Magnesium alloys are gaining traction in industries like automotive and aerospace due to their excellent strength-to-weight ratio and superior castability. One of the most economical and scalable methods for fabricating metal matrix composites (MMCs) with magnesium as the matrix is stir casting. This blog walks you through the step-by-step procedure of stir casting magnesium alloys, highlighting the key considerations and techniques to ensure optimal results.
What is Stir Casting?
Stir casting is a liquid-state technique used to incorporate reinforcements (like ceramic particles) into molten metal. A mechanical stirrer creates a vortex in the molten metal, allowing uniform distribution of the reinforcing material.
Safety Precautions
Working with molten magnesium is hazardous due to its flammability and reactivity. Always use proper protective gear, work in a well-ventilated area, and handle with high-temperature-rated tools. Keep a Class D fire extinguisher or dry sand nearby, as water should never be used on magnesium fires.
Equipment & Materials
Stir casting magnesium alloys requires essential materials and specialized equipment. Magnesium alloy ingots like AZ91 or AM60 serve as the base, while reinforcements such as SiC, Al₂O₃, or CNTs enhance mechanical properties. A protective gas (CO₂ + SF₆ or argon) is used to prevent oxidation during melting. The process needs a graphite or ceramic crucible and a furnace—either resistance or induction—for controlled heating. A mechanical stirrer with a graphite or stainless-steel impeller creates the vortex needed for mixing. Reinforcement particles are preheated to improve wetting, and a thermocouple helps monitor melt temperature. Finally, preheated metal or sand molds are used for casting the molten composite.
Step-by-Step Stir Casting Procedure
Step 1: Preheating the Reinforcements
The first and one of the most critical steps in stir casting magnesium composites is the preheating of reinforcement particles. Reinforcements, such as silicon carbide (SiC), aluminium oxide (Al₂O₃), or carbon nanotubes (CNTs), often come with surface moisture or contaminants that can cause unwanted reactions during casting. To address this, the particles are typically heated to a temperature range of 300°C to 500°C. This not only removes moisture but also improves their wettability with molten magnesium, which naturally has poor wetting behaviour with most ceramic reinforcements. Preheating ensures a cleaner interface, reduces the risk of gas entrapment, and helps in achieving uniform dispersion later in the process.
Step 2: Melting the Magnesium Alloy
Next, the magnesium alloy is placed into a graphite or ceramic crucible and gradually heated to a temperature range of 650°C to 700°C using either a resistance furnace or an induction furnace. Magnesium is highly reactive, especially at elevated temperatures, so oxidation is a major concern. To prevent this, a protective atmosphere must be maintained throughout the melting process. Typically, a gas mixture of carbon dioxide and sulfur hexafluoride (CO₂ + SF₆) is used, or alternatively, argon gas can be employed as an inert shielding gas. Maintaining this protective atmosphere minimizes oxidation, prevents burning, and ensures the integrity of the molten metal.
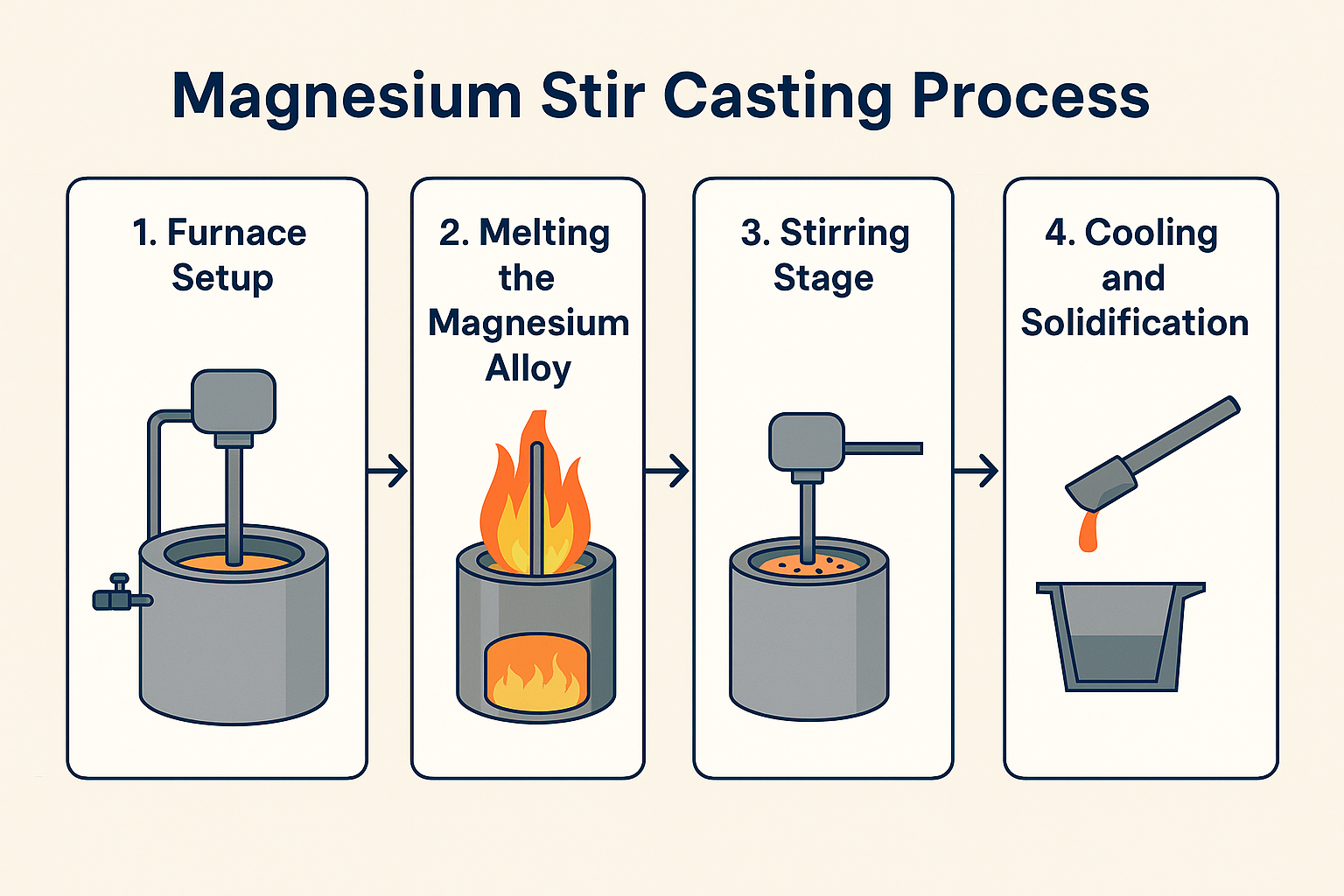
Step 3: Initiating Stirring
Once the alloy has fully melted and reached a stable temperature, mechanical stirring is initiated. A stirrer with a graphite or stainless-steel impeller is lowered into the melt and rotated at a controlled speed—usually between 300 and 600 revolutions per minute (rpm). The purpose of stirring is to create a strong vortex in the molten metal, which facilitates the uniform incorporation of reinforcement particles. The depth and intensity of the vortex are carefully adjusted to avoid drawing air into the melt, which can cause porosity. The quality of the vortex directly influences the uniformity of the final composite.
Step 4: Introducing Reinforcements
With the vortex well-formed, the preheated reinforcement particles are gradually introduced into the centre of the melt. This must be done slowly and steadily to ensure even distribution and to avoid particle agglomeration or settling. Stirring is continued for about 5 to 10 minutes after all the particles are added. This allows sufficient time for the particles to disperse uniformly throughout the matrix. It’s essential to avoid vigorous or turbulent stirring, as it may introduce gas into the melt and lead to defects such as porosity or unwanted oxide inclusions.
Step 5: Degassing and Fluxing (Optional)
Depending on the alloy system and the quality of the melt, degassing and fluxing might be necessary. Degassing agents can be introduced to remove dissolved gases like hydrogen, which are common in magnesium melts and can lead to porosity in the final casting. Fluxes may also be used to remove impurities from the surface of the molten metal and improve the cleanliness of the composite. While not always mandatory, these steps contribute significantly to enhancing the mechanical properties and structural integrity of the final product.
Step 6: Pouring the Composite
Once the stirring process is complete and the melt is cleaned, the molten composite is poured into preheated molds. Preheating the molds to around 200°C helps reduce thermal shock and prevents premature solidification at the mold surface. Care should be taken to pour the metal steadily and avoid turbulence, which could disrupt the even distribution of reinforcement particles. Controlled cooling allows the casting to solidify uniformly, minimizing internal stresses and defects.
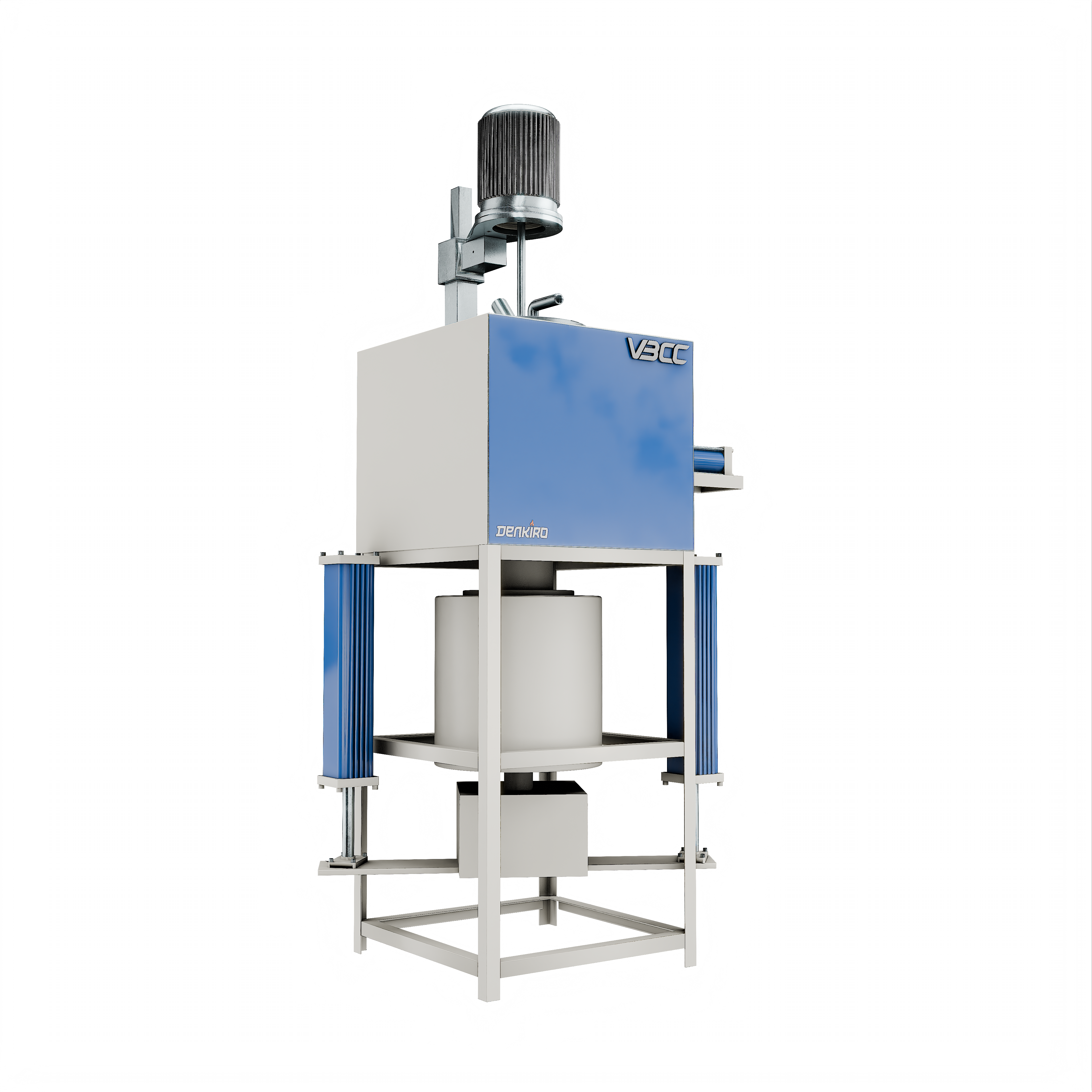
Step 7: Post-Processing
After solidification, the casting is removed from the mold and may undergo further processing such as machining, heat treatment, or surface finishing, depending on the desired application. At this stage, quality assessments such as microstructural analysis, mechanical testing, and non-destructive inspection may also be carried out to evaluate particle distribution, bonding, porosity levels, and mechanical performance. These tests help in verifying the success of the stir casting process and ensuring that the composite meets the intended design criteria.
Tips for Better Results
- Wettability is key: Magnesium doesn’t naturally wet most reinforcements—pre-treatments or wetting agents can help.
- Uniform particle distribution: Ensure steady stirring and proper vortex depth.
- Control oxidation: Always use protective gases and avoid prolonged exposure of molten magnesium to air.
Stir casting offers a cost-effective and scalable approach to producing magnesium matrix composites with enhanced mechanical properties. With careful control over processing parameters, material selection, and safety precautions, high-quality MMCs can be consistently fabricated.
Whether you're working in a research lab or an industrial setting, mastering this method opens up new possibilities in lightweight materials engineering.