In manufacturing, both accuracy and streamlined operations are key to success. One machine that plays a vital role in creating high-quality moulded parts is the compression moulding press. Whether you’re in the automotive, aerospace, electrical, or consumer goods industry, understanding how a compression moulding machine works can help you make better production decisions—especially when working with materials like rubber and plastic.
In this blog, we’ll explore what a compression moulding press is, how it works, and the different types of compression moulding machines.
What Is a Compression Moulding Press?
A compression moulding press is a type of machine used to shape materials—usually thermosetting plastics or rubber—by applying heat and pressure in a mould cavity. Unlike injection moulding, which injects material into a mould, compression moulding involves placing the raw material directly into the mould, then compressing it under high pressure.
This process is perfect for producing large, durable parts with complex shapes. It is commonly used to manufacture components such as electrical insulators, automotive gaskets, appliance housings, and sporting goods.
How Does a Compression Moulding Machine Work?
The working principle of a compression moulding machine involves several critical steps:
- Material Preparation
A pre-defined amount of raw material, in the form of pellets, sheets, or preforms, is placed directly into the open, heated mould cavity. - Mould Closing
The top half of the mould is closed by the press. Hydraulic or mechanical force is applied to compress the material within the mould. - Heating and Forming
Heat is applied (usually between 250°F and 400°F), causing the material to flow and fill the mould cavity. The material begins to solidify or set when subjected to continuous pressure. - Cooling and Ejection
Once the material is fully cured, the mould is opened and the finished part is removed.
This straightforward yet powerful process makes compression moulding ideal for high-strength, high-volume production.

Types of Compression Moulding Machines
By Drive Type:
Hydraulic Compression Moulding Machine:
Hydraulic machines are the traditional and most commonly used type in compression moulding. These systems rely on hydraulic fluid pressure to apply the force needed to shape and cure the material in the mould.
Key Features:
- High clamping force (typically ranging from 20 to over 2000 tons)
- Excellent for processing large or thick parts
- Well-suited for thermoset materials and composite applications
Electric Compression Moulding Machine:
Electric compression moulding machines utilize servo motors in place of hydraulic systems to apply force. This design enables greater precision and quicker cycle times, making them ideal for high-speed manufacturing.
Key Features:
- Servo-driven mechanisms for movement and pressure application
- Requires lower energy input than standard hydraulic systems
- Quieter and cleaner operation (no hydraulic oil)
Hybrid Compression Moulding Machines:
By merging hydraulic and electric features, hybrid machines offer versatile operation. Typically, they use electric drives for functions requiring speed and precision while retaining hydraulic systems for high-force operations.
Key Features:
- Blend of electric and hydraulic systems for optimized performance
- Energy-efficient without sacrificing clamping force
- Improved process control and flexibility
By Application:
Rubber Compression Moulding Machine:
Specifically designed to work with natural and synthetic rubbers, these machines are widely used in industries where flexibility, durability, and temperature resistance are key—such as automotive seals, vibration dampers, and medical-grade components.
Key Features:
- High-temperature heating plates
- Multiple cavity moulds
- Vacuum options for better finish and fewer air bubbles
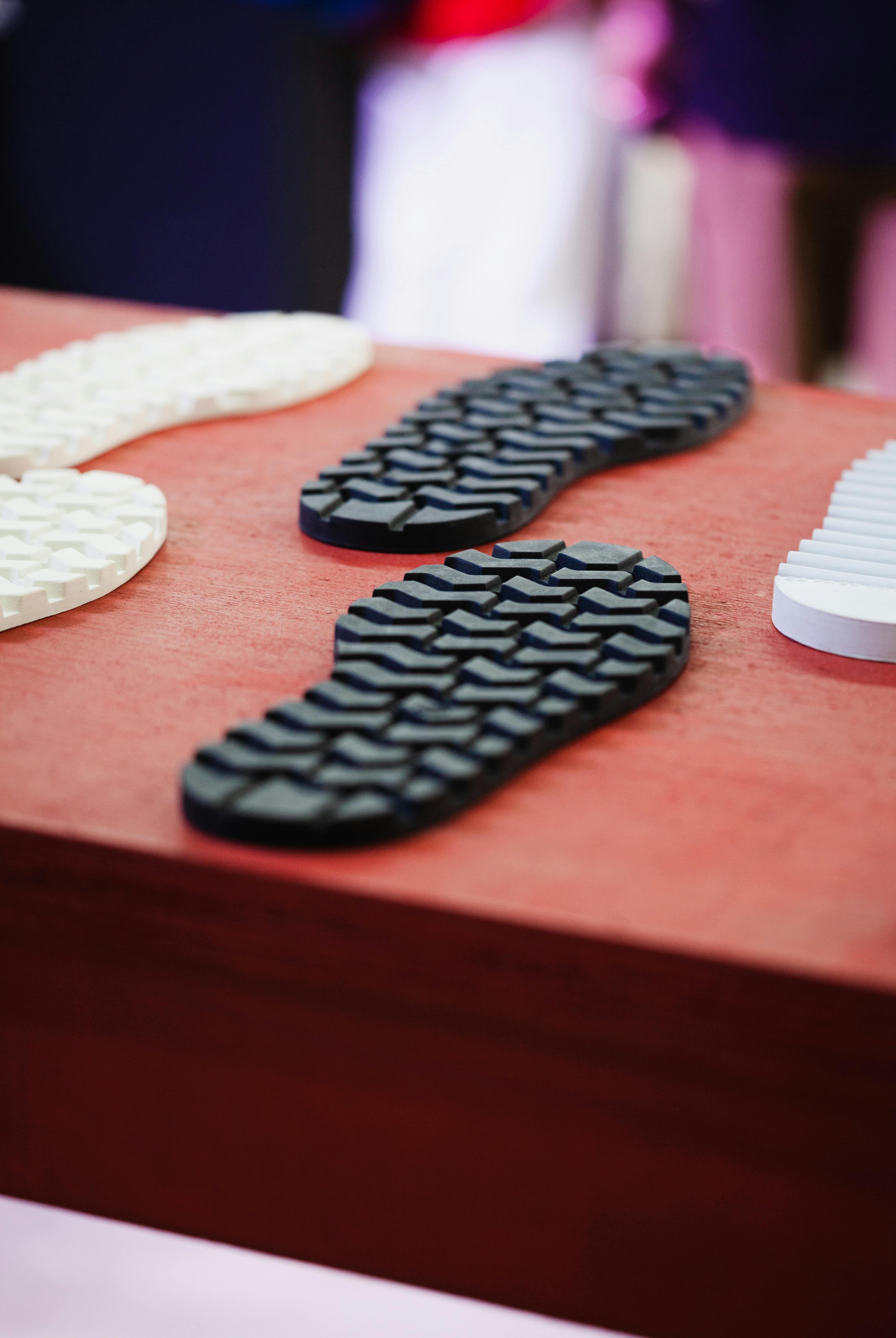
Plastic Compression Moulding Machine:
Designed for thermoset plastics such as phenolic, melamine, and polyester. These are frequently used to produce items such as electrical components, household utensils, and protective industrial casings.
Key Features:
- Consistent pressure control
- Precision mould alignment
- Fast cycle times for mass production
Advantages of Using a Compression Moulding Press
- Suitable for Large-Scale Parts: Offers a cost advantage in tooling over injection moulding.
- Excellent Material Utilization: Minimal waste, especially for rubber and fibre-reinforced plastics.
- Durable End Products: Provides excellent structural integrity and dimensional stability.
- Versatility: Suitable for a variety of industrial applications, as mentioned above.
A compression moulding machine is a foundational tool in modern manufacturing, offering a blend of efficiency, strength, and flexibility. Whether you're using a rubber compression moulding machine for high-flexibility parts or a plastic compression moulding machine for rigid components, understanding how a compression moulding press works helps you maximize productivity and product quality.
If you’re considering investing in or upgrading your moulding equipment, be sure to assess your material needs, part complexity, and production volume. The proper press plays a key role in achieving quality results.