The aerospace industry is synonymous with innovation, precision, and advanced materials. Whether crafting the lightweight structures of commercial airliners or the heat-resistant alloys of space shuttles, achieving these remarkable results relies on state-of-the-art industrial furnaces and heat-treating equipment. These high-temperature instruments play a pivotal role in aerospace manufacturing, enabling the development of high-performance materials and ensuring components meet stringent standards.
The Role of Industrial Furnaces in Aerospace Manufacturing
Aerospace materials must endure extreme conditions, such as high temperatures, pressure, and corrosive environments. To meet these demands, advanced processes like heat treatment, sintering, brazing, and thermal coating are vital. Industrial furnaces and furnace systemsare at the heart of these operations, offering precise temperature control, uniform heating, and customizable atmospheres to enhance material properties.
Key Applications of Heat-Treating Equipment in Aerospace
Heat Treatment of Alloys: Industrial furnaces optimize the strength, durability, and temperature resistance of aerospace alloys like turbine blades and engine parts through annealing, quenching, and tempering.
Sintering of Ceramics: High-temperature instruments densify and strengthen ceramics used in thermal insulation and structural components for aerospace.
Brazing and Joining: Vacuum furnaces enable defect-free assembly of critical aerospace parts like honeycomb panels and fuel lines by providing an oxygen-free environment.
Thermal Coatings: Industrial furnaces apply protective coatings to turbine blades and engine components, enhancing resistance to heat, corrosion, and wear.
Types of Industrial Furnaces Used in Aerospace
Vacuum Furnaces
Essential for processes requiring an oxygen-free environment, vacuum furnaces are used for heat treating, brazing, and sintering. These systems ensure oxidation-free, high-quality finishes for critical aerospace parts, such as turbine blades, fuel nozzles, and landing gear.
Roller Hearth Furnaces
Ideal for high-volume production, roller hearth furnaces are commonly used to process turbine blades, mounting brackets, and fasteners. These furnaces ensure precise, consistent heating in controlled atmospheres, essential for high-quality aerospace components.
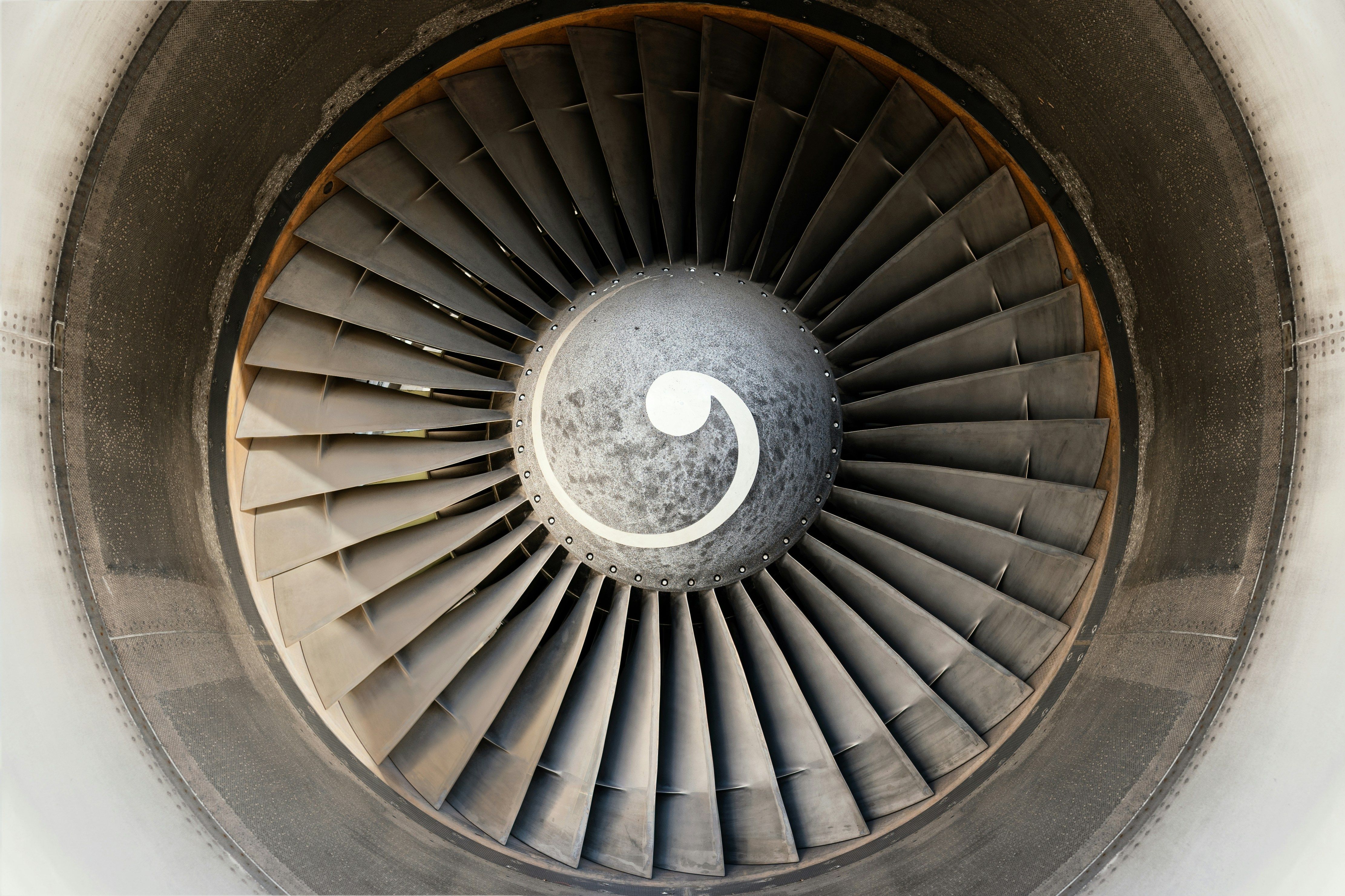
Microwave Furnaces
Advanced microwave industrial furnaces enable rapid and uniform heating for materials like ceramic matrix composites and high-performance ceramics. These are critical in manufacturing thermal protection tiles, heat shields, and engine components, offering reduced energy consumption and processing times.
Atmosphere-Controlled Furnaces
Atmosphere-controlled furnaces allow for processes like carburizing and annealing of parts such as turbine blades, landing gear, and engine components. These systems use controlled gases like nitrogen, argon, or hydrogen to enhance strength, hardness, and durability.
Box Furnaces
Widely used for heat treatments such as annealing and tempering, box furnaces process large aerospace components like engine casings, wing spars, and landing gear struts. These systems deliver uniform heating to ensure optimal material properties.
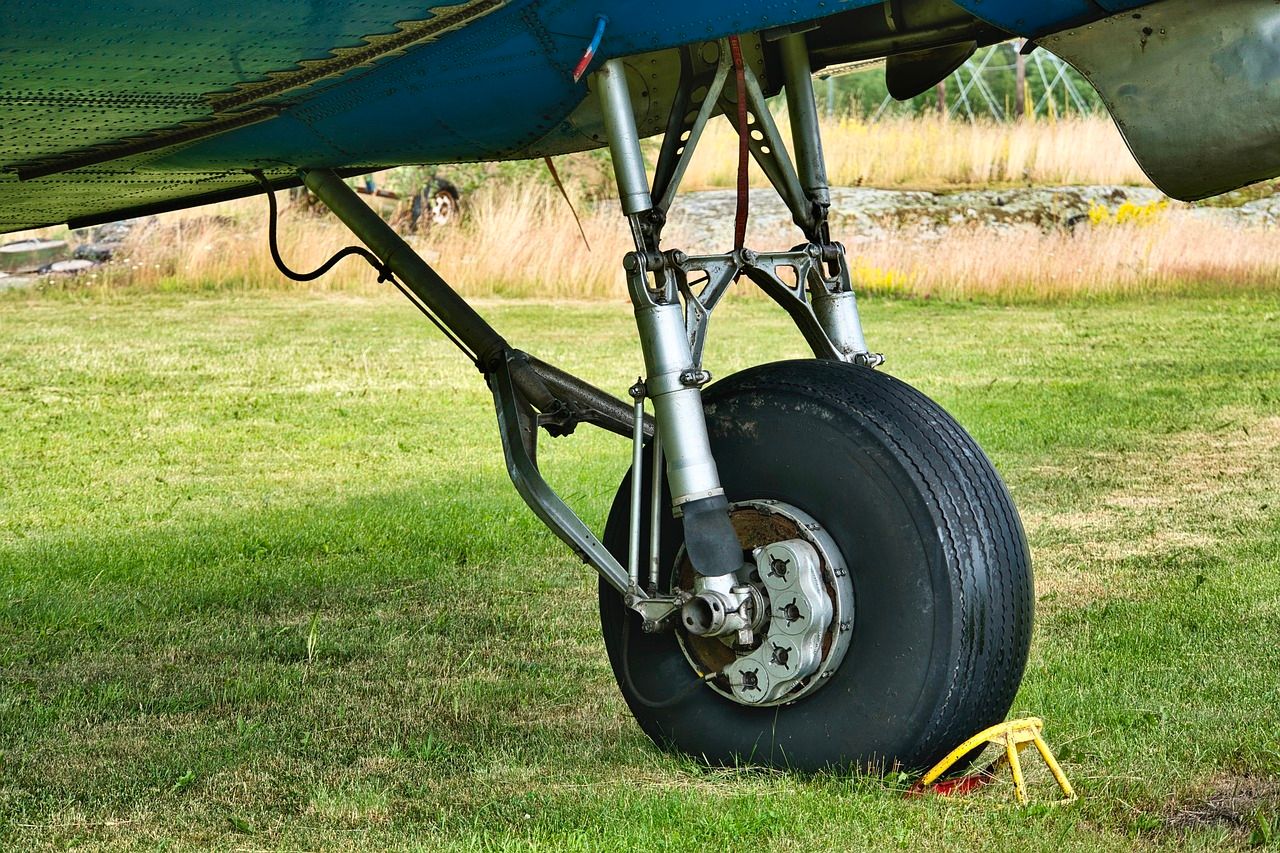
Pit Furnaces
Designed for long, vertically loaded parts, pit furnaces handle components such as turbine shafts, compressor blades, and struts. Their configuration allows for precise heat treatment of elongated parts, improving strength and fatigue resistance.
Continuous Furnaces
Ideal for mass production, continuous furnaces deliver consistent heating for smaller components like fasteners, brackets, and electronic housings. These systems support high efficiency and uniform quality in large-scale aerospace manufacturing.
Rotary Hearth Furnaces
Used for heating and forging, rotary hearth furnaces are instrumental in producing jet engine rings and discs. These systems provide uniform heating, meeting the demands of high-stress aerospace applications.
Benefits of Industrial Furnaces in Aerospace
- Precision: Industrial furnaces offer unmatched control over heating rates, temperature uniformity, and atmospheric conditions, ensuring consistent results.
- Scalability: Modern furnace systems handle both prototyping and mass production, enabling flexibility in aerospace manufacturing.
- Material Optimization: Advanced heat-treating equipment improves material properties, such as mechanical strength, thermal resistance, and corrosion resistance.
The Future of Industrial Furnaces in Aerospace
With the rise of Industry 4.0, industrial furnaces are becoming smarter and more efficient. Innovations such as real-time monitoring, predictive maintenance, and AI-driven optimization are revolutionizing aerospace manufacturing. Additionally, energy-efficient furnace technologies are aligning with the industry's sustainability goals, reducing environmental impact.
As a cornerstone of aerospace innovation, industrial furnaces empower manufacturers to push the boundaries of technology. By enhancing the properties of high-performance materials, these high-temperature instruments contribute to safer, more efficient, and ground-breaking aerospace advancements. As the industry evolves, so will the furnaces and heat-treating equipment that drive its success.