As the demand for sustainable energy solutions rises, biomass pyrolysis furnaces are gaining importance in transforming organic waste into valuable products. To understand their effectiveness and potential, it's important to explore the essential components that facilitate this process. Here’s an in-depth breakdown:
1. Feedstock Hopper
The feedstock hopper is where raw biomass is introduced into the system. Its design ensures a steady and controlled flow of material into the reactor chamber.
Key Functions:
- Regulated Feeding: Prevents fluctuations in biomass supply, which could disrupt the pyrolysis process.
- Pre-processing Capabilities: Some hoppers include features like drying or shredding to reduce moisture or particle size, enhancing pyrolysis efficiency.
·Flow Control Devices: Valves or auger screws regulate the steady movement of feedstock, helping to prevent blockages and material build-up.
Why It’s Important: The characteristics and consistency of the feedstock significantly influence the quality and output of the pyrolysis products. A steady feedstock supply helps maintain uniform heating and reliable system operation.
2. Pyrolysis Reactor Chamber
The reactor chamber is where the biomass undergoes pyrolysis. In this oxygen-free environment, the material is heated to 350°C–600°C, breaking it down chemically without combustion.
Types of Reactor Designs:
- Fixed-bed Reactors: Simple and cost-effective, best suited for batch processing and small-scale applications.
- Fluidized-bed Reactors: Use high-speed air or gas to suspend biomass, allowing for uniform heat distribution and faster reactions.
- Rotary Kilns: Continuously rotate to mix biomass, ideal for handling a variety of feedstocks.
- Auger Reactors: Utilize a rotating screw to move biomass through a heated tube, allowing precise control over residence time.
Core Purpose: This chamber is vital for determining how efficiently biomass is converted into biochar, bio-oil, and syngas. Factors such as temperature, heating rate, and residence time are carefully controlled to maximize output.
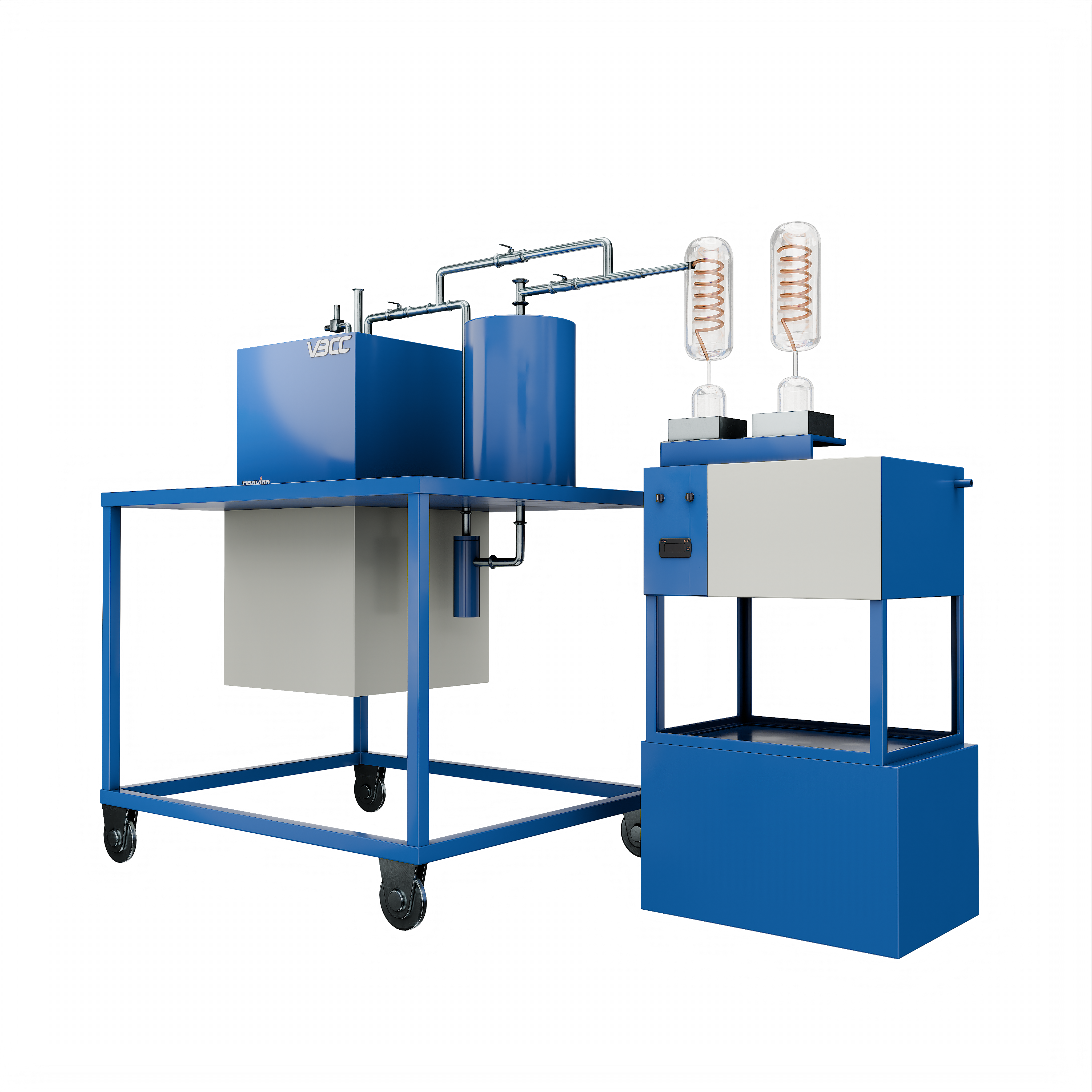
3. Heat Source & Heat Transfer System
Pyrolysis requires a steady heat source to initiate and maintain the reaction.
Heat Sources:
- Electric Heaters: Clean and adjustable but less efficient on a large scale.
- Gas Burners: Often powered by the syngas produced during pyrolysis, enhancing energy efficiency.
- Indirect Heating: Prevents oxygen intrusion by using an external chamber or pipe to deliver heat safely.
Heat Transfer: Effective heat distribution is crucial for achieving optimal pyrolysis. Inadequate heat transfer can lead to:
- Incomplete pyrolysis
- Reduced biochar quality
- Tar formation
Some systems use thermal insulation and heat recuperators to save and reuse energy, reducing operational costs.
4. Condensation & Cooling Unit
After being released from the reactor, the vapours need rapid cooling to condense bio-oil and separate non-condensable gases.
Components:
- Condensers or Chillers: Quickly cool gases to convert heavier hydrocarbons into bio-oil.
- Cyclones or Separators: Clean the gases by removing ash or tar particles before cooling.
- Oil Storage Tanks: Store the recovered bio-oil for use as fuel or in chemical manufacturing.
Why It’s Important: Efficient condensation maximizes liquid yields and prevents tar contamination in subsequent systems.
5. Biochar Collection System
Biochar is a solid by-product formed during pyrolysis, typically collected from the bottom of the reactor or a designated area.
Collection Systems:
- Manual Removal: In smaller systems, biochar is removed manually after each batch.
- Automated Discharge: In continuous systems, screw conveyors or hoppers automatically discharge biochar into collection bins.
Applications:
- Soil amendment for improving nutrient retention
- Tool for carbon sequestration
- Filtration and remediation media
- Solid fuel for heating or cooking
Proper collection systems ensure safety, reduce exposure to dust, and maintain reactor efficiency.
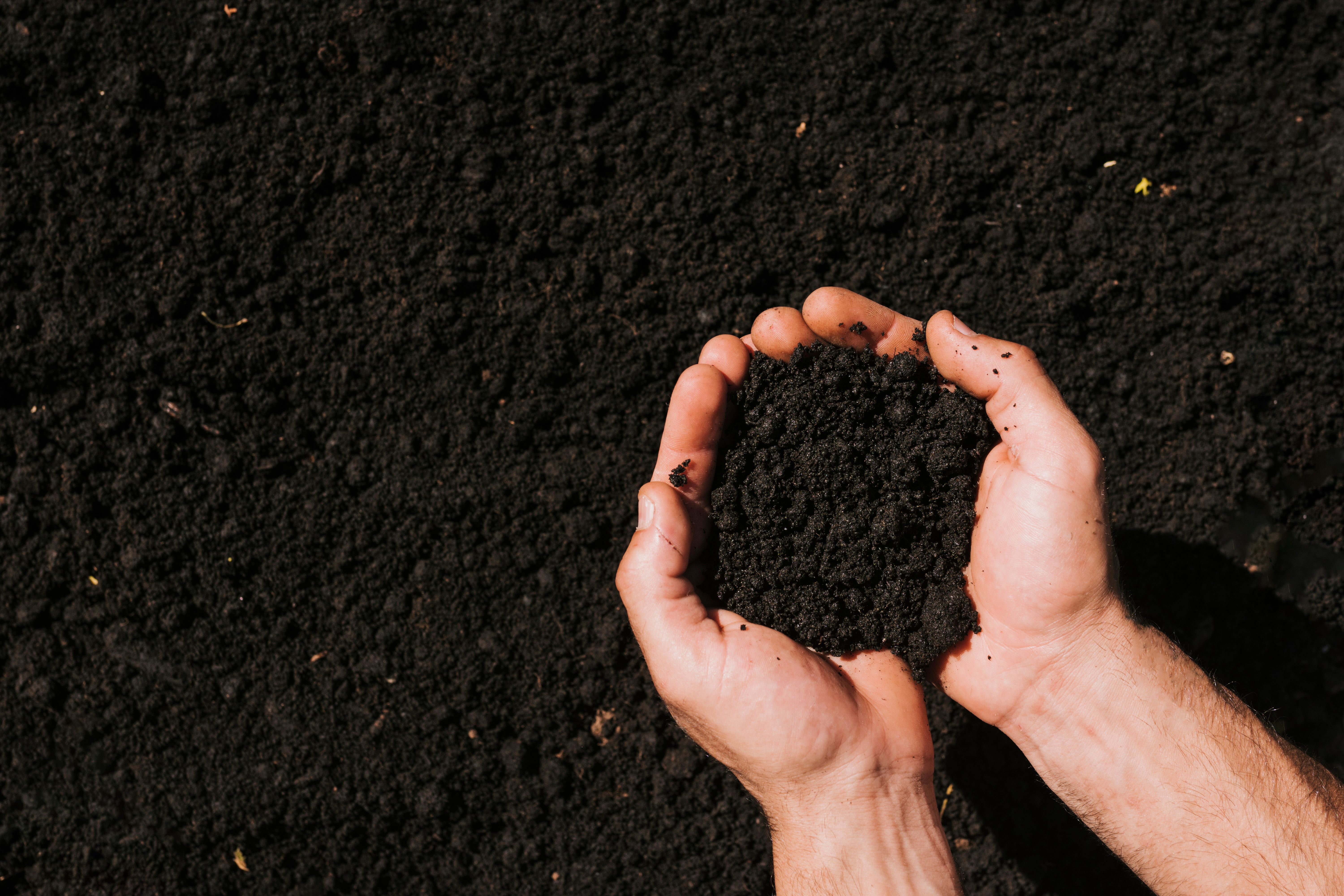
6. Gas Clean-Up & Flue Management
Non-condensable gases (syngas) often contain particulates, tars, and acidic gases that must be cleaned before they can be reused or safely released.
Components:
- Cyclone Separators: Remove large particulates and ash.
- Scrubbers: Eliminate acidic gases like hydrochloric acid (HCl) or sulfur dioxide (SO₂).
- Filters or Activated Carbon Beds: Capture smaller particles, heavy metals, or remaining tars.
Environmental Importance: Cleaning the flue gases helps prevent air pollution, ensures regulatory compliance, and allows the syngas to be used for:
- Heating
- Electricity generation
- Fuel cells
7. Control & Automation System (Optional)
To efficiently manage the complex pyrolysis process, modern furnaces often include automated systems and sensors.
Features:
- Temperature Sensors: Ensure the reactor operates within the optimal pyrolysis temperature range.
- Flow Rate Monitors: Regulate feedstock supply and air/gas flow.
- Pressure Controls: Prevent system overloads or leaks.
- Programmable Logic Controllers (PLCs): Automate processes and respond to real-time data.
Benefits:
- Consistent product quality
- Enhanced safety
- Improved energy efficiency
- Remote monitoring for large-scale or off-grid systems
Biomass pyrolysis furnaces are sophisticated thermochemical systems that transform waste into useful resources. Every component, from feeding and heating to gas purification and product collection, is crucial to the process. Comprehending how these elements function together is key for:
- Designing a new furnace
- Operating a system for rural applications
- Conducting research on renewable energy systems