In the field of material science and thermal analysis, the dilatometer stands out as a crucial tool for understanding how materials behave under varying temperature conditions. But how does a dilatometer work, and what are its key components? This post dives into the underlying principles and essential parts of this precision instrument.
What is a Dilatometer?
A dilatometer is a device designed to track how a material's dimensions vary in response to temperature shifts, time, or other environmental factors. In simple terms, a dilatometer is used to measure the expansion or contraction of a material — a phenomenon crucial in industries like aerospace, ceramics, metallurgy, and polymers.
The Principle Behind a Dilatometer
Dilatometers work on the basic principle that materials increase in size with heat and shrink when cooled. While these changes are often subtle, they can greatly influence performance in applications that demand high precision.
Dilatometry entails the continuous measurement of these dimensional changes over a wide temperature range, providing data that helps scientists and engineers to:
- Calculate the thermal expansion coefficient (CTE)
- Study phase transitions
- Analyse sintering behaviour
- Investigate glass transition temperatures in polymers
Key Components of a Dilatometer
To perform these sensitive measurements, a dilatometer consists of several critical components working in harmony:
1. Sample Holder
The sample holder is designed to securely position the test specimen within the instrument. It must maintain its structural integrity at high temperatures and have a well-characterized thermal expansion behaviour so it doesn’t distort test results.
- Material: Usually made from fused silica, alumina, or other thermally stable materials.
- Design Considerations: It must minimize thermal gradients and mechanical stress on the sample.
2. Push Rod or Probe
The push rod, sometimes referred to as the displacement probe, is a central component in dilatometry testing. It sits in contact with the specimen and transmits its dimensional changes to the measuring system.
- Material: Often made of low-expansion materials like quartz or alumina to avoid interfering with results.
- Function: Converts the sample’s physical expansion into linear motion that can be measured.
- Variants: Some systems use dual-rod setups for compensation and increased precision.
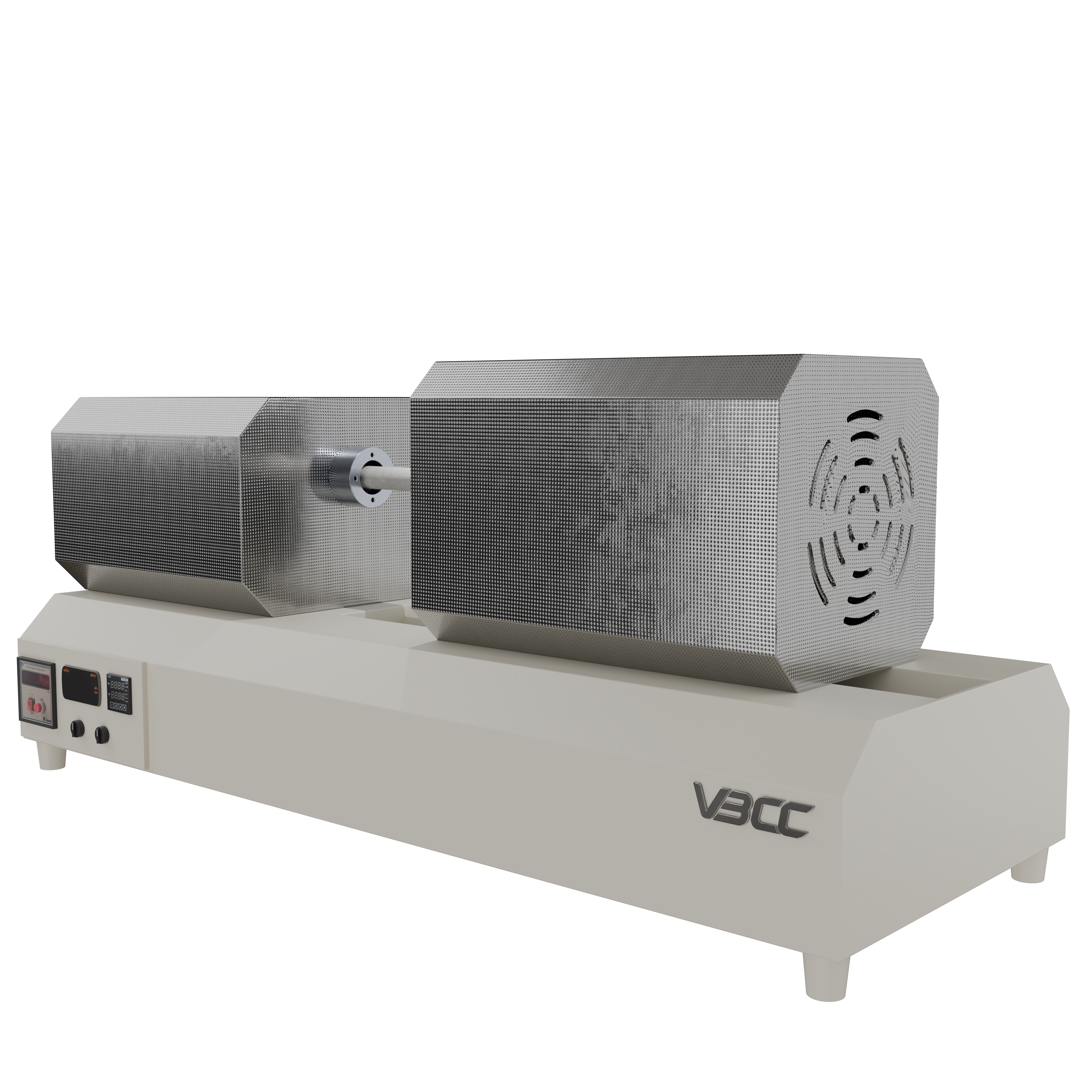
3. Furnace or Heating System
Thermal control is the foundation of dilatometry. The furnace or heating system provides a carefully controlled temperature environment to induce expansion or contraction in the sample.
- Temperature Range: Typically, from ambient temperature up to 1600°C or more.
- Heating Rates: Programmable for slow ramps or rapid thermal changes.
- Atmosphere Control: Some dilatometers include inert, oxidizing, or reducing atmospheres to simulate specific environments.
4. Displacement Sensor
The displacement sensor measures the minute movements transferred by the push rod as the sample’s length varies.
Types of Sensors:
- LVDT (Linear Variable Differential Transformer): Offers high precision with excellent thermal stability.
- Optical Encoders: Used in optical dilatometers for contact-free measurement.
- Capacitive or Inductive Sensors: Found in high-resolution, low-noise systems.
- Accuracy: Often capable of detecting changes as small as 10 nanometres.
5. Data Acquisition and Control System
This system acts as the brain of the dilatometer, collecting and processing signals from the displacement sensor while also managing the furnace temperature.
Features:
- Real-time curve plotting (e.g., length vs. temperature)
- Software for thermal expansion coefficient calculations
- Capturing and exporting data for use in reports and analytical evaluations
User Interface: Typically, computer-controlled with user-friendly software for method setup, calibration, and result interpretation.
6. Cooling System (Optional)
Many modern dilatometers include an integrated or external cooling system to control post-heating temperature profiles or enable low-temperature testing.
Types:
- Forced Air Cooling
- Water-Cooled Jackets
- Liquid Nitrogen Systems for sub-zero testing
Benefit: Enhances the versatility of dilatometry testing by enabling cyclic or rapid cooling experiments.
7. Atmosphere Control System (Optional)
For materials sensitive to oxidation, moisture, or reactive gases, some dilatometers include an atmosphere control module.
Functions:
- Create inert environments (e.g., argon or nitrogen)
- Simulate reducing or oxidizing conditions
- Vacuum compatibility for high-purity testing
Importance: Essential for testing metals, composites, and advanced ceramics under realistic process conditions.
Together, these components make up a sophisticated system capable of delivering accurate, high-resolution measurements across a broad range of materials and industries. Understanding each element helps researchers and engineers select the right configuration for their specific application and enhances the quality of dilatometry testing outcomes.
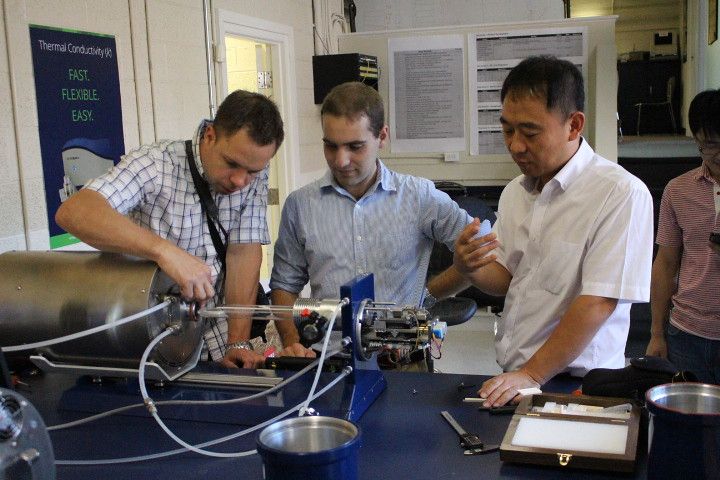
Types of Dilatometers
Dilatometers come in different varieties, each suited to distinct applications:
- Push-Rod Dilatometers: Most common, highly accurate, used for solids like metals and ceramics.
- Optical Dilatometers: Non-contact measurement using cameras or lasers, ideal for fragile or soft materials.
- Capacitance Dilatometers: High sensitivity, often used in low-temperature physics.
Applications of Dilatometry Testing
Dilatometry testing is utilized in multiple industries to address practical, real-world problems:
- Ceramics: Analysing shrinkage during sintering (To learn more, check out this blog from our friends at Ceramic Materials Workshop : Using a Dilatometer in Ceramics.)
- Metals: Analysing phase transitions and stress-relief characteristics
- Polymers: Measuring glass transition and softening points
- Electronics: Ensuring thermal compatibility of materials in multilayer devices
Understanding how a dilatometer works helps scientists and engineers make informed decisions when selecting materials for critical applications. From R&D labs to industrial production lines, dilatometry testing provides essential insights into thermal behaviour — ensuring safety, efficiency, and innovation.
As industries continue to push the boundaries of material performance, the role of dilatometers remains more relevant than ever.