In the fields of materials science, structural engineering, and high-performance manufacturing, precise high-temperature testing is essential. Whether simulating fire exposure in concrete, testing the thermal durability of alloys, or curing advanced ceramics, researchers rely on equipment that offers both accuracy and uniformity. That’s where the three-zone furnace becomes a preferred choice.
What Is a Three-Zone Furnace?
A three-zone furnace is a type of laboratory or industrial furnace equipped with three independently controlled heating zones—typically left, centre, and right. These zones are carefully programmed to maintain uniform temperatures across the entire length of the chamber. This configuration helps minimize temperature differences along the chamber, providing the sample with evenly distributed heat throughout the process.
Why Temperature Uniformity Matters in Research
Uniform heating is critical when studying:
- Thermal behaviour of materials
- Phase transitions
- Creep and fatigue under high heat
- Fire resistance of structural components
For instance, when evaluating the performance of reinforced concrete under simulated fire conditions, inconsistent temperature distribution can distort findings, potentially misrepresenting how the material responds to stress or fails. Three-zone furnaces help ensure consistent heat exposure, making experimental results more dependable and easier to replicate.

Key Advantages for Researchers
Research involving high temperatures requires heating equipment that offers not just durability and reliability, but also precision, adaptability, and stable performance. The three-zone furnace effectively fulfils these requirements, which is why it is commonly used in cutting-edge research environments. Below are some of the key benefits, making it a preferred choice in advanced research settings:
Precise Temperature Control
One of the most significant benefits of a three-zone furnace is its ability to maintain highly controlled thermal environments. Each of the three zones—left, centre, and right—is independently regulated using advanced controllers (typically PID-based), allowing researchers to:
- Match temperatures across all zones for uniform heat distribution, or
- Deliberately set a thermal gradient when experiments require differential heating.
This level of control is essential for replicating real-world thermal conditions such as those encountered in fire exposure, geothermal environments, or industrial processing. It also supports the detailed study of heat-induced transformations like phase changes, diffusion, and material creep.
Consistent Test Conditions
Unlike single-zone furnaces, which often suffer from temperature fluctuations and uneven heating, three-zone furnaces provide stable and repeatable thermal conditions across the heating chamber. The result is:
- Reduced temperature variations that could affect the material's behaviour
- Improved reproducibility across multiple tests
- Greater accuracy in determining thermal thresholds (e.g., failure points or ignition temperatures)
This consistency ensures that researchers can trust the data generated, especially when working with sensitive materials or conducting long-duration experiments.
Versatile Testing Capabilities
The three-zone furnace is highly versatile, making it suitable for a broad array of applications. It is frequently used in both fundamental and applied research, including:
- Heat treatment: for enhancing or altering material properties like hardness, ductility, and grain structure
- Stress relaxation: observing how materials relieve internal stresses at elevated temperatures
- Sintering: facilitating the fusion of powder particles in ceramics or metals without melting them completely
- Fire testing: simulating fire exposure scenarios in structural engineering, especially for concrete, steel, and composites
- Thermo-mechanical studies: combining heat and mechanical loads to test materials under service-like conditions
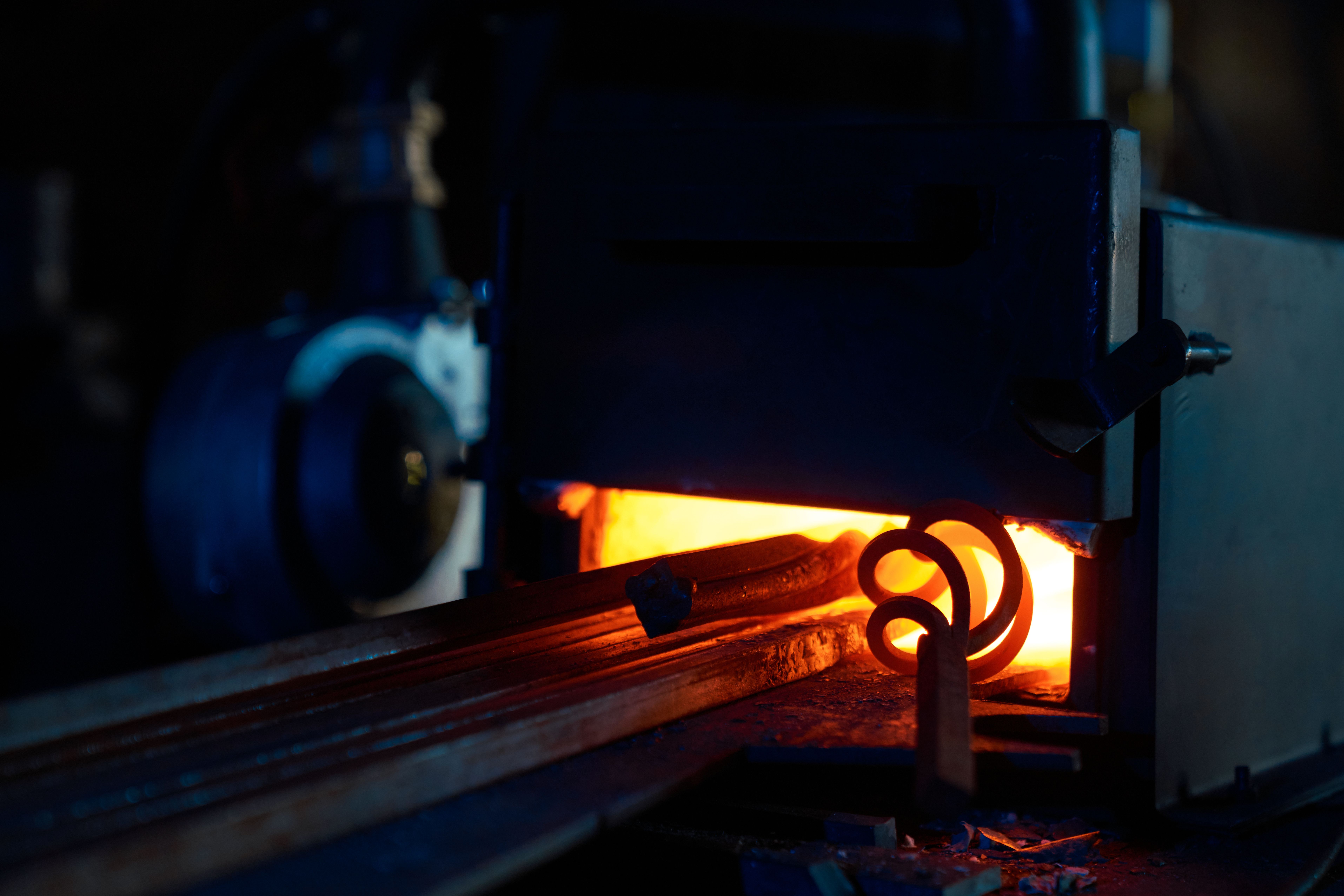
Whether you're studying polymers, ceramics, metals, advanced composites, or even concrete, a three-zone furnace provides the adaptability needed for diverse test regimes.
Programmable Logic Control (PLC)
Modern three-zone furnaces come equipped with intelligent digital control systems, enhancing both precision and usability. Key features include:
- Programmable temperature profiles: Users can set complex thermal cycles involving ramps, dwells, and cool-down stages
- Continuous data tracking and recording: Essential for capturing and analysing temperature trends over time
- User-friendly interfaces: Touchscreens and software interfaces make it easier to operate the furnace and troubleshoot issues
- Safety integration: Features like over-temperature alarms, interlocks, and emergency shut-offs improve lab safety during unattended operations
This level of automation and control is vital for modern research practices, where data integrity, repeatability, and documentation are central to publishing, quality assurance, and peer review.
Broader Impact Across Research Fields
Three-zone furnaces are highly adaptable tools, valued across various fields for their accuracy and flexibility:
- Materials research for discovering heat-resistant alloys and composites
- Academic labs focused on advanced ceramics and energy materials
- Industrial research and development in sectors such as aerospace, automotive, and electronics
- Fire safety engineering and standards testing
In an era where material performance and safety are paramount, researchers need tools that match the complexity of their questions. The three-zone furnace stands out as a vital instrument, offering uniform heating, precision control, and versatility. Whether you're conducting fundamental research or applied testing, it's clear why this equipment has become a cornerstone in high-temperature laboratories.