Spray pyrolysis is a versatile and cost-effective technique widely used in material science to develop high-quality materials for diverse applications. This method allows for the deposition of thin films and coatings with precise control over composition, structure, and thickness, making it an invaluable tool in industries and research. Below, we explore three significant areas where spray pyrolysis has transformed material science: coating technologies, energy storage and battery research, and semiconductor advancements for photovoltaics.
Coating Technologies
Coatings play a critical role in enhancing the functionality and durability of materials. Spray pyrolysis provides an efficient way to create uniform and defect-free coatings on various substrates, including metals, ceramics, and polymers. This technique is employed in:
Protective Coatings: Spray pyrolysis produces corrosion-resistant and wear-resistant coatings for industrial equipment, extending their service life in harsh environments. These coatings are essential for machinery used in chemical plants, marine environments, and heavy-duty manufacturing, where resistance to corrosion and mechanical wear is crucial.
Optical Coatings: Anti-reflective and transparent conductive oxide coatings are applied to glass and lenses for applications in optics and displays. These coatings improve light transmission, reduce glare, and enhance the performance of devices such as cameras, solar panels, and electronic displays.
Thermal Barrier Coatings: These coatings, used in aerospace and power generation, protect components from extreme heat and improve thermal efficiency. Spray pyrolysis enables the deposition of multi-layered thermal barriers, ensuring durability and resistance to thermal cycling, which is critical for jet engines and gas turbines.
By fine-tuning parameters such as precursor concentration, spray rate, and temperature, researchers can optimize the coating properties for specific applications. This customization ensures that the coatings meet the stringent requirements of various industrial and technological fields.
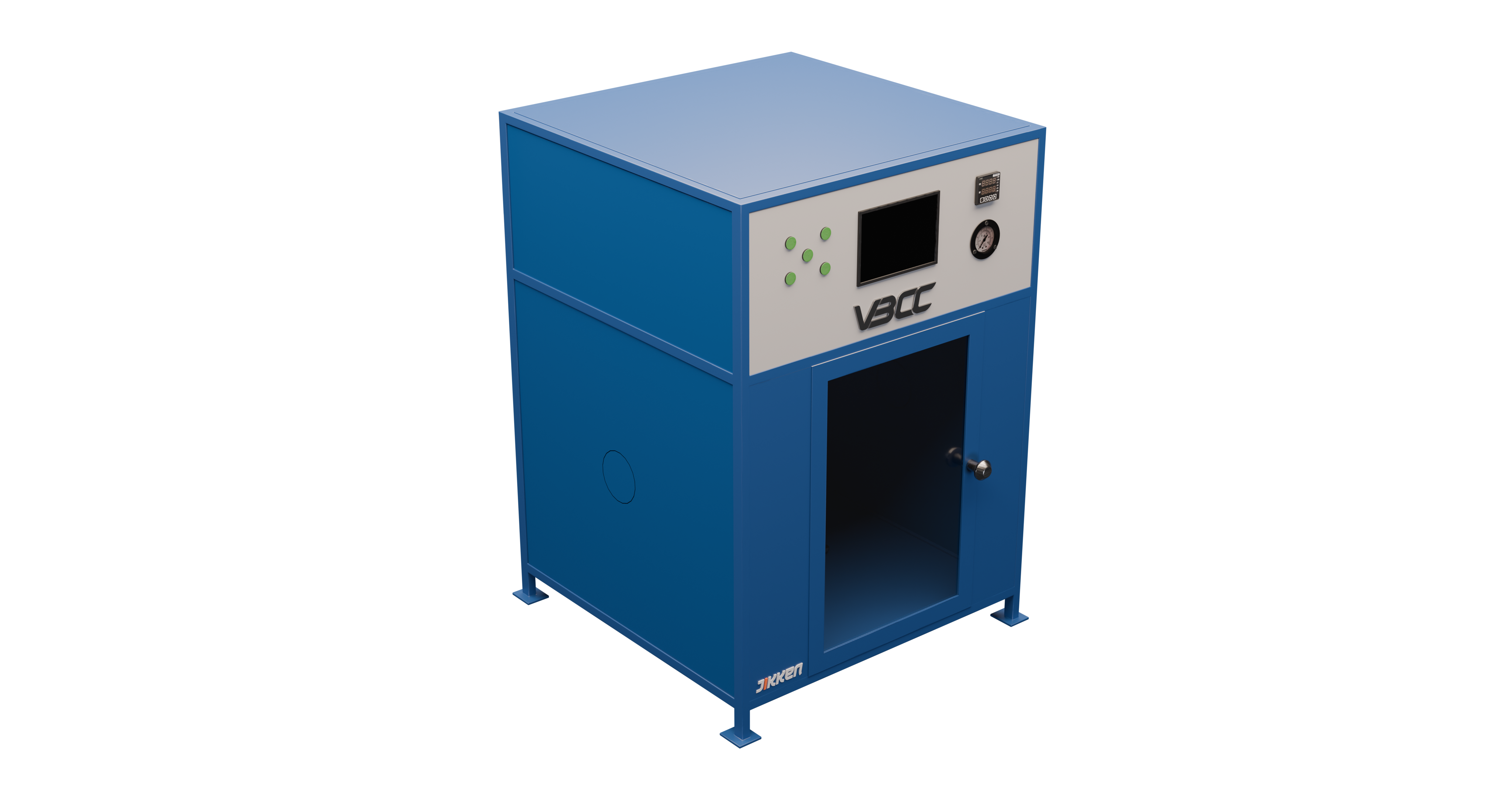
Energy Storage and Battery Research
The demand for efficient and sustainable energy storage systems has driven advancements in battery technology. Spray pyrolysis is pivotal in the fabrication of materials for batteries and supercapacitors due to its ability to produce:
Electrode Materials: High-performance electrodes, such as lithium cobalt oxide (LiCoO2) and nickel manganese cobalt oxide (NMC), are synthesized with uniform particle size and high purity. These materials exhibit enhanced electrochemical properties, such as higher capacity and improved stability, which are vital for next-generation batteries.
Solid Electrolytes: Spray pyrolysis enables the deposition of thin and dense solid electrolyte layers, essential for the development of next-generation solid-state batteries. These solid electrolytes eliminate the risks associated with liquid electrolytes, such as leakage and flammability, making batteries safer and more reliable.
Catalyst Coatings: Enhanced catalytic properties are achieved by creating uniform coatings for fuel cells and electrochemical devices. Spray pyrolysis ensures that the catalyst layer has a high surface area and optimal composition, improving the efficiency and longevity of energy conversion systems.
This technique allows for the scalable production of nanostructured materials with improved energy density, charge-discharge rates, and cycle stability. Such advancements are critical for powering electric vehicles, portable electronics, and renewable energy systems.
Semiconductor Advancements and Photovoltaics
The semiconductor industry relies on advanced material deposition techniques to develop efficient electronic devices. Spray pyrolysis has emerged as a key method for producing high-quality semiconducting films, particularly in:
Thin-Film Solar Cells: Spray pyrolysis is used to deposit light-absorbing layers, such as cadmium sulfide (CdS) and copper indium gallium selenide (CIGS), which enhance the efficiency of solar cells. These films ensure optimal light absorption and charge carrier mobility, leading to higher energy conversion efficiencies.
Transparent Conductive Films: These films, crucial for touchscreens, displays, and photovoltaic cells, are created with optimal transparency and conductivity. Spray pyrolysis enables the production of films with fine-tuned properties, ensuring minimal energy loss and excellent optical clarity.
Sensors and Detectors: Spray pyrolysis facilitates the fabrication of sensitive layers for gas sensors, photodetectors, and other optoelectronic devices. These layers can detect minute changes in environmental conditions, such as gas concentration or light intensity, making them ideal for precision applications in healthcare, security, and environmental monitoring.
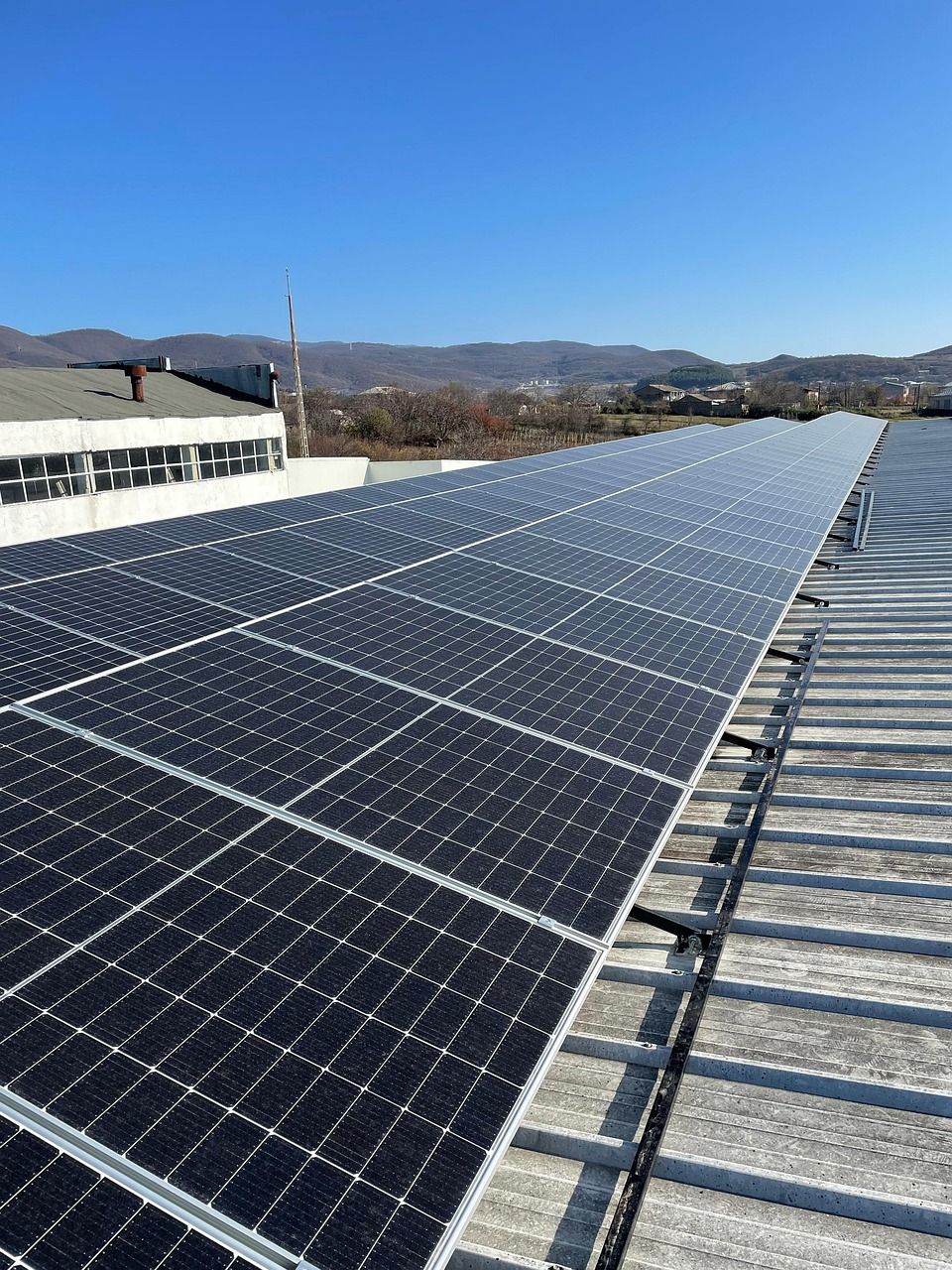
By enabling precise control over film morphology and composition, spray pyrolysis supports the development of innovative semiconducting materials for cutting-edge technologies. This versatility makes it a preferred choice for researchers and industries aiming to create advanced electronic and optoelectronic devices.
Spray pyrolysis is a transformative tool in material science, offering unparalleled flexibility and control for developing advanced materials. Its applications in coating technologies, energy storage, and semiconductor advancements continue to drive innovation and sustainability across industries. As research progresses, spray pyrolysis will undoubtedly remain at the forefront of material engineering, paving the way for new discoveries and technological breakthroughs.