In the realm of material science and advanced manufacturing, the Chemical Vapour Deposition (CVD) furnace has emerged as a cornerstone technology. From semiconductors to industrial coatings, the precision and efficiency of CVD furnaces have revolutionized multiple industries. Let’s delve into the fascinating world of Chemical Vapour Deposition systems, their applications, and why they are indispensable in modern laboratories and production facilities.
A Chemical Vapour Deposition furnace is a high-temperature system designed to deposit thin films or coatings on a substrate. This is achieved by introducing gaseous precursors into the furnace chamber, where they chemically react and form a solid material on the substrate surface. The process is highly controlled, enabling the creation of coatings with exceptional purity, uniformity, and precision.
Applications of CVD Furnaces
- Semiconductor Industry:
Deposition of thin films for transistors, diodes, and integrated circuits
Epitaxial growth for silicon wafers
- Protective Coatings:
Hard coatings for cutting tools and turbine blades
Wear-resistant layers for biomedical implants
- Optical Coatings:
Applications in lenses, mirrors, and optical fibres
- Advanced Materials Development:
Synthesis of carbon nanotubes, graphene, and diamond films
Refractory material deposition (e.g., tungsten, molybdenum)
- Energy Sector:
Fabrication of thin-film solar cells
Coatings for fuel cell components
- Laboratory Research:
Experimental synthesis for nanotechnology, catalysis, and material surface modifications
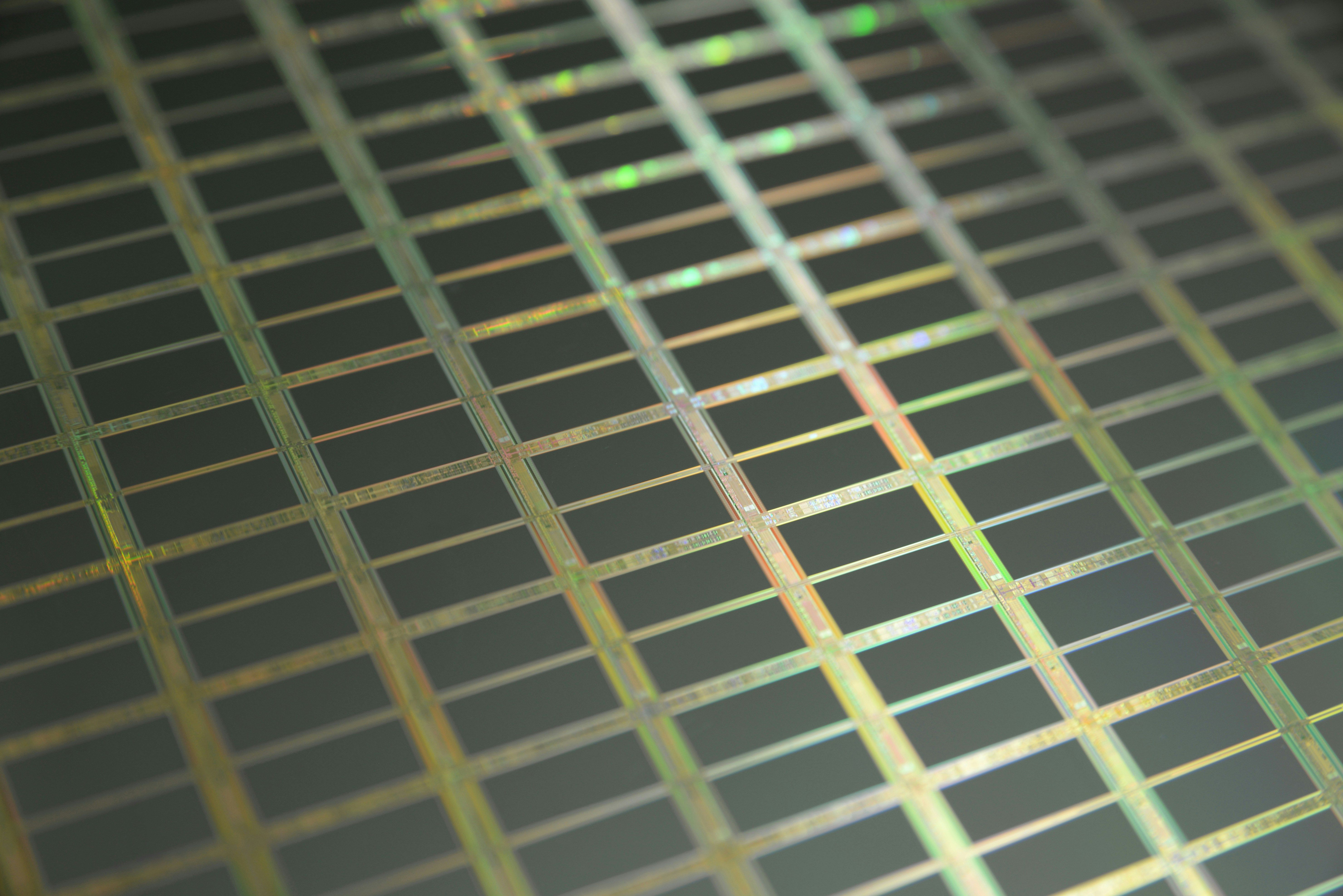
How Does a CVD Furnace Work?
- Preparation:
Substrates are cleaned to ensure adhesion of the deposited material
- Setup:
Substrates are placed inside the furnace chamber under controlled atmospheric or vacuum conditions
- Precursor Introduction:
Gaseous precursors are introduced into the chamber, often mixed with a carrier gas like argon or hydrogen
- Reaction and Deposition:
At elevated temperatures, precursors react near the substrate, forming a solid material that deposits as a thin film or coating
- Exhaust Removal:
By-products are evacuated through an efficient exhaust system
- Post-Processing:
The coated substrate may undergo annealing, etching, or other processes to refine the material
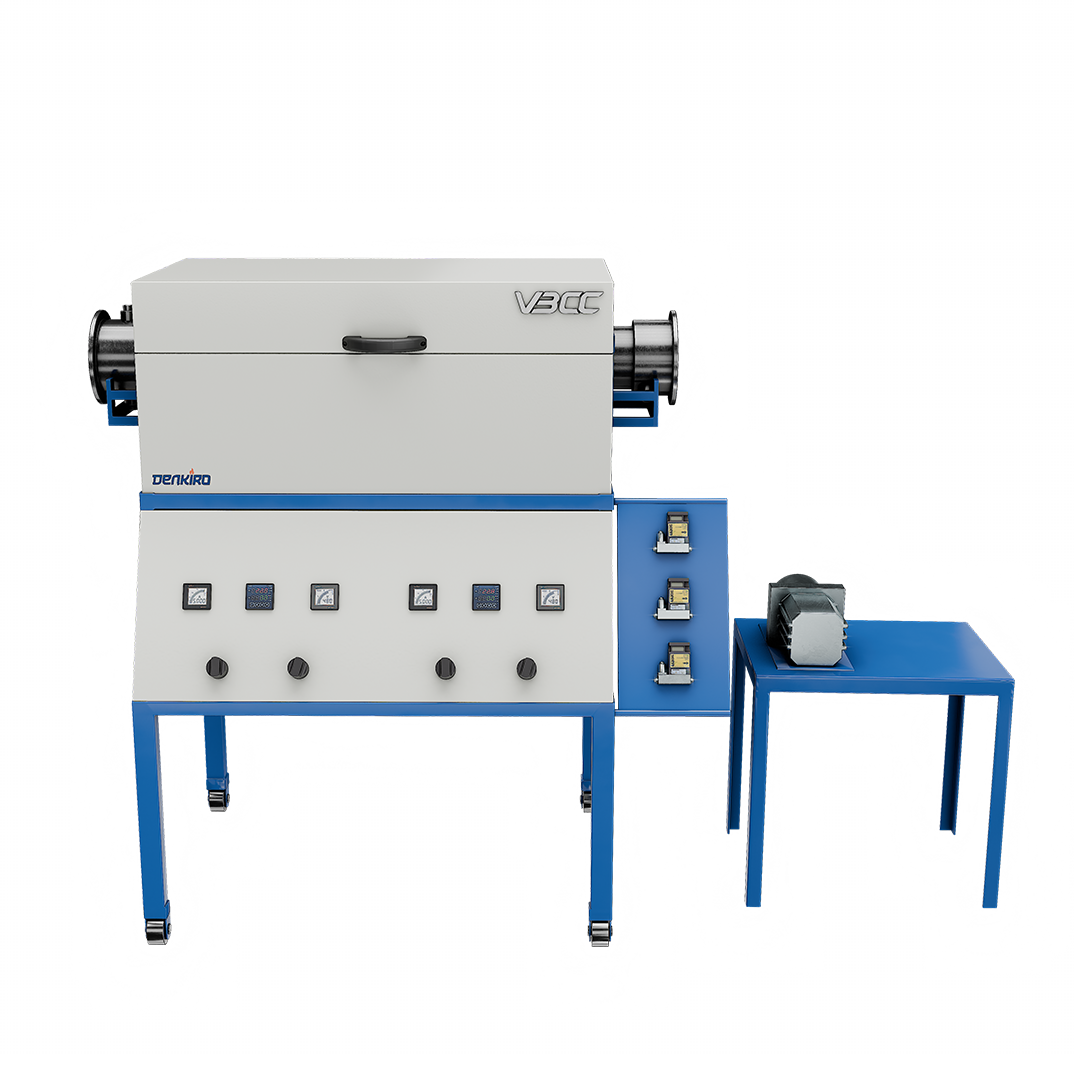
Benefits of Using a CVD Furnace
High Purity: Produces coatings with minimal defects and controlled composition
Uniform Coatings: Ensures even deposition across complex geometries
Material Versatility: Supports metals, ceramics, and polymers
Strong Adhesion: Deposited films exhibit excellent bonding with substrates
Enhanced Properties: Improves hardness, thermal stability, corrosion resistance, and optical characteristics
Scalability: Suitable for both small-scale research and industrial-scale production
How to Choose a CVD Furnace
Key Factors to Consider:
- Temperature Range:
Ensure the furnace meets the required processing temperatures. Laboratory setups typically require up to 1200°C, while industrial systems may demand higher ranges
- Chamber Size:
Choose a size that accommodates your largest substrate or batch volume
- Atmosphere Control:
Check for furnaces efficient in maintaining inert, vacuum, or reactive gas atmosphere
- Material Compatibility:
Ensure furnace materials (e.g., quartz or graphite) are suitable for the chemical reactions involved
- Automation:
Industrial furnaces benefit from automated controls for precision and efficiency
- Safety Features:
Opt for systems with robust exhaust mechanisms, gas flow monitoring, and over-temperature protection
- Maintenance and Support:
Prioritize models with accessible components and reliable technical support
For Laboratory Use:
When choosing a laboratory CVD furnace, consider options with compact designs and modular setups, as these provide enhanced flexibility for a wide range of experiments. Such systems allow for easy customization to meet specific research needs. Additionally, cost-effective solutions are crucial for budget-conscious labs, ensuring that you can achieve high-quality results without overspending. Flexibility, cost-effectiveness, and adaptability are key factors to look for when selecting the right furnace for laboratory applications.
For Industrial Applications:
For industrial applications, it’s important to focus on models that offer high throughput and scalability to handle large-scale production requirements. Look for systems with advanced process controls and automation to ensure precision and consistency across operations. Additionally, prioritize durability and efficiency to guarantee long-term performance and minimize maintenance costs, especially in demanding industrial settings. These factors are key to selecting a reliable and effective industrial CVD furnace.
Chemical Vapour Deposition (CVD) furnaces are indispensable tools in advancing material science and manufacturing processes. Their ability to produce high-quality thin films and coatings with precision, uniformity, and enhanced properties makes them vital in industries ranging from semiconductors to energy. Whether for laboratory research or large-scale industrial applications, choosing the right CVD furnace involves careful consideration of factors like temperature range, material compatibility, and automation. With their scalability, versatility, and performance, CVD furnaces continue to drive innovation across various sectors, shaping the future of advanced materials and manufacturing technologies.