Ceramics are essential in a wide range of advanced technologies—from electronics and aerospace to biomedical devices and energy systems. At the core of ceramic fabrication lies a critical thermal process: sintering and firing. These processes are what transform raw powders or moulded “green bodies” into fully dense, durable ceramic components. And the tool that makes this transformation possible? The laboratory furnaces.
In this article, we’ll break down the roles furnaces play in ceramic sintering and firing, key technical requirements, and common applications across industries.
What Is Ceramic Sintering?
Sintering is a high-temperature process that densifies ceramic powders into solid forms through solid-state diffusion. It takes place below the melting point of the material and is driven by the reduction of surface energy between particles.
Depending on the material, sintering typically occurs in the range of:
- 1200–1600°C for Alumina (Al₂O₃)
- 1300–1500°C for Yttria-Stabilized Zirconia (YSZ)
- 1700–1900°C for Ultra-High-Temperature Ceramics like ZrB₂ or SiC
To support these conditions, furnaces must offer precise temperature control, uniform heating, and controlled atmosphere capabilities.
Firing vs. Sintering: What’s the Difference?
Though often used interchangeably, the terms have specific meanings in materials science:
- Firing is the general process of heating ceramics, which may include drying, binder burnout, sintering, and even glazing.
- Sintering refers specifically to the densification stage, where the structure consolidates into a solid, mechanically strong material.
In technical ceramics, sintering is the most critical phase, especially for applications requiring tight tolerances, high strength, and thermal stability.
The Role of Furnaces in the Ceramic Process
Laboratory furnaces are essential to every stage of ceramic processing—from initial debinding to final densification. Their design and performance directly impact material quality, repeatability, and yield. Let’s delve deeper into the key functions that furnaces perform in this process:
1. Temperature Uniformity
Achieving consistent, uniform heat distribution across the furnace chamber is vital during ceramic sintering. Uneven heating can lead to localized densification, resulting in warping, internal stress, or incomplete bonding between particles. These issues can compromise mechanical integrity, dielectric properties, and dimensional stability—especially in applications requiring tight tolerances. High-quality laboratory furnaces are equipped with multi-zone heating systems and high thermal mass insulation to maintain uniform temperatures, typically within ±3–5°C across the hot zone. This level of control ensures homogeneous grain growth and sintering kinetics, which are especially important when processing multilayer ceramic devices, advanced composites, or 3D-printed components.
2. Controlled Atmospheres
Many advanced ceramics are sensitive to the surrounding atmosphere during firing. While some materials, such as alumina or silica, sinter well in ambient air, others require inert or reducing environments to preserve chemical stability and functional performance. For example, silicon carbide (SiC) and boron carbide (B₄C) are prone to oxidation at elevated temperatures and must be sintered in argon or nitrogen. Similarly, electronic ceramics like barium titanate (BaTiO₃) can experience changes in stoichiometry and dielectric behaviour when fired in air, necessitating a low oxygen partial pressure environment. Furnaces designed for ceramic R&D and production may include sealed chambers, vacuum pumps, or gas inlet systems that enable tight control over gas composition and flow rates. This functionality allows researchers to tune material properties by manipulating redox conditions and phase equilibria during the firing cycle.
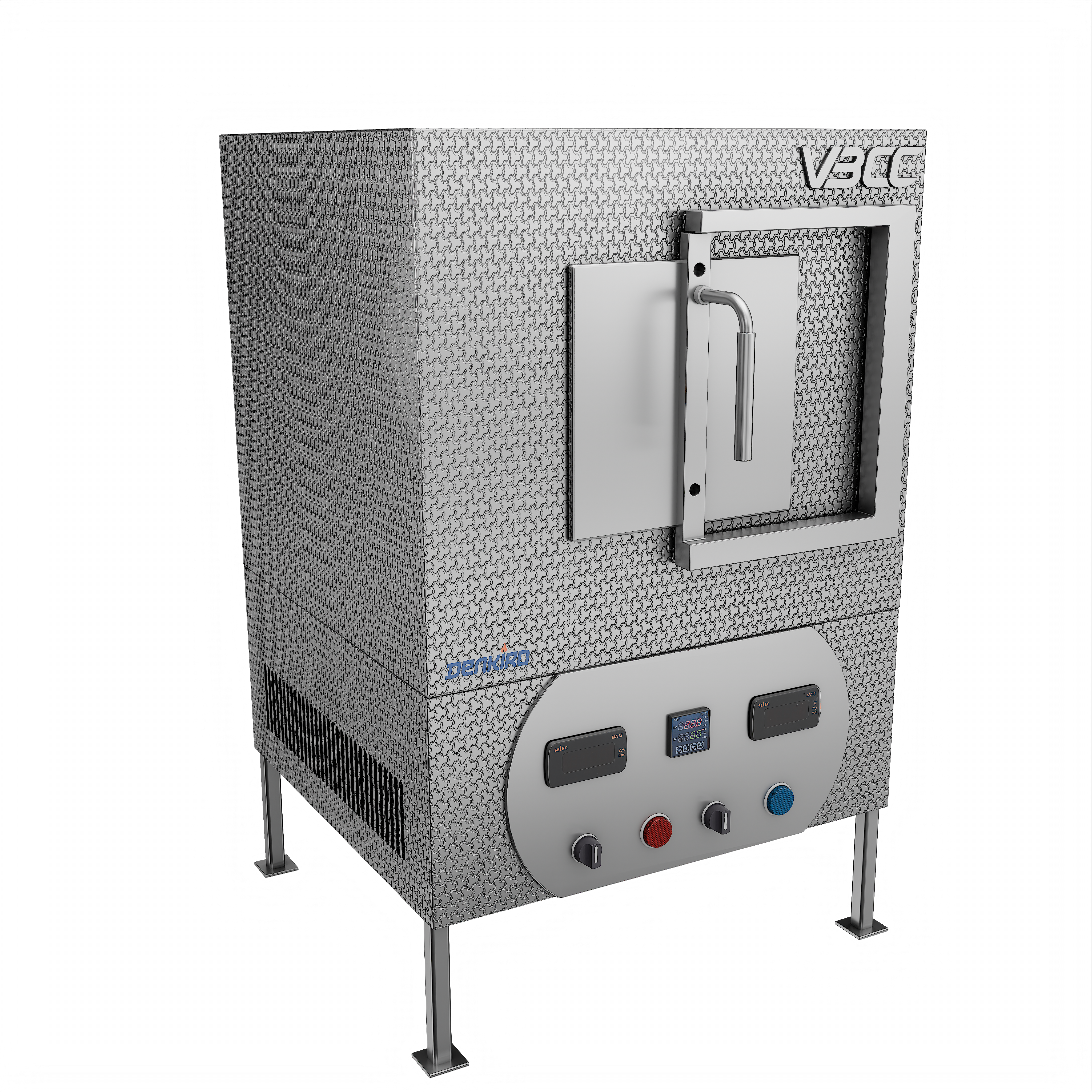
3. Programmable Thermal Profiles
Sintering is a complex thermal operation that requires more than just raising the material to a high temperature. The process depends on carefully designed heating profiles that include controlled ramp rates, specific hold durations (soaks), and gradual cooling sequences. For example, during the initial debinding phase—typically occurring between 200°C and 600°C—temperature must be increased slowly to avoid thermal shock or deformation as organic binders decompose and volatilize. If heating is too rapid at this stage, it can lead to bloating or the formation of internal cracks. After successful debinding, the material is gradually brought to its sintering temperature, often at a rate of 3–10°C per minute, depending on its thermal properties and geometry. A sustained soak at peak temperature, lasting between 1 to 6 hours, enables grain boundary diffusion and densification. Controlled cooling is equally critical, helping to prevent thermal stresses and defects such as microcracks. Advanced laboratory furnaces equipped with programmable PID controllers are essential for executing these thermal cycles with precision and consistency, making them indispensable in both research and production environments.
Industrial & Research Applications
Laboratory furnaces support a wide range of ceramic applications. YSZ components for solid oxide fuel cells are sintered at 1350–1500°C in air or oxygen. Alumina and barium titanate, used in electronics, require 1200–1450°C with controlled atmospheres. Hydroxyapatite for biomedical implants is typically fired at 1000–1200°C in air. Ultra-high temperature ceramics like ZrB₂ and SiC, used in aerospace, demand 1800–2000°C under vacuum or inert gas. In additive manufacturing, materials such as alumina and silica are sintered between 1200–1600°C, depending on the formulation.
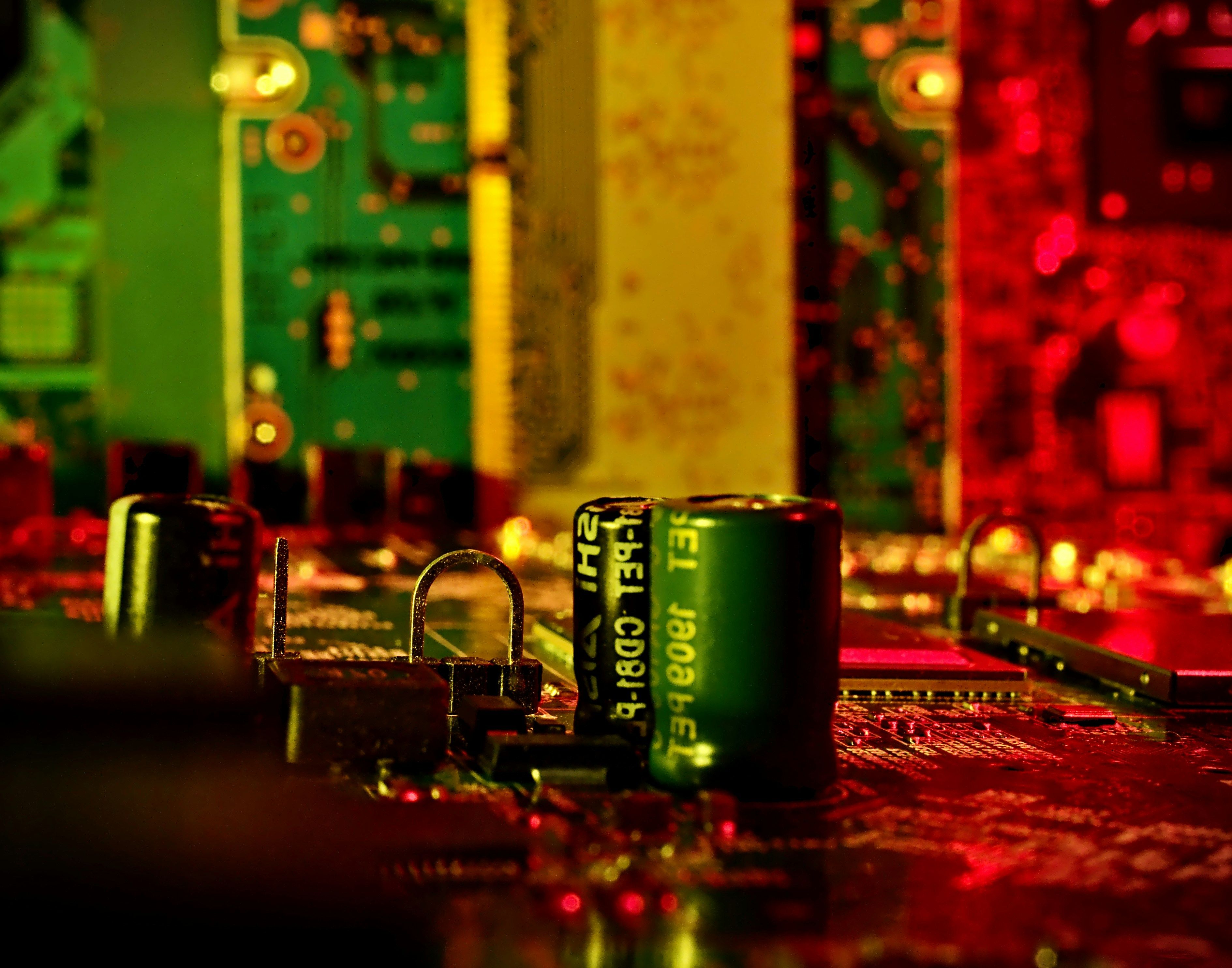
From traditional kiln-based ceramics to advanced structural and functional materials, furnaces are the backbone of the ceramic sintering and firing process. With the increasing demand for high-performance materials, the importance of precision thermal processing has never been greater.
Whether you’re developing solid oxide fuel cells, bio ceramics, or ultra-high temperature coatings, selecting the right laboratory furnace ensures process repeatability, high part quality, and reliable material performance.