The dental industry is experiencing a wave of transformation as digital dentistry takes centre stage. Technologies such as Computer-Aided Design/Manufacturing (CAD/CAM), 3D printing, and digital imaging are not only streamlining processes but also enhancing precision and efficiency. Amidst this evolution, dental furnaces—essential tools for sintering, glazing, and firing dental prosthetics—are undergoing remarkable advancements to align with these modern workflows.
The Role of Dental Furnaces in Digital Dentistry
Dental furnaces play a critical role in the fabrication of prosthetics such as crowns, bridges, and veneers. After designs are created using CAD software and materials are shaped through CAM milling or 3D printing, furnaces complete the process by sintering and glazing the restorations. This ensures the prosthetics achieve the desired strength, durability, and aesthetic finish.
Key Advancements in Dental Furnace Technology
1. Material Versatility
Contemporary dental furnaces are engineered to handle a wide variety of materials such as zirconia, lithium disilicate, and hybrid ceramics. This adaptability is essential as CAD/CAM technologies bring forth new materials with specific temperature and processing needs. For example:
- Zirconia: Requires high-temperature sintering cycles up to 1600°C.
- Lithium Disilicate: Demands precise cooling to prevent micro-cracking during crystallization.
2. Enhanced Speed and Efficiency
One of the critical demands of dental labs is faster turnaround times. High-speed sintering furnaces now enable processing of zirconia prosthetics in less than two hours, a significant improvement over traditional cycle. These advancements allow labs to deliver same-day restorations, a key advantage in modern dental practices.
3. Smart Technology and IoT Integration
Next-generation dental furnaces are equipped with smart features, including:
- Remote Monitoring: IoT-enabled systems let technicians’ control and track furnace operations from mobile devices.
- Pre-Set Programs: Furnaces now come with automated cycles tailored to specific materials, reducing the risk of human error.
- Diagnostics and Maintenance Alerts: Smart furnaces provide real-time alerts for maintenance, minimizing downtime.
4. Sustainability and Energy Efficiency
As dental labs adopt greener practices, manufacturers are developing furnaces with energy-efficient designs. These eco-friendly models not only reduce operational costs but also align with global sustainability goals.
Integration with CAD/CAM Workflows
The compatibility of modern furnaces with CAD/CAM workflows has transformed dental prosthetics production. By seamlessly integrating with milling machines and 3D printers, these furnaces ensure smooth transitions between design, production, and finishing stages. This integration reduces errors, enhances precision, and enables technicians to achieve optimal results consistently.
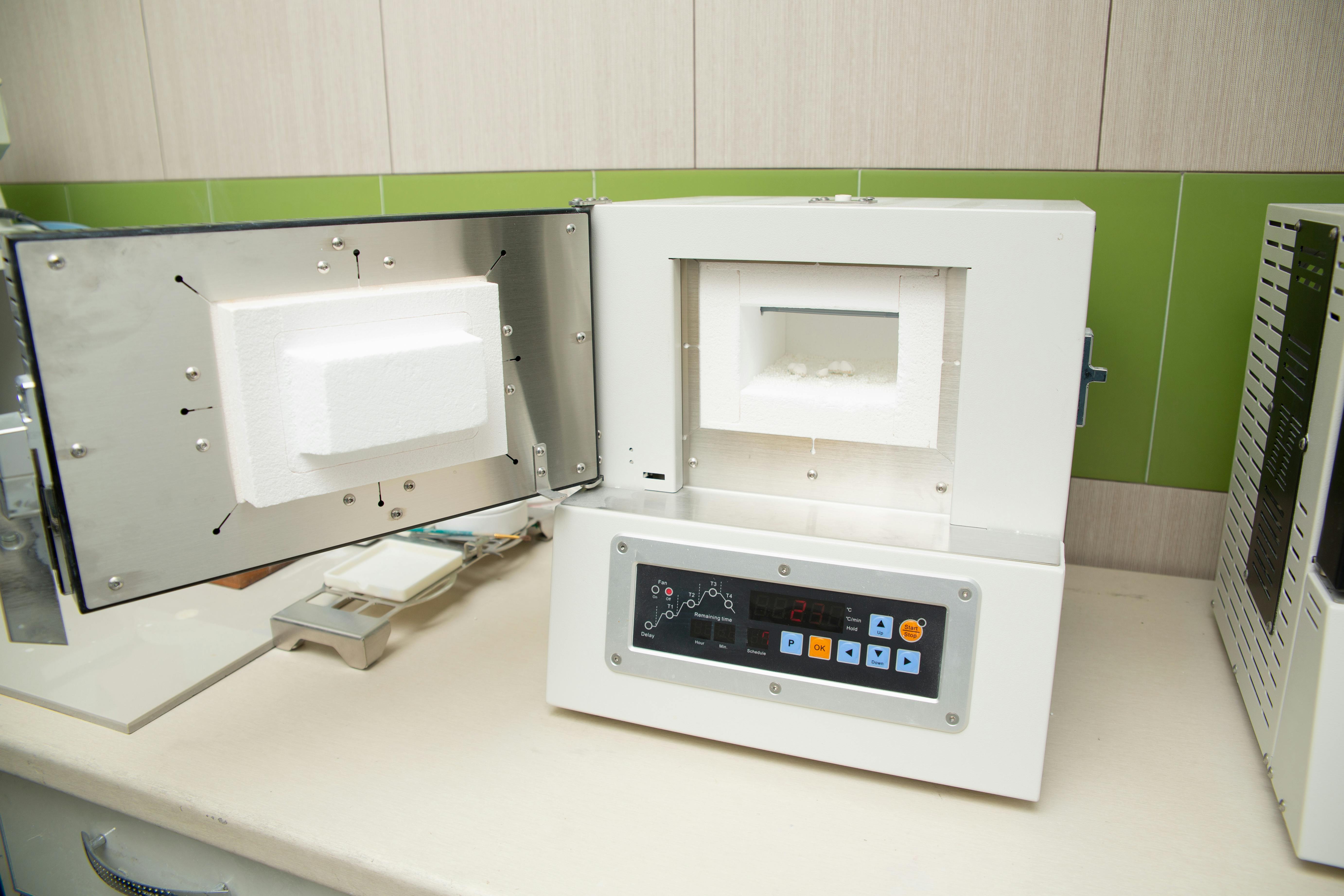
Future Trends in Dental Furnaces
The evolution of dental furnaces is set to continue, with trends such as:
- Hybrid Systems: Devices that combine sintering, glazing, and additional functions into one compact unit.
- AI-Driven Processes: Artificial intelligence will likely optimize firing cycles based on material properties and historical data.
- Customizable Interfaces: User-friendly systems with adaptable settings for diverse lab needs.
As digital dentistry continues to redefine the dental industry, furnaces are evolving to meet these new challenges and opportunities. With advanced features like smart technology, material versatility, and faster processing times, dental furnaces are not only keeping pace but also driving the future of dental prosthetics production. For dental labs and clinics, investing in state-of-the-art furnaces is a step toward efficiency, precision, and patient satisfaction.