Proper insulation ensures that the furnace can maintain high temperatures while using less power.
- Optimized Power Consumption: Features like energy-saving heating elements and adjustable power settings can help reduce energy usage without compromising performance.
- Initial Investment vs. Long-Term Savings: While high-end, energy-efficient furnaces may have a higher initial cost, they can result in lower long-term operational costs. Be sure to consider both the upfront investment and the savings in energy costs over the furnace's lifetime.
7. Customization & Support Services
Industries vary widely in their needs, and a one-size-fits-all approach may not work for every application. Customization options allow you to tailor the Rotary Tubular Furnace to your specific requirements. Key considerations include:
- Bespoke Designs: We offer custom tube dimensions, specialized heating elements, and automation systems to meet unique operational demands. Customization can ensure that the furnace performs optimally for your specific material processing requirements.
- After-Sales Support: It’s important for us to consider the level of support we offer as the furnace manufacturer. We ensure that our comprehensive after-sales services, including training, spare parts availability, and ongoing maintenance support, help guarantee the longevity and reliability of your equipment.
Choosing the right Rotary Tubular Furnace requires careful evaluation of several factors, including process requirements, temperature range, material compatibility, and energy efficiency. By considering these key aspects, you can select a furnace that not only enhances your productivity but also ensures consistent quality and operational efficiency in the long term.