Roller Hearth Furnaces (RHF) are widely used in industrial heat treatment processes due to their ability to provide continuous heating with precise temperature control. They utilize a conveyor system with rotating rollers to move materials through the heating chamber, making them ideal for high-volume production. Different types of roller hearth furnaces cater to various industrial needs, each offering unique advantages based on temperature requirements, processing speed, and atmosphere control. In this blog, we explore the primary types of RHFs and their applications across industries.
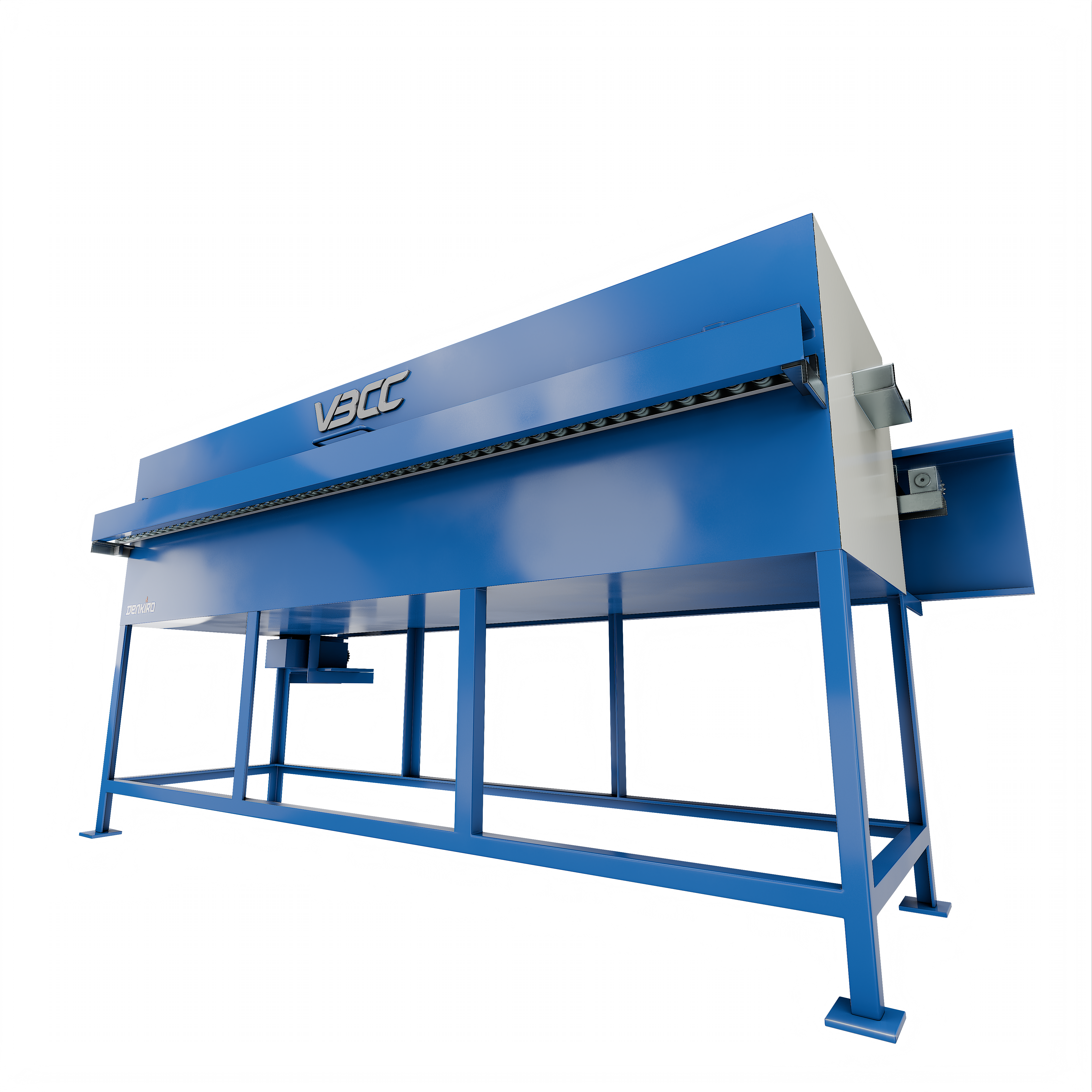
1. Gas-Fired Roller Hearth Furnace
Overview:
Gas-fired roller hearth furnaces use natural gas or other fuel sources for heating, making them energy-efficient for high-temperature applications. They are designed with burners that provide uniform heating throughout the chamber.
Applications:
- Heat treatment of steel and alloys: Used for processes like annealing, normalizing, and hardening to improve mechanical properties.
- Automotive and aerospace component manufacturing: Essential for producing high-strength and wear-resistant parts, including gears, shafts, and engine components.
- Metal forging and rolling operations: Supports preheating and post-processing of metal parts to enhance their durability and performance.
- Large-scale industrial heating: Ideal for continuous production lines where rapid heating and cooling cycles are necessary.
2. Electric Roller Hearth Furnace
Overview:
Electric RHFs utilize electric heating elements, offering precise temperature control and reduced emissions compared to gas-fired alternatives. They are preferred in industries where clean processing environments are essential.
Applications:
- High-purity material processing: Used in semiconductor and electronics manufacturing where contamination must be minimized.
- Precision heat treatment: Required for critical aerospace and medical components that demand exact thermal conditions.
- Heat treatment of aluminium and non-ferrous metals: Ensures controlled annealing and hardening processes for lightweight metal applications.
- Eco-friendly industrial operations: Helps industries meet stringent environmental regulations with lower emissions and energy-efficient designs.
3. Vacuum Roller Hearth Furnace
Overview:
Vacuum RHFs operate under low-pressure conditions, preventing oxidation and contamination of sensitive materials. They provide a controlled environment for specialized processes requiring inert or reducing atmospheres.
Applications:
- Heat treatment of titanium and superalloys: Essential for aerospace, medical, and high-performance applications requiring superior strength and corrosion resistance.
- Sintering of powdered metals and ceramics: Used in producing high-density components with enhanced mechanical properties.
- Brazing and diffusion bonding: Commonly applied in the medical and aerospace industries for joining dissimilar materials without compromising structural integrity.
- Thermal processing of sensitive materials: Supports research and development in material science where oxidation-sensitive elements are involved.
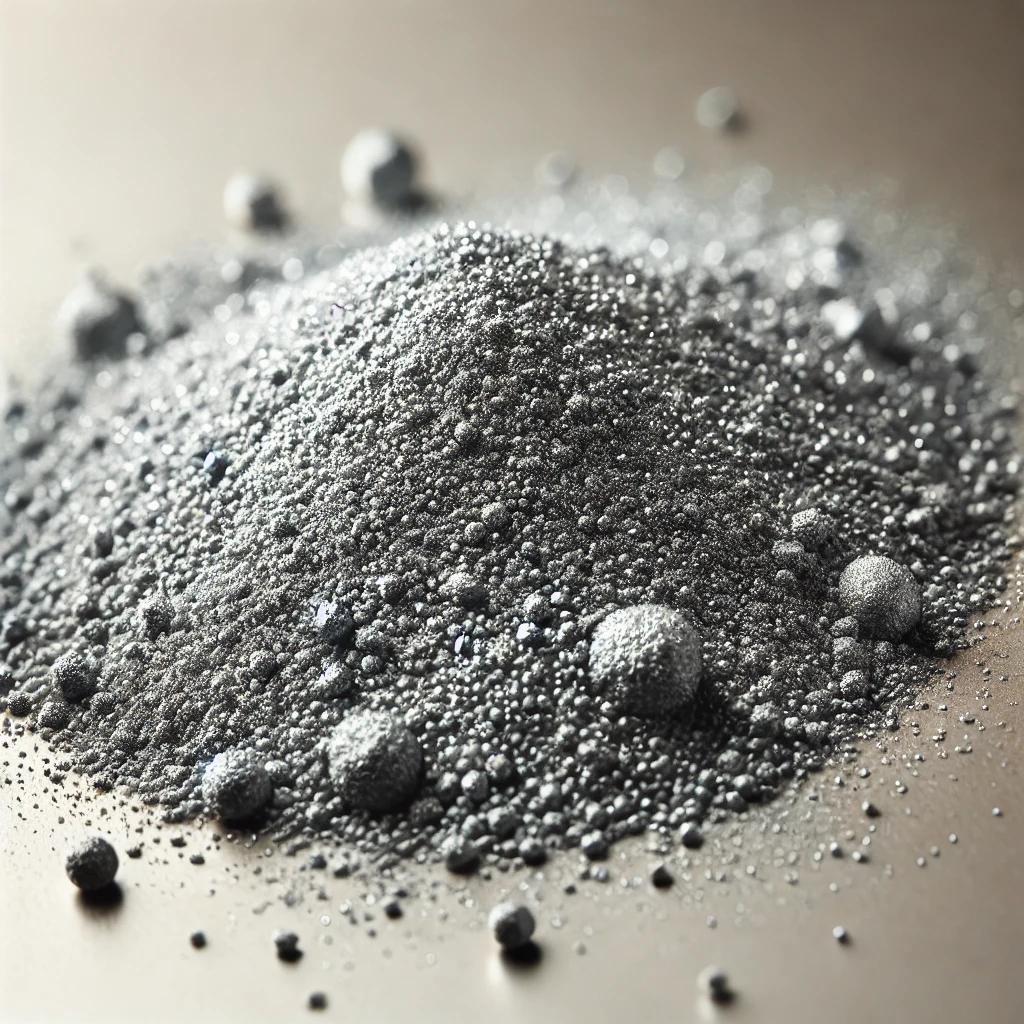
4. Atmosphere-Controlled Roller Hearth Furnace
Overview:
These furnaces use a controlled gas environment, such as nitrogen, hydrogen, or argon, to achieve specific metallurgical properties. They help in preventing scale formation and oxidation during heat treatment.
Applications:
- Carburizing and nitriding of gears and bearings: Improves surface hardness and wear resistance in automotive and industrial machinery parts.
- Annealing of stainless steel and specialty alloys: Enhances ductility and machinability in various metal components.
- Production of electronic and precision components: Used for controlled oxidation and surface conditioning in microelectronics and precision engineering.
- Gas-assisted sintering processes: Facilitates better control over material composition in high-performance applications.
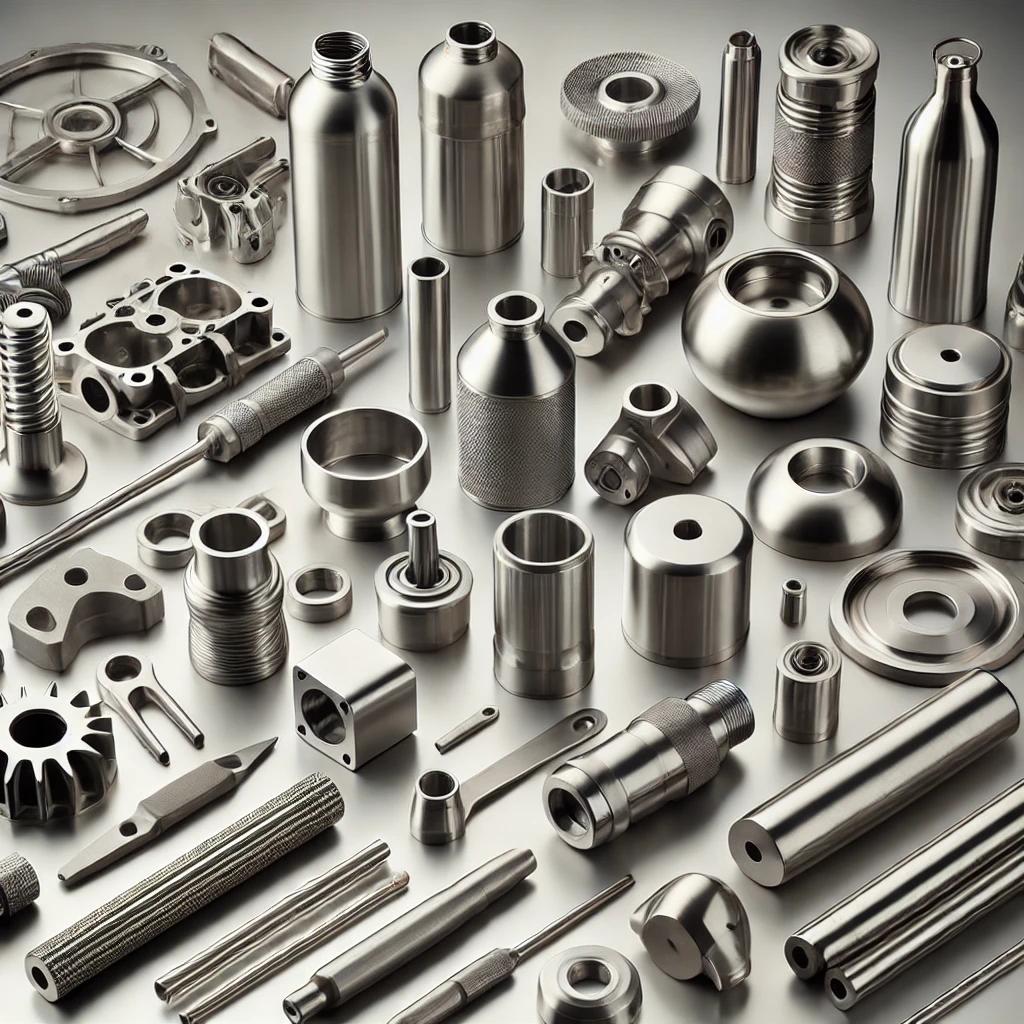
5. High-Temperature Roller Hearth Furnace
Overview:
Designed for extreme temperature applications (up to 1800°C), high-temperature RHFs are used for materials that require intense thermal processing. These furnaces often incorporate advanced refractory materials and insulation to maintain efficiency.
Applications:
- Ceramic sintering and refractory material processing: Used to manufacture durable and heat-resistant components for industrial and consumer applications.
- Graphite and carbon processing: Essential for producing electrodes, crucibles, and high-purity carbon-based materials.
- Heat treatment of advanced composites: Supports the development of high-performance materials for aerospace, defence, and energy applications.
- High-temperature research and prototyping: Utilized in R&D facilities for developing new materials with extreme thermal resistance.
Choosing the right type of Roller Hearth Furnace depends on the material being processed, the required temperature range, and the desired atmospheric conditions. Whether for steel annealing, precision electronics manufacturing, or high-temperature ceramics, RHFs offer versatility and efficiency for modern industrial applications. As industries continue to demand higher efficiency and sustainability, advancements in RHF technology, such as hybrid heating and energy recovery systems, will further enhance their role in manufacturing processes.