Aluminium Stir Casting is one of the most widely used techniques for producing metal matrix composites (MMCs) — materials that combine the lightweight nature of aluminium with the enhanced properties of ceramic reinforcements. If you're new to materials science, manufacturing, or engineering, this guide will walk you through the basics of what aluminium stir casting is, how it works, and why it matters.
What is Stir Casting?
Stir casting is a liquid-state fabrication process where solid particles (usually ceramic) are stirred into a molten metal matrix, typically aluminium. Once mixed, the composite slurry is poured into a mould and allowed to solidify, forming a component that combines the properties of both the metal and the reinforcements.
It’s a simple, cost-effective, and scalable method — making it ideal for industrial applications.
Why Aluminium?
Aluminium is favoured in stir casting because it’s:
- Lightweight
- Corrosion-resistant
- Thermally and electrically conductive
- Relatively low-cost and abundant
When reinforced with particles like silicon carbide (SiC), alumina (Al₂O₃), or boron carbide (B₄C), aluminium’s properties can be significantly improved — particularly in strength, wear resistance, and stiffness.
The Stir Casting Process: Step by Step
Stir casting is a relatively straightforward but sensitive process that requires precision at every stage to ensure a high-quality composite. The following provides a detailed outline of the process steps:
1. Melting the Aluminium Matrix
The process begins with the selection and melting of the aluminium matrix alloy — commonly used grades include Al6061, Al7075, or Al2024. These alloys are selected based on the required properties of the final composite (e.g., corrosion resistance, strength, or machinability).
The aluminium alloy is placed in a crucible and heated in a resistance or induction furnace until it reaches its liquid state (typically between 660°C and 750°C).
Temperature control is crucial to ensure the alloy is fully molten without excessive oxidation.
2. Preheating the Reinforcement Particles
Reinforcement materials such as Silicon Carbide (SiC), Alumina (Al₂O₃), Graphite, or Boron Carbide (B₄C) are introduced into the matrix to improve properties like hardness, wear resistance, and strength.
The particles are generally heated to around 500–600°C before being introduced into the molten metal.
Why preheat?
- It removes moisture that could cause gas porosity.
- It reduces the temperature difference between the particles and the melt, minimizing thermal shock.
- It improves wettability, allowing particles to bond better with the molten aluminium.
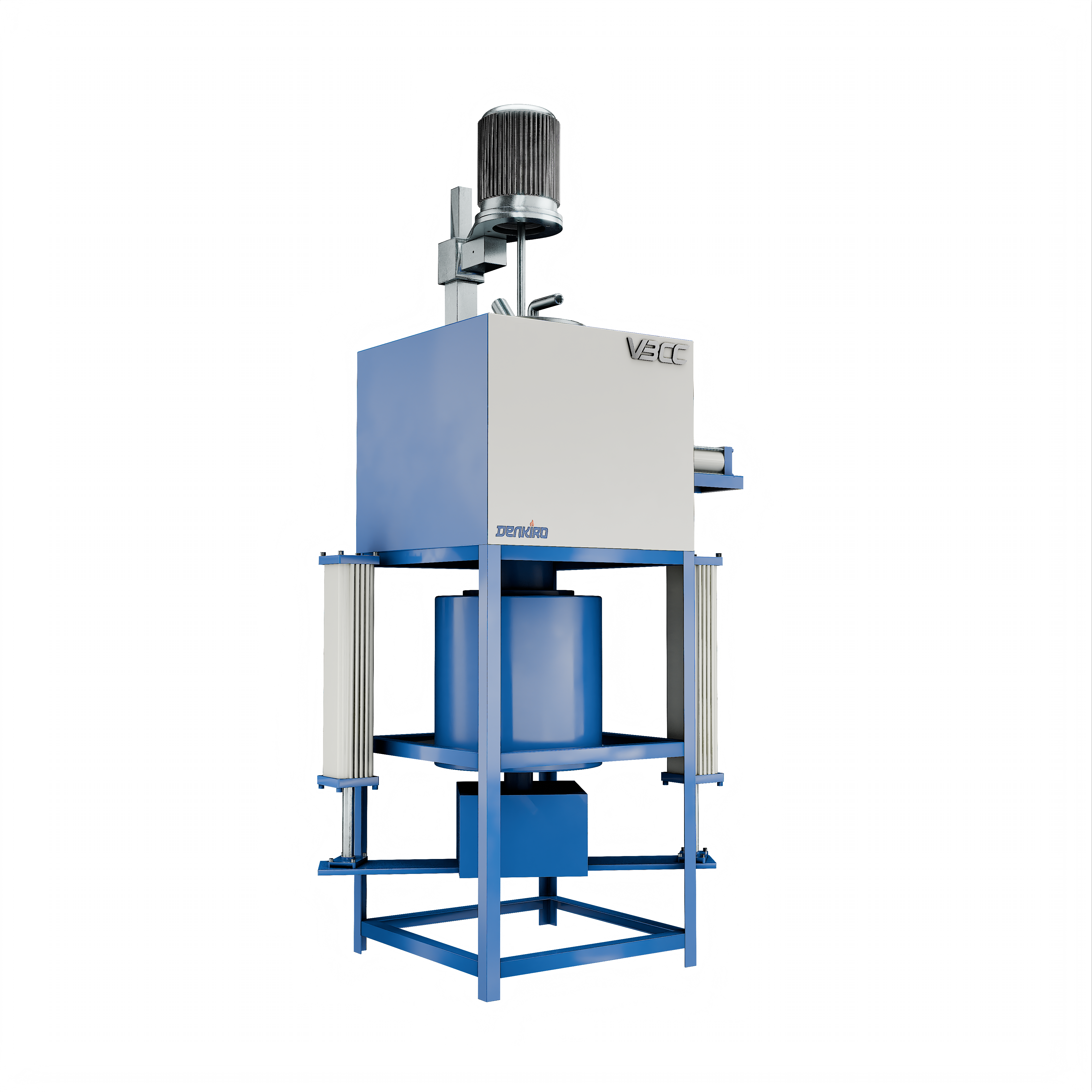
3. Mechanical Stirring of the Slurry
This is the core step of the stir casting process and determines how well the reinforcements are distributed in the aluminium matrix.
A mechanical stirrer(often graphite-coated or ceramic to resist high temperatures) is inserted into the crucible.
The molten metal is stirred at a regulated speed, usually between 300 and 600 rpm, for a defined period ranging from 3 to 10 minutes.
The stirring creates a vortex that helps draw the particles down into the molten matrix and ensures uniform distribution.
Certain systems utilize inert gas shielding, such as argon or nitrogen, to minimize oxidation while stirring.
4. Addition of Wetting Agents (Optional)
In cases where the reinforcement particles have poor wettability with aluminium (especially Nano-particles or certain ceramics), wetting agents like magnesium (Mg) are added.
Magnesium enhances the bonding at the interface between aluminium and reinforcement particles.
The amount typically ranges from 0.5% to 2% by weight, depending on the system.
5. Pouring into moulds
After the reinforcement has been evenly incorporated:
The molten composite is poured into pre-heated moulds, which can be metallic or sand-based, depending on the required surface finish and cooling rate.
Controlled pouring helps prevent turbulence, which could reintroduce air bubbles or cause segregation of particles.
6. Solidification and Cooling
The cast composite is allowed to cool and solidify under ambient or controlled conditions.
Solidification rate affects the microstructure: faster cooling often results in finer grains and better mechanical properties.
Once solidified, the casting is removed and cleaned of any surface slag or oxide layers.
7. Post-Processing (Optional)
Based on the intended use and desired quality standards, the casting process may include:
Heat treatment (e.g., T6 tempering for Al6061) to enhance strength.
Machining or applying surface treatments to achieve specific dimensions and visual appearance.
Conducting evaluation tests including hardness measurement, tensile testing, microstructural examination, and wear analysis.
Key Considerations During Stir Casting
Uniform stirring is essential to avoid agglomeration and settling of particles.
Oxidation must be minimized during melting and stirring.
Stirring tool design, depth, and placement affect the vortex and particle distribution.
Process parameters (temperature, speed, time) must be optimized for each material combination.
Applications of Aluminium Stir Cast Composites
Because of their enhanced mechanical and thermal properties, aluminium stir cast composites are used in:
- Automotive components (engine blocks, pistons, brake discs)
- Aerospace structures
- Sports equipment
- Defence applications
- Electrical enclosures and heat sinks
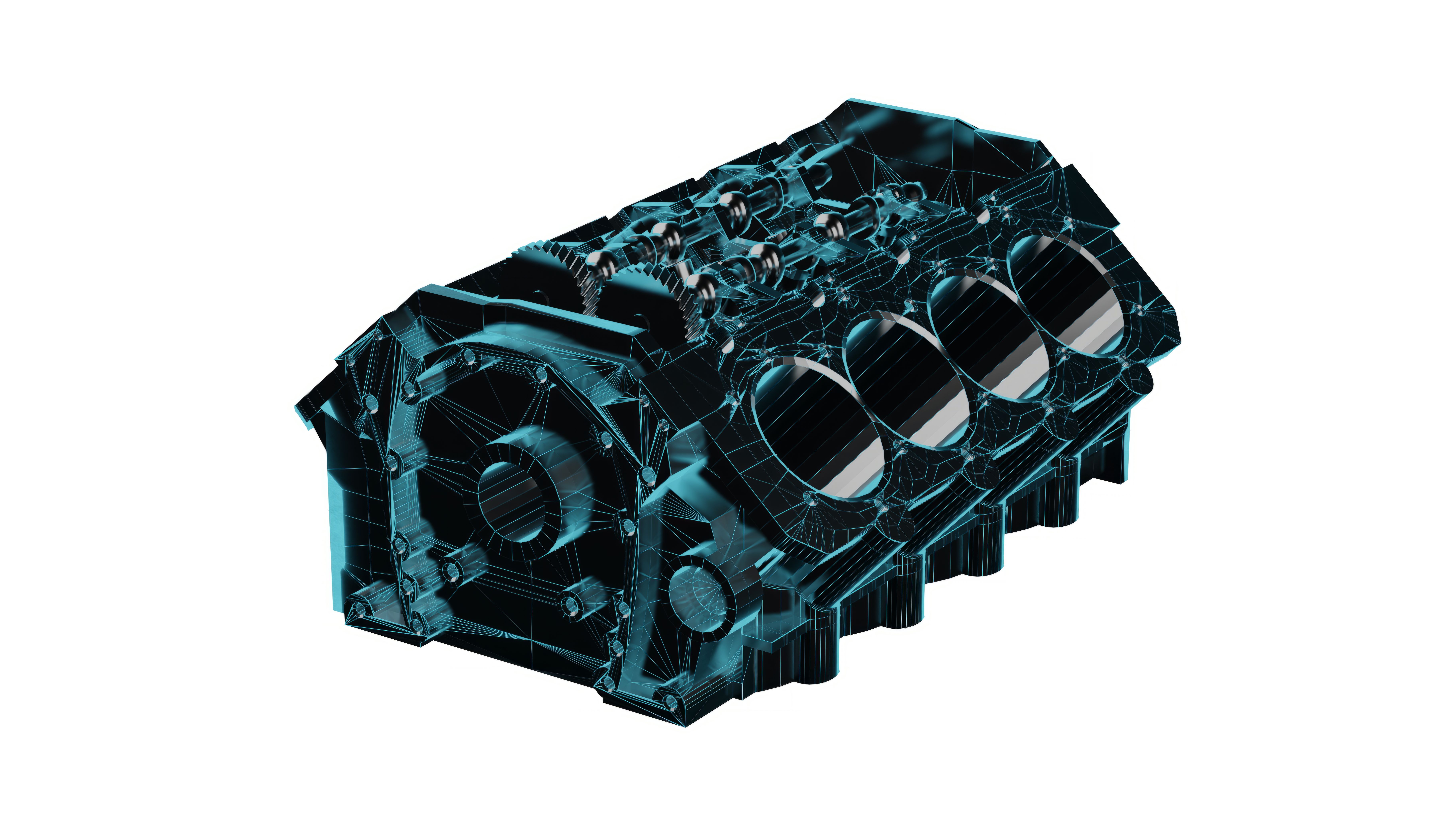
Benefits of Stir Casting
- Cost-effective: Compared to other composite manufacturing techniques like powder metallurgy or squeeze casting.
- Simple setup: No highly specialized equipment is required.
- Suitable for mass production
- Versatile: Can work with various reinforcements and matrix compositions.
Challenges and Limitations
- Particle clustering or agglomeration, especially with Nano-particles.
- Porosity and poor bonding if stirring is not done correctly.
- Uneven dispersion of reinforcements may result in areas with weak spots.
These issues can often be overcome with optimized process parameters, such as stirring speed, duration, and the use of wetting agents like magnesium.
Stir casting using aluminium offers a straightforward approach to producing composite materials. It strikes a balance between simplicity, scalability, and performance, making it a valuable process for industries and research alike. Whether you're a student, a researcher, or a manufacturing professional, understanding the basics of stir casting opens the door to innovation in materials engineering.