When most people think of pharmaceutical laboratories, images of microscopes, test tubes, and chemical solutions often come to mind. What’s less known is the vital role high-temperature furnaces play in pharmaceutical research and manufacturing. These precision-engineered devices operate at elevated temperatures and are essential for a wide range of processes that demand accuracy, cleanliness, and consistency.
In this blog, we’ll explore how pharmaceutical labs utilize high-temperature furnaces, their specific applications, and why these tools are indispensable to the development of safe and effective medications.
Why High-Temperature Furnaces Matter in Pharma
Pharmaceutical research and production require stringent controls to ensure purity, efficacy, and regulatory compliance. High-temperature furnaces provide:
- Stable thermal environments
- Controlled atmosphere heating
- Precise temperature uniformity
- Contaminant-free processing
These features are critical when working with sensitive chemical compounds, performing material testing, or preparing equipment for sterile environments.

Key Applications of Furnaces in Pharmaceutical Labs
High-temperature furnaces are not just high-heat devices—they're precision instruments that support critical pharmaceutical lab functions. Here are some of the primary ways high-temperature furnaces are applied in pharmaceutical laboratories:
1. Loss on Ignition (LOI) Testing
Loss on Ignition (LOI) is a commonly used analytical method for measuring the quantity of volatile components like moisture, solvents, and organic materials within a sample. Pharmaceutical laboratories use Loss on Ignition (LOI) as a crucial quality control method to assess raw materials such as excipients, fillers, and active pharmaceutical ingredients.
Here’s how it works:
- A pre-weighed sample is placed in a crucible and heated in a furnace to a specified high temperature (usually between 550°C–1000°C).
- After a set duration, the crucible is cooled and reweighed.
- The weight loss corresponds to the volatile content, helping identify inconsistencies or contamination.
This method is critical for ensuring product purity and consistency, especially when working with hygroscopic or thermally sensitive substances.
2. Ash Content Analysis
Ash content determination is another essential furnace-based technique. In this method, the sample is subjected to high temperatures inside a muffle furnace, which burns off all organic substances and isolates the remaining inorganic ash. This is crucial for:
- Detecting foreign inorganic materials
- Evaluating excipient purity
- Verifying compliance with USP (United States Pharmacopeia) and other pharmacopeial guidelines
This process helps ensure that raw materials meet stringent specifications, especially for injectables, where even trace inorganic residues can cause safety issues.
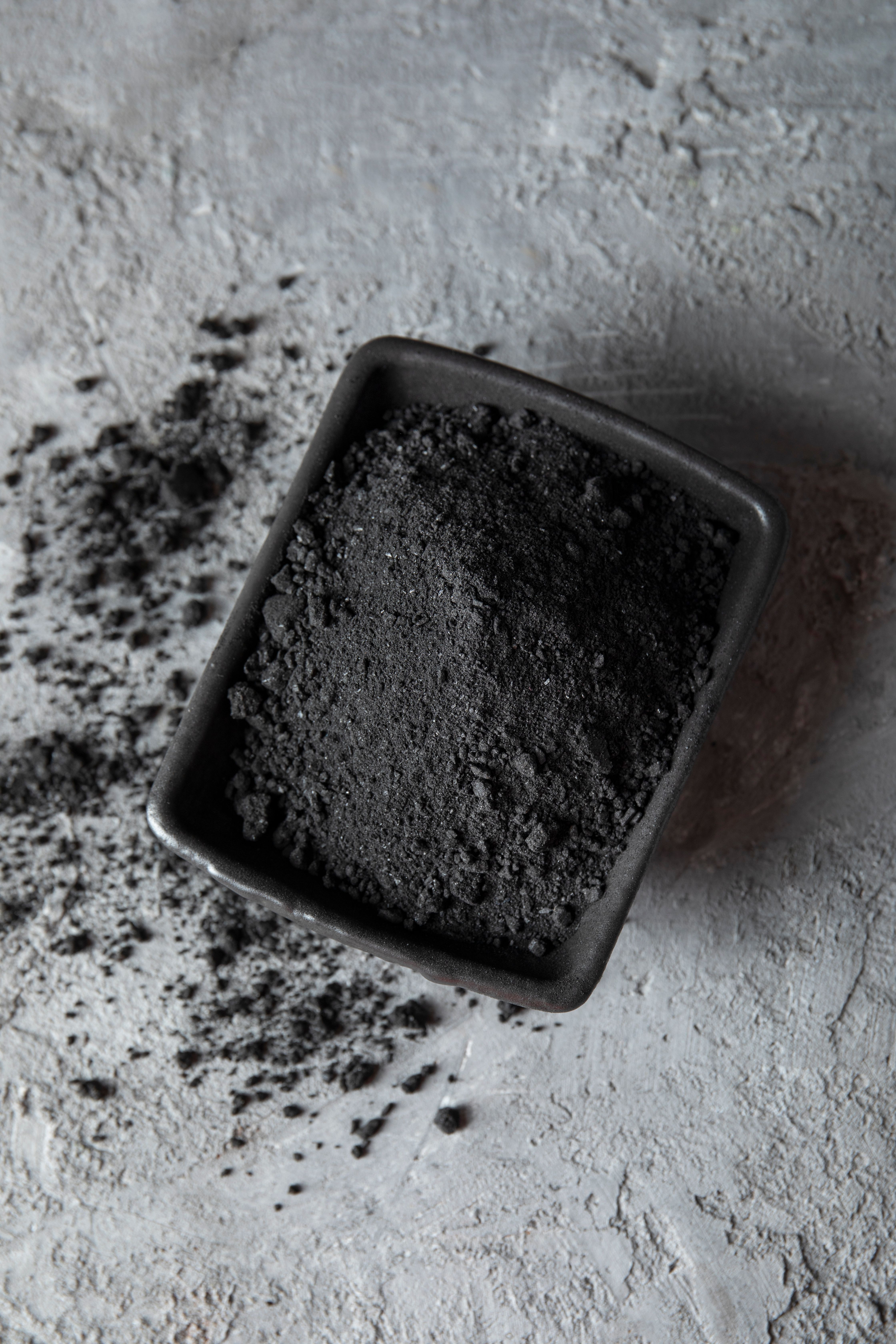
3. Sterilization of Laboratory Equipment
While autoclaves are widely used for sterilization, dry heat sterilization using high-temperature furnaces offers distinct advantages for specific materials:
- Glassware and metal tools that can tolerate high temperatures
- Materials that are sensitive to moisture or incompatible with steam sterilization methods
- Instruments used in sensitive analytical work where water vapor could interfere with results
Sterilization furnaces generally function at temperatures between 160°C and 180°C for extended periods to effectively eliminate all microbial life. This method is especially valued for its simplicity, reliability, and ability to avoid moisture-induced degradation.
4. Thermal Decomposition and Stability Studies
Understanding how pharmaceutical compounds behave under thermal stress is crucial for:
- Determining shelf life
- Ensuring that pharmaceutical compounds retain their integrity during processing, transportation, and storage conditions
- Identifying degradation products or reaction byproducts
Furnaces provide a controlled environment to simulate high-heat exposure over time. This data informs regulatory documentation, formulation adjustments, and packaging design, ensuring drug safety and performance in real-world conditions.
Some labs also use this data for accelerated aging tests, where samples are exposed to higher-than-normal temperatures to simulate long-term storage in a shorter time.
5. Sintering and Calcination of Carriers and Catalysts
Advanced pharmaceutical research increasingly involves drug delivery systems that use carrier particles or catalytic agents to enhance bioavailability. Furnaces are used to:
- Sinter ceramic-based drug carriers to achieve optimal porosity and structure
- Calcine catalyst supports to increase surface area and remove unwanted compounds
Modern laboratory furnaces are engineered to deliver accurate temperature management, controlled dwell times, and regulated atmospheres essential for these processes.
Sintering and calcination are also used in nanotechnology-based formulations and controlled-release systems, making them vital in cutting-edge pharma R&D.
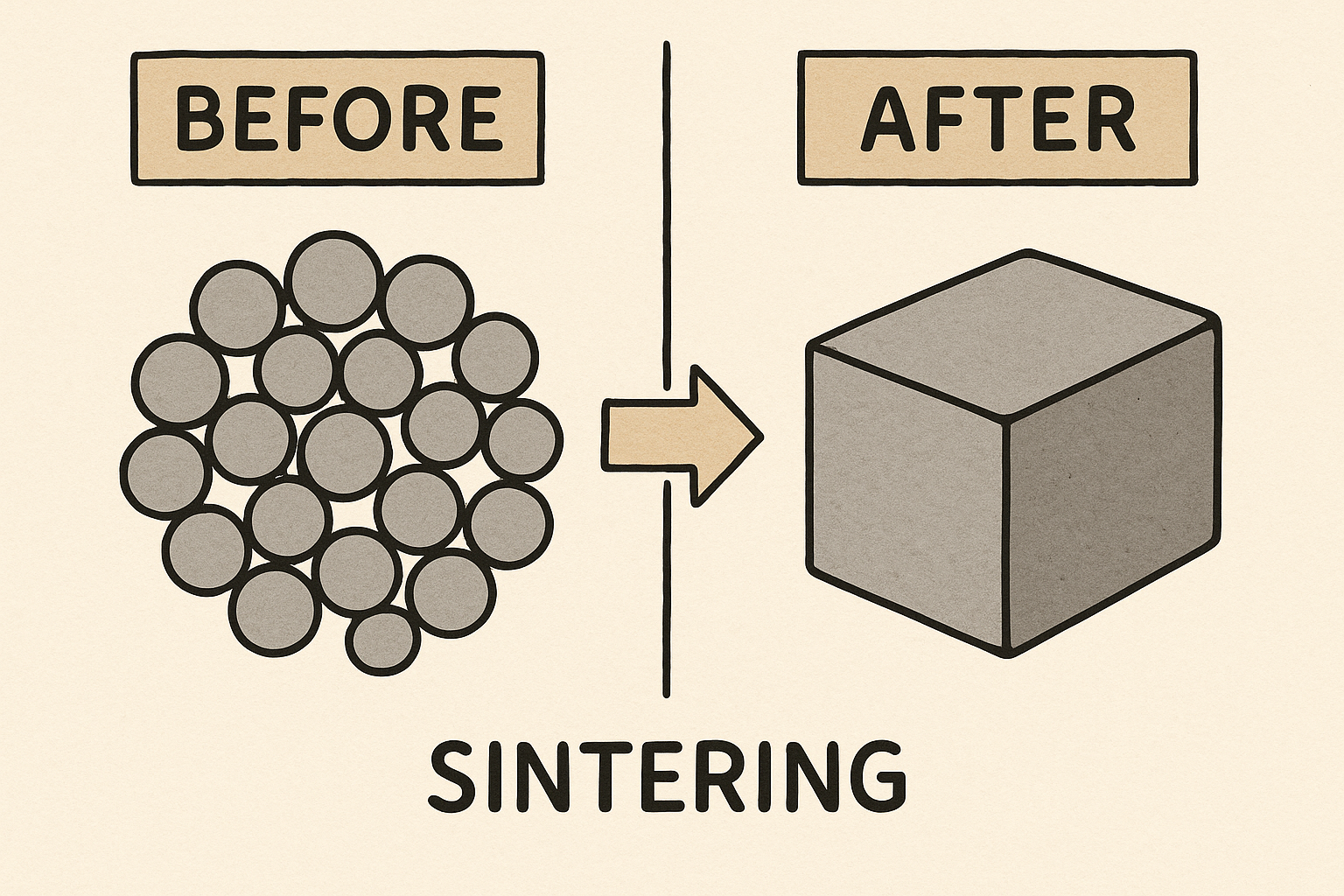
Specialized Furnace Features for Pharma Use
Because pharmaceutical processes require strict contamination control and repeatability, lab furnaces for this sector often include:
- Chambers made from clean, non-reactive materials such as high-grade ceramic or alumina to prevent contamination
- Programmable temperature profiles
- Rapid heating and cooling rates
- Air or inert gas atmosphere controls
These features help ensure that the heating process doesn’t compromise the quality or safety of pharmaceutical compounds.
Regulatory Compliance and Validation
Pharmaceutical labs must adhere to GMP (Good Manufacturing Practice) and FDA or USP standards. Furnace-based processes, especially those involved in product testing or preparation, must be:
- Validated
- Repeatable
- Documented
Modern furnaces often include data logging, remote monitoring, and audit trail capabilities to support compliance.
While they might not be as visible as beakers and balances, high-temperature furnaces are foundational to many pharmaceutical lab operations. From quality testing to material processing and sterilization, these tools help ensure that drugs are safe, consistent, and effective.
As pharmaceutical technologies continue to evolve, so too will the role of precision lab equipment like high-temperature furnaces—making them a critical component of today’s and tomorrow’s pharmaceutical innovation.