Heat treatment is a crucial manufacturing process that enhances the properties of metals and ceramics, making them more suitable for industrial applications. Whether you’re new to the field or looking to deepen your knowledge, this guide covers the fundamentals of industrial heat treatment.
What is Heat Treatment?
Heat treatment involves controlled heating and cooling of metals and ceramics to modify their physical and mechanical properties without altering their shape. This process enhances hardness, strength, ductility, and wear resistance, depending on the application.
Key Stages of Heat Treatment
Industrial heat treatment typically consists of three main stages:
- Heating: The material is gradually heated to a specific temperature based on the desired property changes
- Soaking: The material is held at the target temperature for a set time to ensure uniform transformation
- Cooling: The material is cooled at a controlled rate—either rapidly (quenching) or slowly (annealing)—to achieve the desired characteristics
Common Heat Treatment Processes
Different heat treatment techniques are used depending on material type and application requirements.
1. Annealing
Annealing enhances metal workability by reducing internal stresses and improving machinability. The process involves heating the metal to a set temperature, maintaining it for a specific duration, and then gradually cooling it, usually in a furnace. This results in increased ductility and reduced brittleness, making materials like steel, copper, and aluminium easier to shape and process.
Types of Annealing
- Full Annealing – Heating above the material’s recrystallization temperature and slow cooling to achieve maximum softness
- Process Annealing – Performed below the recrystallization temperature to remove work hardening effects
- Stress Relief Annealing – Reduces residual stresses without significantly altering material properties
- Spheroidizing Annealing – Improves machinability of high-carbon steels by forming spherical carbides
- Isothermal Annealing – Rapid cooling to an intermediate temperature, followed by soaking for uniform grain refinement
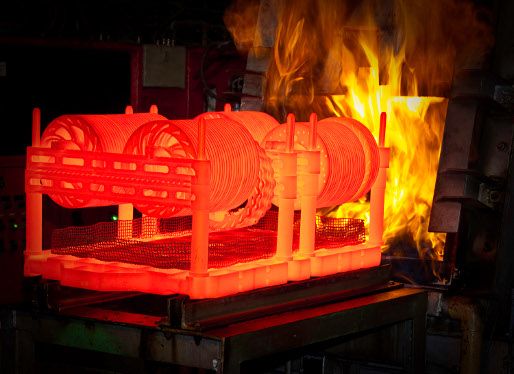
2. Hardening
Hardening strengthens metals by heating and rapidly cooling them through quenching. While it increases wear resistance, it can make the metal brittle, often requiring tempering for improved toughness. This process is widely used in tools, gears, and machine parts to enhance durability.
Types of Hardening
- Quench Hardening – Heating above the transformation temperature and rapidly cooling (quenching) to form a hard-martensitic structure
- Case Hardening (Surface Hardening) – Hardens only the surface while maintaining a tough core; includes carburizing, nitriding, and carbonitriding
- Precipitation Hardening (Age Hardening) – Strengthens alloys like aluminium and stainless steel by forming fine precipitates in the metal matrix
3. Tempering
Tempering reduces brittleness in hardened metals while maintaining strength. The metal is reheated to a moderate temperature and then cooled at a controlled rate. This improves toughness, making the material more resistant to cracking and impact. Tempering is commonly applied to tools, springs, and automotive parts.
Tempering Temperature Effects
- Low-Temperature Tempering (150–300°C) – Retains high hardness, improves wear resistance
- Medium-Temperature Tempering (300–500°C) – Enhances toughness and strength
- High-Temperature Tempering (500–700°C) – Maximizes ductility and reduces hardness
4. Normalizing
Normalizing refines the grain structure of metals, enhancing strength and toughness. The metal is heated above its critical temperature, held there, and then air-cooled. This process improves uniformity, reduces internal stresses, and enhances machinability. It is widely used in forgings, castings, and structural components.
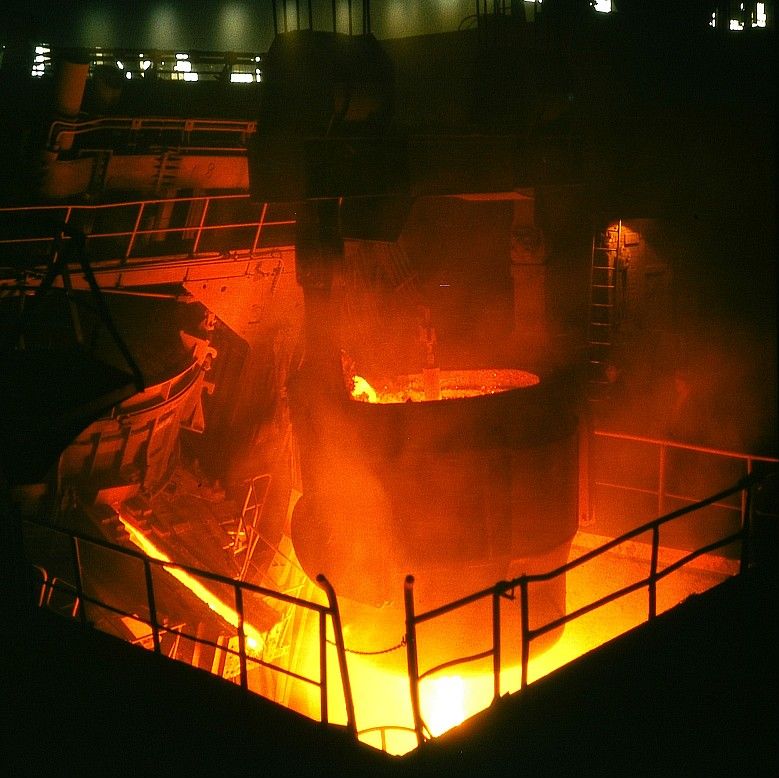
5. Case Hardening (Surface Hardening)
Case hardening increases surface hardness while keeping the core softer. It involves adding carbon or nitrogen to the surface, followed by quenching. This process enhances wear resistance, making it ideal for parts exposed to high surface stress, such as gears and bearings.
Types of Case Hardening
- Carburizing – Adds carbon to the surface of low-carbon steel, followed by quenching to form a hard case
- Nitriding – Introduces nitrogen into the surface layer, creating a hard, wear-resistant case without quenching
- Carbonitriding – A combination of carburizing and nitriding, using both carbon and nitrogen for deeper hardening
- Induction Hardening – Uses electromagnetic induction to heat specific areas, followed by rapid cooling (quenching)
- Flame Hardening – Direct flame application heats specific areas, followed by quenching to harden only the surface
- Laser Hardening – Uses a focused laser beam to precisely heat and harden surface regions
6. Quenching
Quenching rapidly cools heated metal by immersing it in water, oil, or air. This alters the metal’s microstructure, increasing strength and wear resistance. It is commonly used in manufacturing tools, gears, and components requiring high durability.
Types of Quenching Media
- Water Quenching – Fastest cooling, produces maximum hardness but increases the risk of cracking
- Brine Quenching – Saltwater quenching for even faster cooling than water
- Oil Quenching – Moderate cooling rate, reduces warping and cracking
- Air Quenching – Used for air-hardenable steels (e.g., A2, D2 tool steels) that harden at slower cooling rates
- Polymer Quenching – Water-based solutions with controlled cooling rates for customized hardening
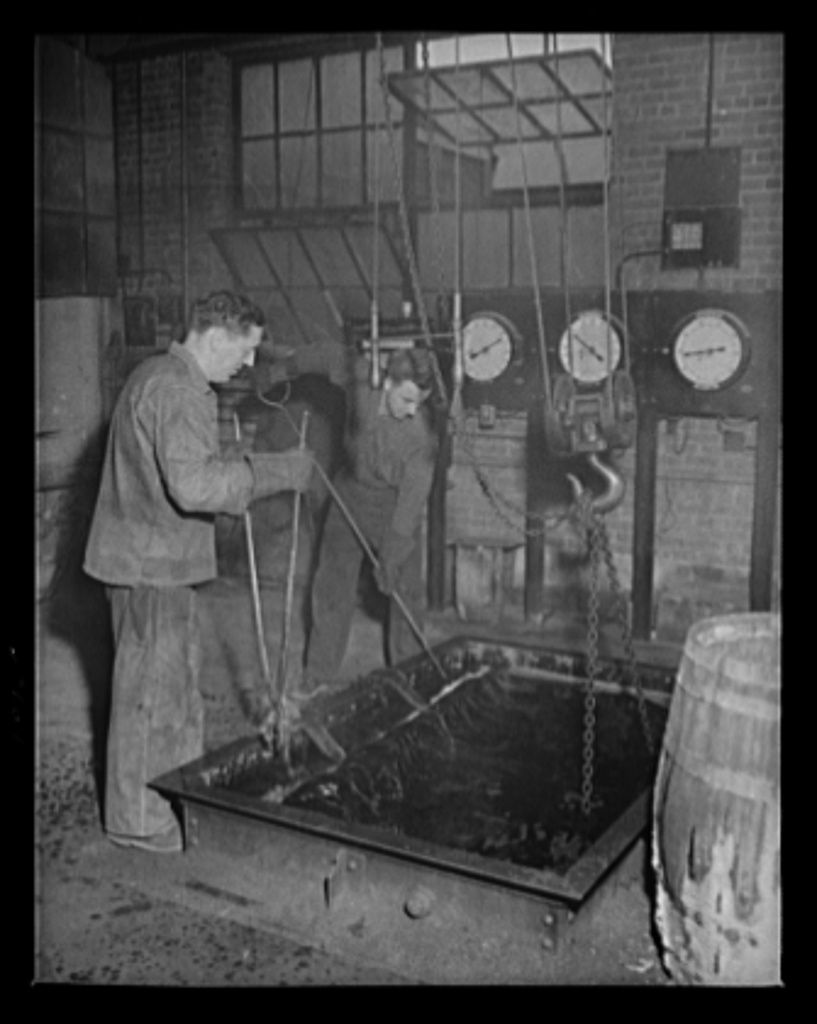
7. Stress Relieving
Stress relieving reduces internal stresses caused by welding, casting, or machining. The metal is heated to a specific temperature (below its critical point) and then slowly cooled. This prevents distortion and cracking while improving stability and strength.
Stress Relieving Temperatures
- Carbon Steels & Alloy Steels: 500–700°C
- Stainless Steels: 450–600°C (to avoid sensitization)
- Aluminium Alloys: 250–350°C
- Copper & Brass: 200–300°C
8. Austempering and Martempering
Both processes improve steel's hardness and toughness.
- Austempering – Steel is quenched in a salt bath and held until bainite forms, enhancing toughness
- Martempering – Steel is cooled in oil or salt at a controlled rate, preventing internal stresses before forming martensite
Applications of Heat Treatment in Industries
Heat treatment is vital in various industries, including:
- Automotive: Enhances durability of engine components, gears, and shafts.
- Aerospace: Improves strength and fatigue resistance of aircraft parts.
- Manufacturing: Ensures reliability of tools, dies, and machine components.
- Electronics: Enhances thermal and mechanical stability in semiconductors.
Industrial heat treatment transforms material properties to meet specific engineering needs. Understanding its fundamentals helps manufacturers select the right process to optimize performance and longevity. With advancements in furnace technology, companies continue to enhance precision and efficiency in heat treatment applications.